Flowserve M-series PolyChem User Manual
Page 18
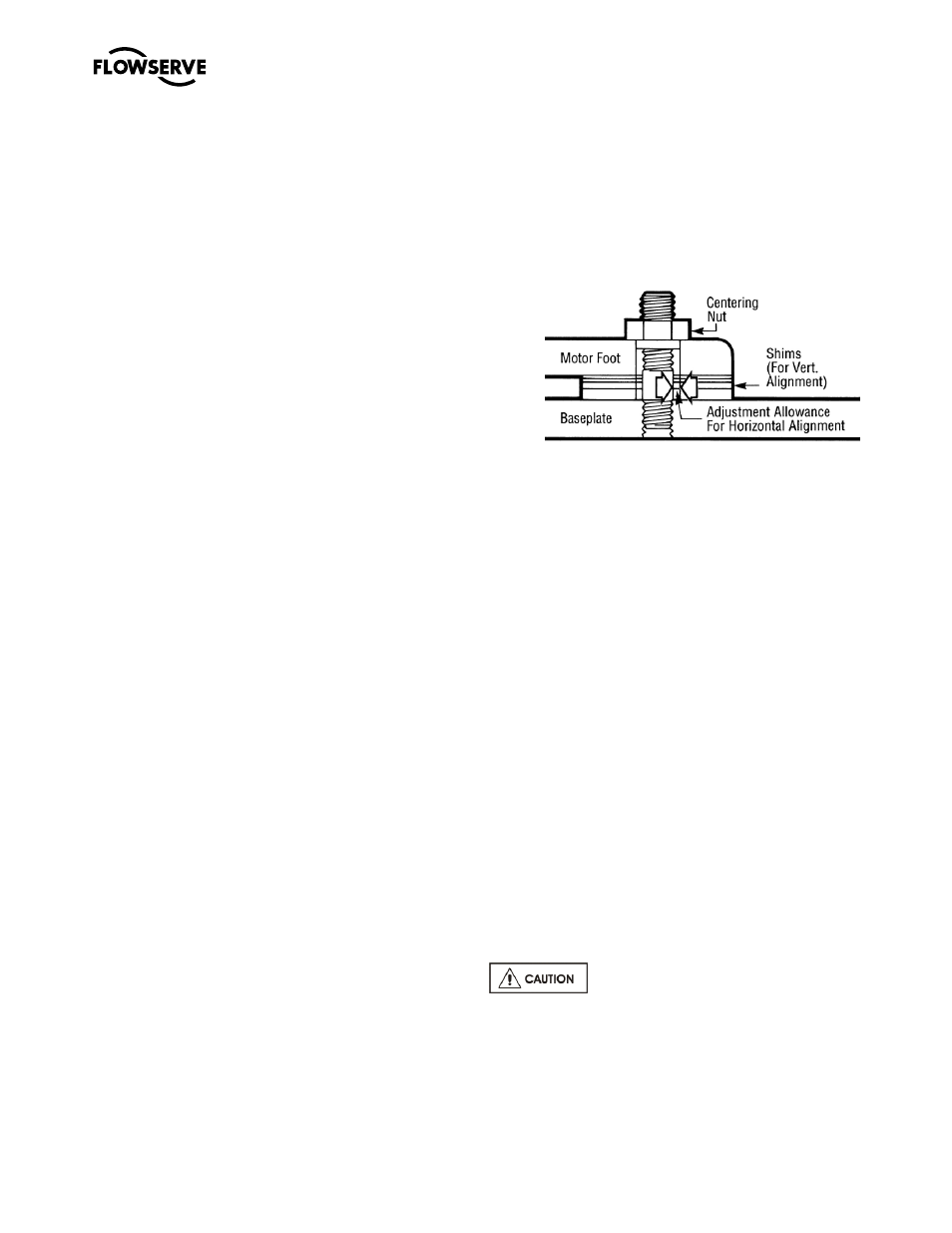
USER INSTRUCTIONS PolyChem M-SERIES ENGLISH 71569218 07-11
flowserve.com
Page 18 of 60
®
baseplate and there has been no transit damage,
and also if the above steps where done properly,
the pump and driver should be within 0.38 mm
(0.015 in.) FIM (Full Indicator Movement) parallel,
and 0.0025 mm/mm (0.0025 in./in.) FIM angular.
If this is not the case, first check to see if the driver
mounting fasteners are centered in the driver feet
holes. If not, re-center the fasteners and perform a
preliminary alignment to the above tolerances by
shimming under the motor for vertical alignment,
and by moving the pump for horizontal alignment.
j)
Grout the baseplate. A non-shrinking grout
should be used. Make sure that the grout fills
the area under the baseplate. After the grout
has cured, check for voids and repair them.
Jackscrews, shims and wedges should be
removed from under the baseplate at this time.
If they were to be left in place, they could rust,
swell, and cause distortion in the baseplate.
k)
Run piping to the suction and discharge of the
pump. There should be no piping loads
transmitted to the pump after connection is
made. Recheck the alignment to verify that
there are no significant loads.
4.5 Initial alignment
– Long-coupled
4.5.1
Horizontal initial alignment procedure
The purpose of factory alignment is to ensure that the
user will have full utilization of the clearance in the
motor holes for final job-site alignment. To achieve
this, the factory alignment procedure specifies that
the pump be aligned in the horizontal plane to the
motor, with the motor foot bolts centered in the motor
holes. This procedure ensures that there is sufficient
clearance in the motor holes for the customer to field
align the motor to the pump, to zero tolerance. This
philosophy requires that the customer be able to
place the base in the same condition as the factory.
Thus the factory alignment will be done with the base
sitting in an unrestrained condition on a flat and level
surface. This standard also emphasizes the need to
ensure the shaft spacing is adequate to accept the
specified coupling spacer.
The factory alignment procedure is summarized
below:
a)
The baseplate is placed on a flat and level
workbench in a free and unstressed position.
b)
The baseplate is leveled as necessary. Leveling
is accomplished by placing shims under the rails
of the base at the appropriate anchor bolt hole
locations. Levelness is checked in both the
longitudinal and lateral directions.
c)
The motor and appropriate motor mounting
hardware is placed on the baseplate and the
motor is checked for any planar soft-foot
condition. If any is present it is eliminated by
shimming.
d)
The motor feet holes are centered on the motor
mounting fasteners. This is done by using a
centering nut as shown in Figure 4-6.
Figure 4-6
e)
The motor is fastened in place by tightening the
nuts on two diagonal motor mounting studs.
f)
The pump is put onto the baseplate and leveled.
The foot piece under the bearing housing is
adjustable. It is used to level the pump, if
necessary. If an adjustment is necessary, add or
remove shims [3126.1] between the foot piece
and the bearing housing.
g)
The spacer coupling gap is verified.
h)
The parallel and angular vertical alignment is
made by shimming under the motor.
i)
The motor feet holes are again centered on the
motor mounting studs using the centering nut.
At this point the centering nut is removed and
replaced with a standard nut. This gives
maximum potential mobility for the motor to be
horizontally moved during final, field alignment.
All four motor feet are tightened down.
j)
The pump and motor shafts are then aligned
horizontally, both parallel and angular, by
moving the pump to the fixed motor. The pump
feet are tightened down.
k)
Both horizontal and vertical alignment is again
final checked as is the coupling spacer gap.
See section 4.8, Final shaft alignment.
4.6 Piping
Protective covers are fitted to both the
suction and discharge flanges of the casing and must
be removed prior to connecting the pump to any pipes.
4.6.1
Suction and discharge piping
All piping must be independently supported, accurately
aligned and preferably connected to the pump by a