Changes from the standard product – Yaskawa A1000 AC Drive Spindle Orientation User Manual
Page 7
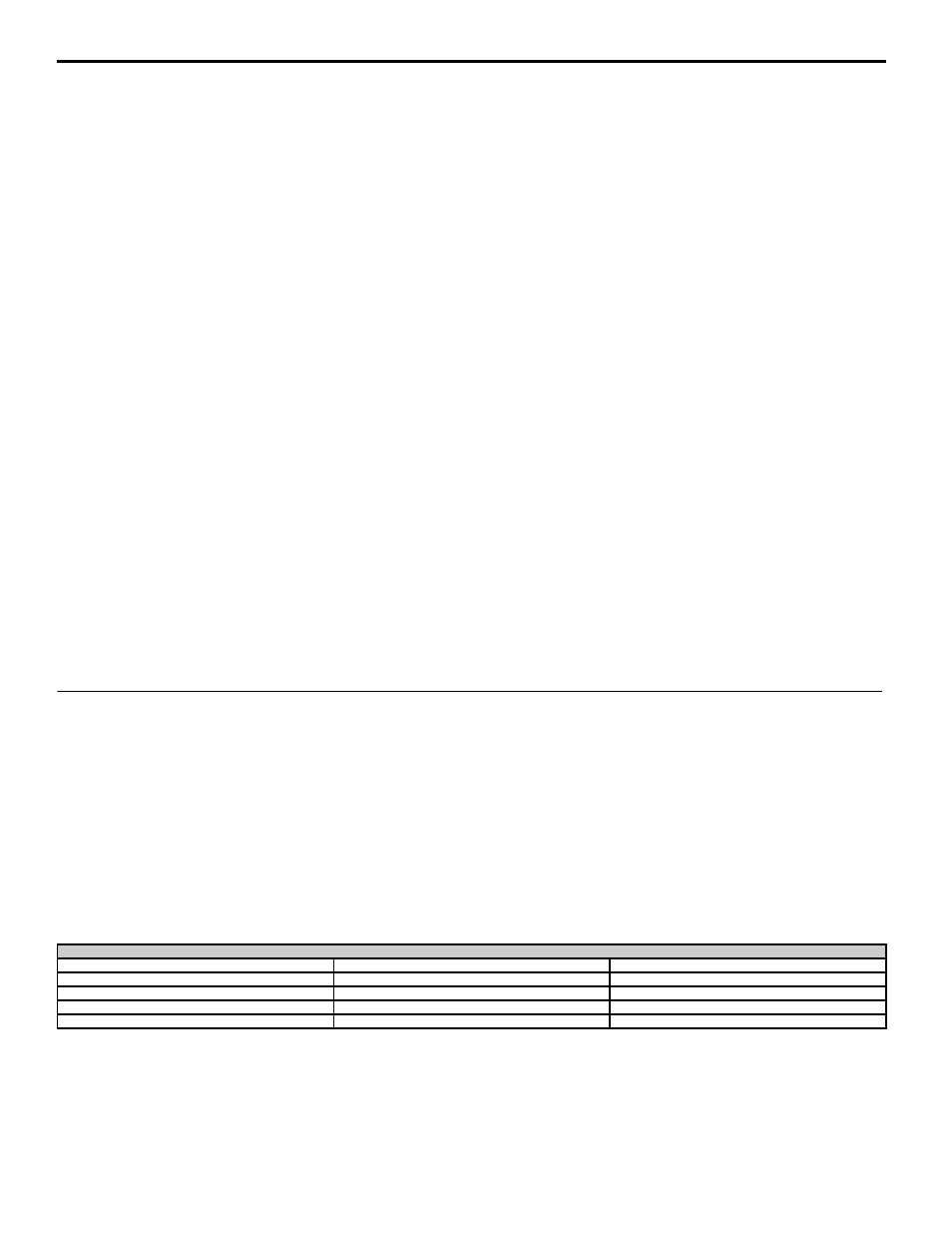
2 Spindle Orientation
YASKAWA TM.A1000SW.063 Spindle Orientation A1000 Custom Software Supplement
7
Direct Drive
In the first configuration, the drive motor directly drives the machine part being oriented (positioned). When using this
method, the motor encoder is used for both closed loop vector motor control and for orientation. This encoder must have
a C or Z channel which provides a “marker” or “index” pulse with every rotation. If the encoder does not have a C/Z
channel, an external marker pulse can be implemented as outlined in
Encoder (PG) Option Card Configuration and
. Additionally, a PG-X3 or PG-B3 encoder (PG) feedback option card is required to connect the
encoder to the drive.
Indirect Drive with Orientation Encoder
When the motor and the machine part to be oriented (positioned) are connected through a drive train with a constant ratio,
two encoders are required. The first encoder is mounted on the driven motor, and the second, an orientation encoder, is
mounted on the machine part to be oriented. The orientation encoder must have a C or Z channel which provides a
“marker” or “index” pulse with every rotation. If the encoder does not have a C/Z channel, an external marker pulse can
be implemented as outlined in
Encoder (PG) Option Card Configuration and Wiring on page 29
. The motor encoder
does not need to have a C/Z channel. Two encoder (PG) feedback option cards are required for this setup.
Indirect Drive with Proximity Sensor
When the motor and the spindle are connected through a drive train and the spindle does not have its own encoder, a
proximity sensor may be used. The proximity sensor is connected as an external marker pulse; therefore this
configuration requires only one PG-X3 encoder (PG) feedback option card. In this configuration, the gear ratio of the
drive train must be expressed as the number of revolutions of the motor per revolution of the spindle.
Online Control Mode Switch Function
This software can switch between Closed Loop Vector Control and V/f Control during run. The 1000 Hz software is
limited to V/f control mode above 400 Hz, it is possible to change tools without stopping the machine if the inverter
switches to Closed Loop Vector Control for Position Control at Low-Speed. At Low-Speed the inverter can be set to
operate in Closed Loop Vector Control and automatically switch to V/f Control when the output is above the frequency
which is set.
Changes from the Standard Product
• Second PG Channel Parameters F1-30 through F1-37 are always visible whether or not digital selection H1-0 =16
(Motor 2 Select) is programmed.
• Only two Control Modes can be set in A1-02 and E3-01, 0:V/f and 3:Closed-Loop Vector.
• Only two Auto-Tuning Mode Selections are available, 0:Rotational Auto-Tuning and 2:Stationary Auto-Tuning for
Line-to-Line Resistance.
Deleted Functions
Certain functions in the standard software of A1000 are deleted in this Orientation software. Deleted functions are listed
in
.
Table 2 Deleted Functions
Function Name
Speed Search (all methods)
KEB Function
Fault Restart
High Slip Braking (HSB)
Overexcitation Braking
Field Weakening Function
Energy Savings
Droop Control
Field Forcing Function
Frequency Reference Lower Limit
Feed Forward Control
DC Injection Braking Current Setting in V/f
Torque Detection
Stall Prevention Selection during Acceleration
Stall Prevention Selection during Run