English – Ivoclar Vivadent Manufacturer User Manual
Page 2
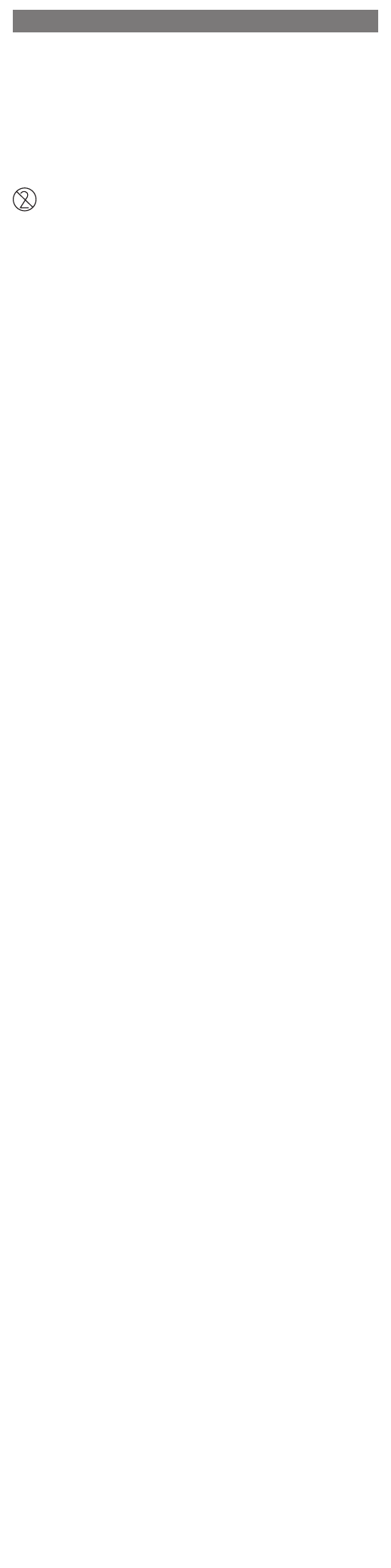
General notes:
Please also observe the country-specific regulations and guidelines regarding
the hygiene standards and reprocessing of medical devices in dental prac-
tices.
New non-sterile instruments must be subjected to a complete processing
cycle before they are used for the first time. Clean and disinfect all instru-
ments prior to each use. It is strongly recommended to additionally sterilize
the instruments in a steam sterilizer!
Single-use items and single-use components of reusable items must
not be cleaned, disinfected, sterilized and used again!
Users are strongly advised not to use damaged instruments. Maintenance
and repair work should only be carried out by specialist staff.
Do not place instruments in NaCI solution (to avoid the risk of pitting and/or
stress corrosion cracking).
Protective gloves and goggles complying with the requirements of directive
89/686/EEC must be worn to handle any used and contaminated instruments.
In line with the recommendations of the Robert Koch Institute and the guide-
line compiled by the pertinent bodies (DGKH - German Society for Hospital
Hygiene, DGSV - German Society for Sterile Supply and AKI - Working Group
Instrument Preparation), automated processing in a washer-disinfector (WD)
is to be generally preferred over manual processing. Manual processing
should only be used if automated processing is not possible.
Only a WD (compliant with DIN EN ISO 15883) with proven effectiveness
should be used to ensure reliable automated cleaning and disinfection. The
operator is responsible for ensuring that validation, performance re-qualifica-
tion and periodic routine checks of the processing procedures in the WD are
defined, documented and carried out appropriately.
Restrictions on reprocessing:
The life span of the instruments is mainly determined by wear and damage
through use. Frequent reprocessing has little impact on the performance of
these instruments.
Processing at the patient treatment area:
Carefully remove large, unhardened residues from the instruments with a
lint-free cellulose tissue immediately after use on the patient. Before you con-
tinue with the processing procedure, remove the modelling tip from the
handheld instrument and discard it. The tips are designed for single use only.
They must not be cleaned, disinfected, sterilized and re-used. The handheld
instruments may either be placed in a removal container (dry removal) or
directly immersed in a combination of detergent and disinfectant (wet re-
moval), see below, for transportation to the processing and sterilization area.
In any case, it is advisable to transport soiled instruments from the patient
treatment area to the processing area as soon as possible. Waiting periods of
several hours between contamination and processing should be absolutely
avoided.
Preparation for cleaning/disinfection:
Preliminary treatment of the instruments is strongly recommended to
protect personnel against infection and to prepare the instruments
for the automated or manual processing procedure!
To prevent residues from drying on the surfaces and to ensure preliminary
disinfection, place the instruments in a disinfection bath (with basket insert
and lid) filled with aldehyde-free alkaline disinfectant (e.g. ID 212 forte, Dürr
Dental, for 15 min). Make sure that the instruments are completely covered in
disinfectant and that the disinfectant is free of bubbles. The disinfectant used
should be suitable for the instruments in question and tested for effectivness
(e.g. DGHM or FDA certification or CE mark). Please adhere to the disinfec-
tant manufacturer’s instructions (concentration rate, temperature and contact
time) to ensure that the disinfectant is used correctly.
If you use an automated processing method, carefully rinse the instruments
under running tap water after preliminary disinfection to prevent residues of
the cleaning and disinfecting agent from reaching the WD.
Automated cleaning and disinfection:
Requirements to carry out the validated procedure:
–
WD: G 7882, Miele (A
0
-value > 3000)
–
Program: Vario TD
–
Cleaning and disinfecting agent: Neodisher FA, Dr. Weigert
Place the instruments in an instrument container that is suitable for your
particular type of WD, according to the WD manufacturer’s directions. Fill the
WD with cleaning and disinfecting agent (e.g. Neodisher FA, Dr. Weigert) as
appropriate for the intended process. Observe the directions of the disinfec-
tant and equipment manufacturer. Start the cleaning and disinfection pro-
gram (e.g. Vario TD) validated for the particular type of unit.
Drying:
After the cleaning and disinfection program has been completed, remove the
instruments from the WD and completely dry any remaining moisture with
compressed air or a clean, lint-free single-use towel.
Maintenance, checking and inspection:
Visually inspect the instruments to see if they are clean, undamaged and
function properly. If macroscopically visible residual debris is present on the
instruments, repeat the cleaning and disinfection process.
If the instruments have only been cleaned in the WD (without automated dis-
infection), thermal disinfection of the unwrapped instruments in a steam ster-
ilizer is absolutely mandatory!
Manual cleaning and disinfection:
Requirements to carry out the validated procedure:
–
Soft brush: nylon instrument cleaning brush, Miltex
–
Cleaning and disinfecting agent: ID 212 forte, Dürr Dental
Only use soft brushes for the manual removal for visible residues. Never use
metal brushes or steel wool.
Brush the instruments with a suitable brush (e.g. nylon instrument cleaning
brush, Miltex) in the disinfection bath of the preliminary treatment until you
can no longer see any contamination on the surface. Remove the instruments
English