Commissioning, start-up, operation and sutdown, 1 pre-commissioning procedure, 2 pump lubricants – Flowserve APKD User Manual
Page 28: 3 impeller adjustment
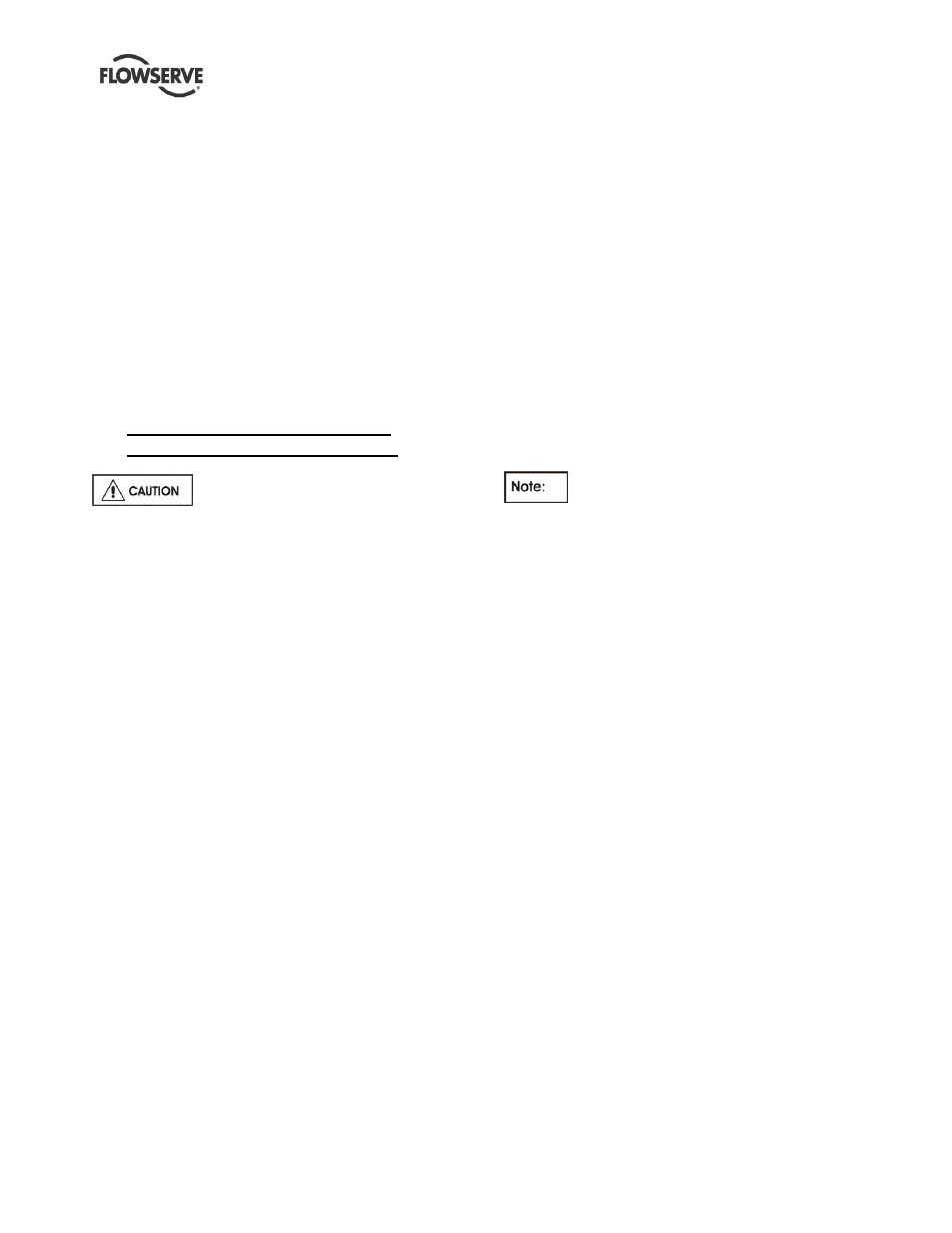
APKD DOUBLE-CASE, DOUBLE-SUCTION USER INSTRUCTIONS 26999903 07-13
Page 28 of 55
flowserve.com
If there are any circumstances in which the system
can allow the pump to run dry, or start up empty, a
power monitor should be fitted to stop the pump or
prevent it from being started. This is particularly
relevant if the pump is handling a flammable liquid.
If leakage of product from the pump or its
associated sealing system can cause a hazard it is
recommended that an appropriate leakage
detection system is installed.
To prevent excessive surface temperatures at the
bearings, it is recommended that temperature
and/or vibration monitoring is done on a regular
basis.
5 COMMISSIONING,
START-UP,
OPERATION AND SHUTDOWN
These operations must be carried
out by fully qualified personnel. Turn off power
supply for safety while pump commissioning is in
progress.
5.1 Pre-commissioning
procedure
The gland is to be filled with grease and flush
supply to be in place. Flush piping to be checked
for leaks. Mechanical seals to be checked for leaks,
flush flow and pressure.
a) For can pumps check all vent connections for
complete filling of the pump. The venting
procedure can take from 10 minutes up to 2
hours, depending on the kind of fluid.
b) Check the direction of rotation of the pump
(Coupling spacer dismantled). Should be
counter clockwise when viewed from the driver
end.
c) The pump rotor and the shaft seal must be in
correct axial position.
d) Check the readiness of all auxiliary systems
(seal sys., lubrication system etc.,) for startup.
e) All pipe work, including the internal and the
auxiliary pipe work, must be connected correctly
and must be absolutely tight. Check the
tightness of all connections of the auxiliary pipe
work. The suction valve must be open, the
discharge valve shall be closed or partially open
as required.
f)
Turn the pump by hand, if required with the help
of a lever, to check the free rotation of the rotor.
The rotor must turn uniformly and noiselessly.
Some resistance may be felt due to the friction in
the bearings and seals.
g) Check the readiness of the driver for startup.
Refer to the manual for the driver to be sure that
all precautions are in place to energize the
motor.
5.2 Pump
lubricants
Other than the stuffing box lubrication, mechanical
seal and/or lineshaft lubrication, the pump will not
require further periodic lubrication. On water
pumps, the suction bearing on the bowl assembly
should be repacked when required. If the pump will
be started after a longer storage period, the
bearings should be first flushed and cleaned by
using a suitable cleaning agent. It is not necessary
to remove the oil sprayed for short or long-term
storage as this will mix up thoroughly with the
lubrication oil.
Re-checking the motor lubrication should
be in accordance with the motor manufacturer’s
user instructions supplied separately with the
pump.
5.2.1
Open lineshaft lubrication
Open lineshaft bearings are lubricated by the
pumped fluid on short-coupled units less than 15 m
(50 ft) long and will usually not require pre or post-
lubrication. Care is to be taken to ensure that the
gland or seal is supplied with the required flush flow.
All open lineshaft pumps where the static water level
is more than 15 m (50 ft) below the discharge head
should be adequately pre-lubricated before starting
the pump.
5.3 Impeller
adjustment
Proper impeller adjustment positions the impeller
inside the bowl assembly for maximum
performance. The impellers must be raised slightly
to prevent them from dragging on the bowls, but not
raised too high so as to adversely affect hydraulic
performance.
The impeller must be down against the bowl seat
when starting impeller adjustment. When pumps are
subjected to suction pressure, the pressure acting
against the shaft tends to raise it. Make sure the
shaft is down when starting to adjust the impellers.
5.3.1
Impeller axial clearance setting
a) Install indicator bracket on pump stuffing box
extension [348] and arrange indicator so that
tip is located against lower hub face of the
pump half coupling [44]. Determine that the