6 fastener torques, 7 setting impeller clearance, 8 disassembly – Flowserve APKD User Manual
Page 39
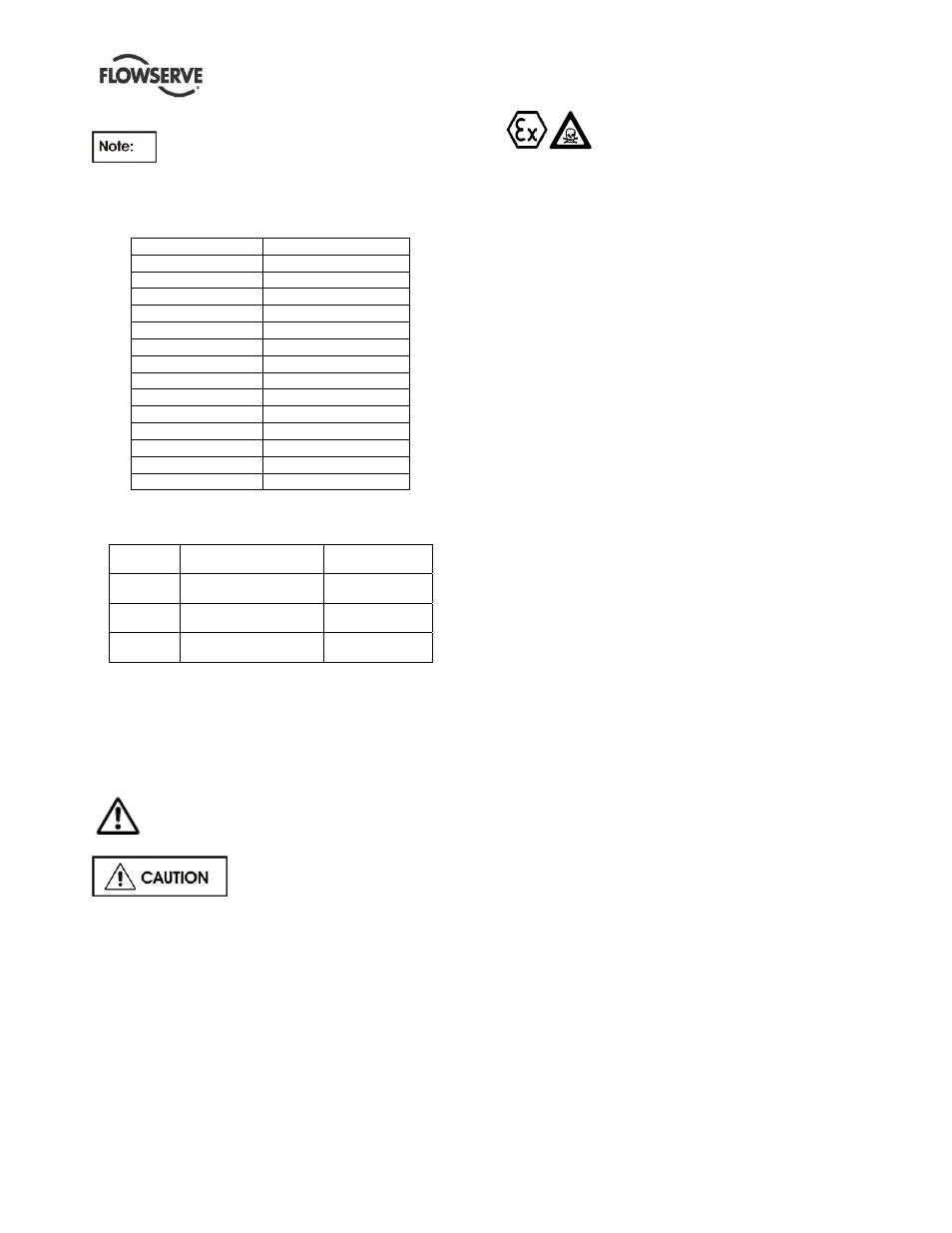
APKD DOUBLE-CASE, DOUBLE-SUCTION USER INSTRUCTIONS 26999903 07-13
Page 39 of 55
flowserve.com
6.6 Fastener
torques
Torque values shown are for standard
fasteners lubricated with high stress lubricant such
as graphite-oil, moly-disulphite, white lead, etc.
6.6.1
Fastener torques for bowl assembly
Fastener size
Torque
mm (in.)
Nm (lb
·ft)
6 (0.25)
7 (5)
8 (0.31)
14 (10)
10 (0.37)
23 (17)
11 (0.43)
37 (27)
12 (0.5)
54 (40)
15 (0.56)
81 (60)
16 (0.62)
114 (84)
19 (0.74)
183 (135)
22 (0.87)
346 (255)
25 (1.00)
502 (370)
28 (1.12)
678 (500)
32 (1.25)
902 (665)
38 (1.50)
1322 (975)
6.6.2
Torques for couplings screws
Coupling
size #
Flange diameter
mm (in.)
Nm
(lb
·ft)
1 & 2
111 or 137
(4.4 or 5.4)
122
(90)
3-5
156, 187 213
(6.0, 7.4, 8.4)
237
(175)
6
250
(10.0)
424
(313)
6.7 Setting impeller clearance
Please see section 5.3 for specific instructions on
impeller adjustment.
6.8 Disassembly
Refer to section 1.6,
Safety, before
dismantling the pump.
Before dismantling the pump make sure that
the power supply is turned off. Pump controls
are in off position, locked and tagged
Ensure genuine Flowserve replacement parts
are available on hand
Refer to sectional drawings for part numbers
and identification. See section 8 in this manual
Contact Flowserve for repair/disassembly/
rework instructions as each order is different
and are made specific to the requirements
Please take precaution during
disassembly that there is no risk of explosion due
to the nature of the
materials/tools/equipments/method used.
Wherever chemical and hazardous materials are
involved, proper safety rules have to be followed to
prevent any dangers to human lives or livestock.
Contact Flowserve for guidance, or local regulatory
agency for specific safety information.
6.7.1 Pump disassembly instructions
See section 8.0 for sectional drawings.
a) Disconnect all cables/wires and cooling water
pipe connections to the driver (if provided).
b) Carefully remove the flush or lubricant
connections and remove any associated piping
that would interfere with the dismantling.
c) Make sure that all the valves are shut
completely to avoid any leaks or spills.
d) Disconnect the coupling halves [471] (the
driver & pump).
e) Disconnect the suction (if used) and discharge
pipe connections to the discharge head.
f) Rig the motor to a suitable hoist and keep the
lifting mechanism in ready state.
g) Remove the motor to discharge head [304]
bolting and remove the motor from the
discharge head and place it on a safe and
appropriate location.
h) If the pump is of shorter length (with or without
can) rig the discharge head along with the
entire pump assembly (see section 2.3 for
lifting) using a suitable hoist (check the building
height clearance before the lifting is attempted)
i)
Use eye bolts and hooks as necessary and get
the lifting mechanism in ready state.
j)
Lifting of short set pumps
Remove the fasteners at the discharge
head/foundation/soleplate
Lift the entire pump assembly by clamping
at the discharge head [304] (See section
2.3)
k) Lifting of deep set pumps
Remove the fasteners at the foundation
plate or soleplate
Remove stuffing box/Mechanical seal [349]
completely. Protect the shaft against
damage while lifting the discharge head
[304]
Lift the pump just enough to access the
first column pipe flange connection
Support the entire pump just below the first
column pipe joint [101]