3 bearing carrier/power end assembly, 2 wet end assembly, 1 split gland yoke – Flowserve Mark 3 User Manual
Page 38
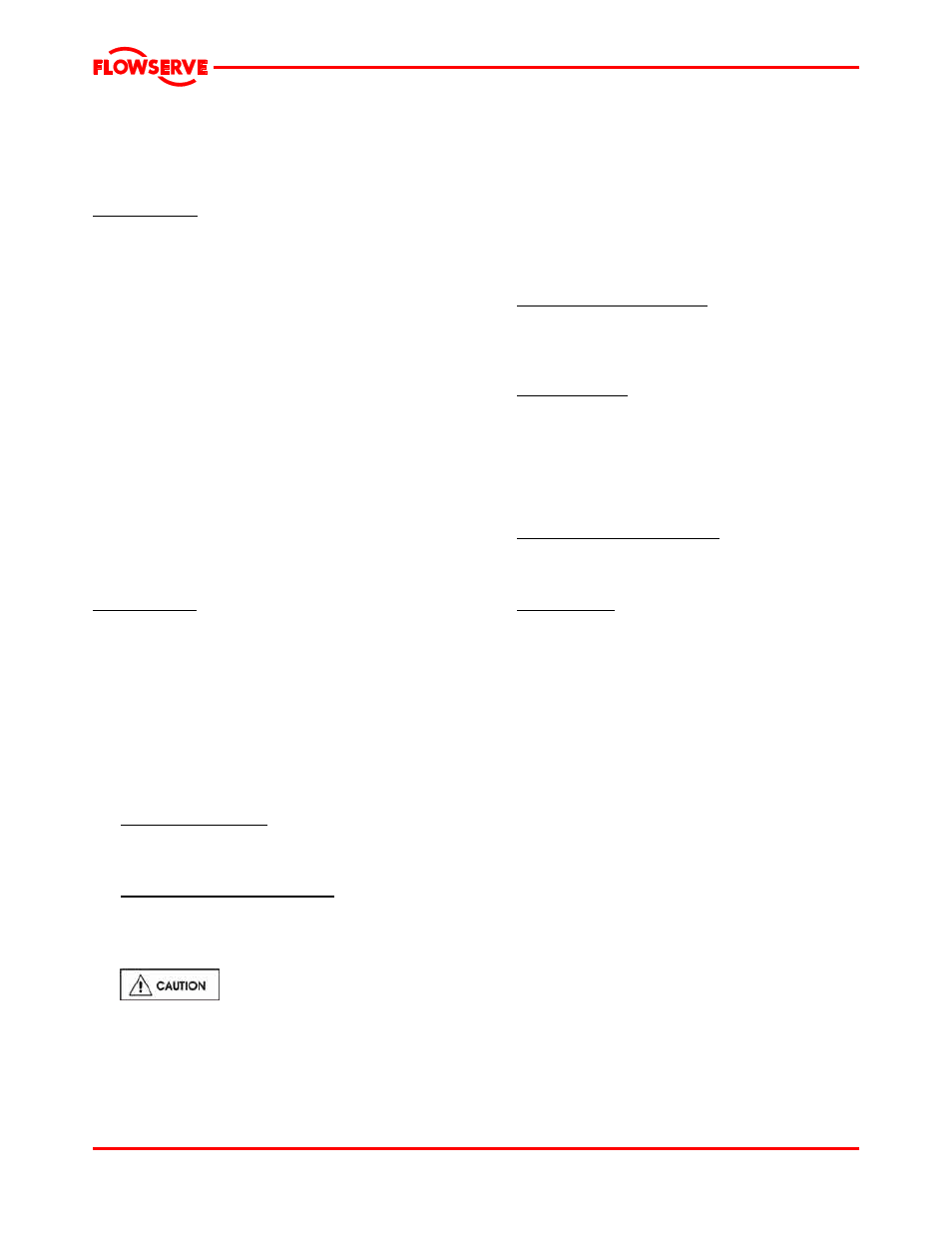
USER INSTRUCTIONS MARK 3 High Silicon Iron ENGLISH 71569249 09-04
style, the cavity between these two lips should be
1
/
2
to
2
/
3
filled with grease. When installing this part, the large
metal face on the lip seal must face away from the
bearings.
Labyrinth seals
The following are general installation instructions
regarding the VBXX Inpro seal. Follow the
instructions provided with the seal by the
manufacturer.
The elastomer O-ring located on the OD of the seal
has been sized to overfill the groove in which it is
located. When installing the seal into its
corresponding housing, in addition to compressing
the O-ring a certain amount of material may shear off.
This sheared material should be removed. An arbor
press should be used to install the seal.
Install the inboard seal in the bore of the bearing
housing adapter with the single expulsion port
positioned at the 6 o’clock position.
Install the outboard seal in the bore of the bearing
carrier. There are no orientation issues since this is a
multiport design seal.
Magnetic seals
Follow the installation instructions provided by the
manufacturer.
6.9.1.3 Bearing carrier/power end assembly
a) Install new O-rings [4610.2] onto the bearing
carrier. Be sure to use the correct size O-rings.
(The Mark 3 and Mark 3A bearing carriers use
different O-rings.)
b) Slide the bearing carrier [3240] over the outboard
bearing [3012].
c) Install the outboard bearing retaining device.
Double row bearings Slide the snap ring [2530.1]
in place with its flat side against the outboard
bearing and snap it into its groove in the bearing
carrier.
Duplex angular contact bearings
Slide the bearing retainer [2530.2] against the
outboard bearing and install and tighten the
socket head capscrews [6570.2]. See figure 6-2
for correct torque values.
Never compress the snap ring
unless it is positioned around the shaft and between
the bearings. In this configuration, it is contained
therefore if it should slip off the compression tool it
is unlikely to cause serious injury.
d) The shaft, bearings, and bearing carrier assembly
(figure 6-11) can now be installed into the bearing
housing [3200]. The bearing carrier [3240] should
be lubricated with oil on the O-rings and threads
before installing the assembly into the bearing
housing. Thread the bearing carrier into the
bearing housing by turning it clockwise to engage
the threads. Thread the carrier onto the housing
until the carrier flange is approximately 3 mm (
1
/
8
in.)
from the housing. Install the set screws [6570.3]
loosely.
e) Reinstall any tags, plugs, site gages and oiler.
Mark 3 and Mark 3A design
Install the following items onto the bearing housing;
oil level tag (figure 6-15) and combination Trico
oiler/site gage [3855], vent/breather [6521] and
drain plug [6469].
ANSI 3A design
Install the following items onto the bearing
housing; oil level tag (figure 6-15) and site gage
[3855], plug [6521] and magnetic drain plug
[6469].
f) Assemble the bearing housing adapter [1340] to
the bearing housing [3200]. Be sure to install a
new O-ring [4610.1].
Mark 3A and ANSI 3A design
Thread the capscrews [6570.5] through the
adapter and into the tapped holes in the bearing
housing.
Mark 3 design
Use the capscrews [6570.5] and hexnuts
[6570.5A]. Orient the bearing housing adapter
with the two holes for capscrews [6570.5] on a
horizontal line.
g) If the pump has lip seals, install the deflector [2540].
h) If the pump is equipped with a hook type sleeve
[2400], slip it into place over the impeller end of
the shaft [2100].
6.9.2 Wet end assembly
6.9.2.1 Split Gland Yoke
Four basic configurations are available. Split Gland
Yokes are available tapped [4121.1] and un-tapped
[4121.2]. Gaskets [4590.4] are used for locations
where the casing seal chamber has a hole. Spacers
[4590.5] are used when there is no casing seal
chamber hole.
Page 38 of 48