Troubleshooting, 2 spindle orientation, Table 13 multi-function output settings (h2- ) – Yaskawa A1000 AC Drive Spindle Orientation User Manual
Page 15: Table 14 faults
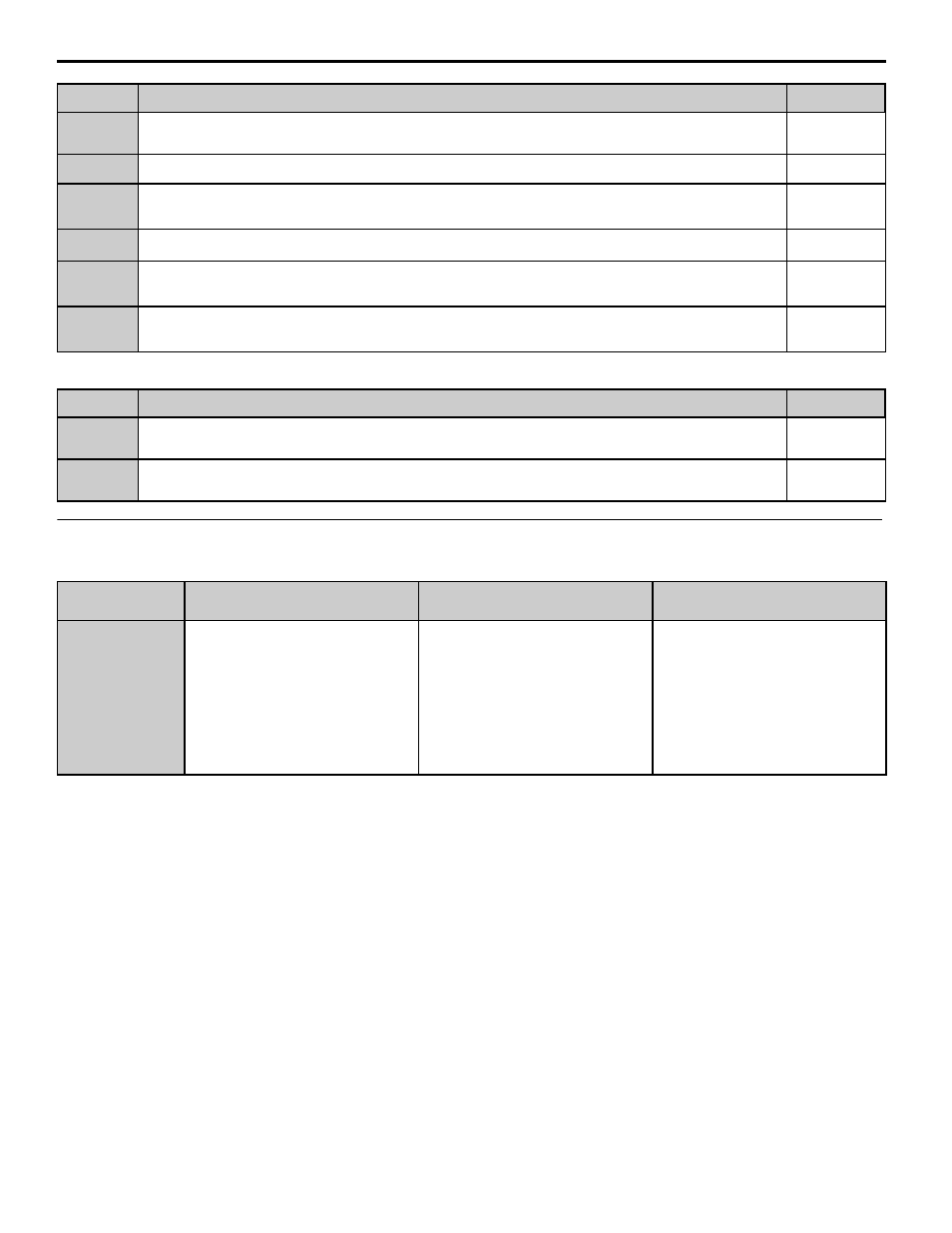
2 Spindle Orientation
YASKAWA TM.A1000SW.063 Spindle Orientation A1000 Custom Software Supplement
15
Table 13 Multi-Function Output Settings (H2- )
Troubleshooting
Table 14 Faults
82
Orient CMD REV
Closed: Causes the drive to run in the reverse direction and orient the motor to the current orientation position offset from the marker pulse.
Function Description on page 17
.
– – – Y– – N
83
Sequential Reset
Closed: Sets the active orientation offset parameter to P2-02 (sequence 0). This function is only active if P2-01 = 1.
– – – Y– – N
84
Offset Sel 1
Orientation Position Offset Selection 1. See Section
Refer to Orient Position Offset Selection on page 25
and parameters P2-02, P2-03, P2-04 and
P2-05.
– – – Y– – N
85
Offset Sel 2
Orientation Position Offset Selection 2.
Refer to Orient Position Offset Selection on page 25
and parameters P2-02, P2-03, P2-04 and P2-05.
– – – Y– – N
86
Gear Ratio Sel 1
Motor Gear Ratio Selection 1.
Refer to Configuration 2: Indirect Drive with Orientation Encoder on page 23
and parameters P2-06, P2-07, and
P2-08.
– – – Y– – N
87
Gear Ratio Sel 2
Motor Gear Ratio Selection 2.
Refer to Configuration 2: Indirect Drive with Orientation Encoder on page 23
and parameters P2-06, P2-07, and
P2-08.
– – – Y– – N
Setting
Description
Control Method/
Access Level
40
Orient Complete
Closed: The machine is within the orient position window established by P1-05 and the P1-07 ORT Set Time has expired. Once this condition is
met, the output remains closed as long as the machine is within the P1-06 window.
– – – Y– – N
41
Home Position
Closed: The active orientation position offset is P2-02 (sequence 0). This output is only active when P2-01 = 1 (Sequential Marker Offset
Selection).
– – – Y– – N
Fault Indication
Digital Operator Display
<Memobus>
Description
Cause
Countermeasures
Marker Pulse Detection
Error
CDEV
Marker Det Error
<3Ch>
The drive monitors the number of A and B channel
encoder pulses between each marker pulse
(Z or C channel). There should be F1-01
(Encoder PPR) A and B channel pulses between
each marker pulse. If the pulse count exceeds F1-01
x 8, the drive displays a CDEV fault and coasts to a
stop.
Note: If Orientation encoder parameter P1-10 = 1,
parameter F1-31 sets Encoder PPR. If an Indirect
Drive configuration is used, Orientation encoder
PPR is multiplied by the active gear ratio.
This fault is displayed when the motor has gone two
rotations without receiving a marker pulse from the
motor encoder (Z or C channel).
This could be caused by disconnected or
malfunctioning hardware, or inappropriate
parameter settings.
This fault is only triggered while an orient digital
input is activated and the frequency reference is less
than the P1-01 Orient Speed.
- Remove all run commands from the drive. Check
the wiring of the encoder, especially the Z pulse.
- Check for noise on the encoder feedback signals.
- Check the F1-01/F1-31 parameter setting matches
the encoder being used.
Setting
Description
Control Method/
Access Level