Flowserve APKD User Manual
Page 32
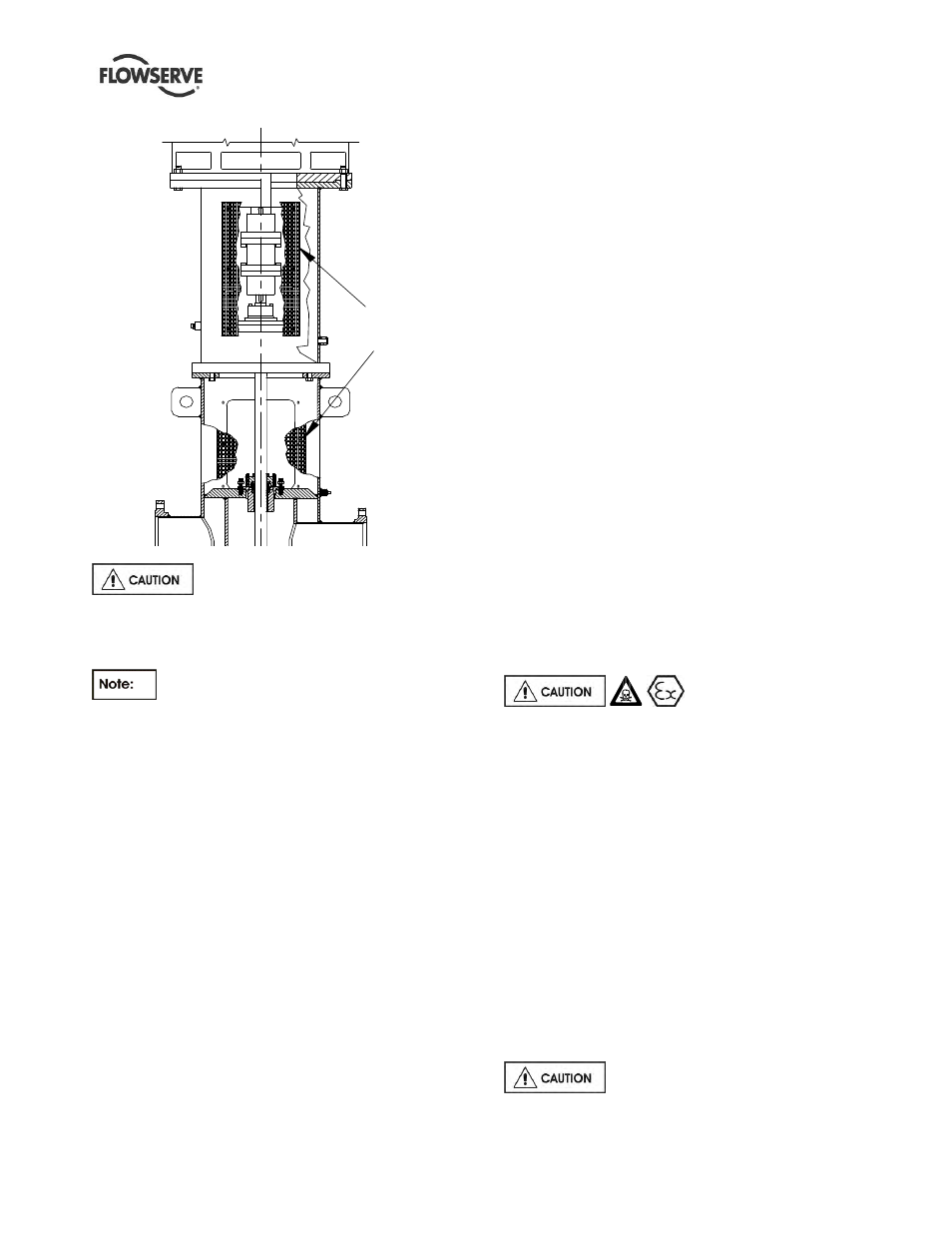
APKD DOUBLE-CASE, DOUBLE-SUCTION USER INSTRUCTIONS 26999903 07-13
Page 32 of 55
flowserve.com
Figure 5.3
G U AR D S
IN STALLED
After initial startup, pre-lubrication
of the mechanical seal will usually not be required
as enough liquid will remain in the seal chamber for
subsequent startup lubrication.
A screen guard is furnished with all
pumps having a two-piece headshaft or an
adjustable flanged coupling. This screen must be
secured in place prior to pump startup to prevent
possible contact with rotating parts. Typical
arrangement is shown in section 5.7.1.1.
5.7.2 Stuffing
box
adjustment
On the initial starting it is very important that the
packing not be tightened excessively. New packing
must be run in properly to prevent damage to the
shaft and shortening of the packing life.
The stuffing box must be allowed to leak for proper
operation. The proper amount of leakage can be
determined by checking the temperature of the
leakage, this should be cool or just lukewarm - NOT
HOT - usually 40 to 60 drops per minute will be
adequate.
When adjusting the packing gland, bring both nuts
down evenly and in small steps until the leakage is
reduced as required. The nuts should only be
tightened about one half turn at a time at 20 to 30
minute intervals to allow the packing to "run-in".
Under proper operation, a packing set will last a long
time. Occasionally a new ring of packing will need
to be added to keep the box full.
After adding two or three rings of packing, or when
proper adjustment cannot be achieved, the stuffing
box should be cleaned completely of all old packing
and re-packed.
5.7.3
Open shaft lubrication before startup
Open lineshaft bearings are lubricated by the
pumped fluid on short-coupled units less than 15 m
(50 ft) long and usually do not require pre- or post-
lubrication.
5.7.4 Initial
Starting
a) If the discharge line has a valve in it, it should
be partially open for initial starting. The
discharge valve is intended to add sufficient
system resistance to the pump. Failure to
maintain pump flow rates within the limits of the
pump and motor could result in severe
damage.
b) Start the pump and observe the operation. If
there is any difficulty, excess noise or vibration,
stop the pump immediately and refer to the
Trouble Shooting Chart (section 7.0) to
determine the probable cause.
Observe extreme caution
when venting and or draining hazardous liquids.
Wear protective clothing in the presence of caustic,
corrosive, volatile, flammable or hot liquids. Do not
breath toxic vapors. Do not allow sparking, flames
or hot surfaces in the vicinity of the equipment.
Ensure that the unit is vented of all trapped
vapor
Open the discharge valve as desired to operate
the unit at its design conditions
Check complete pump and driver for leaks,
loose connections, or improper operation
If possible, the pump should be left running for
approximately one half hour on the initial startup,
this will allow the bearings, packing or seals, and
other parts to "run-in" and reduce the possibility of
trouble on future starts.
If abrasives or debris are present,
upon startup, the pump should be allowed to run