1 actuator fails to operate, 2 jammed valve detected – Flowserve MX Electronic Actuator User Manual
Page 87
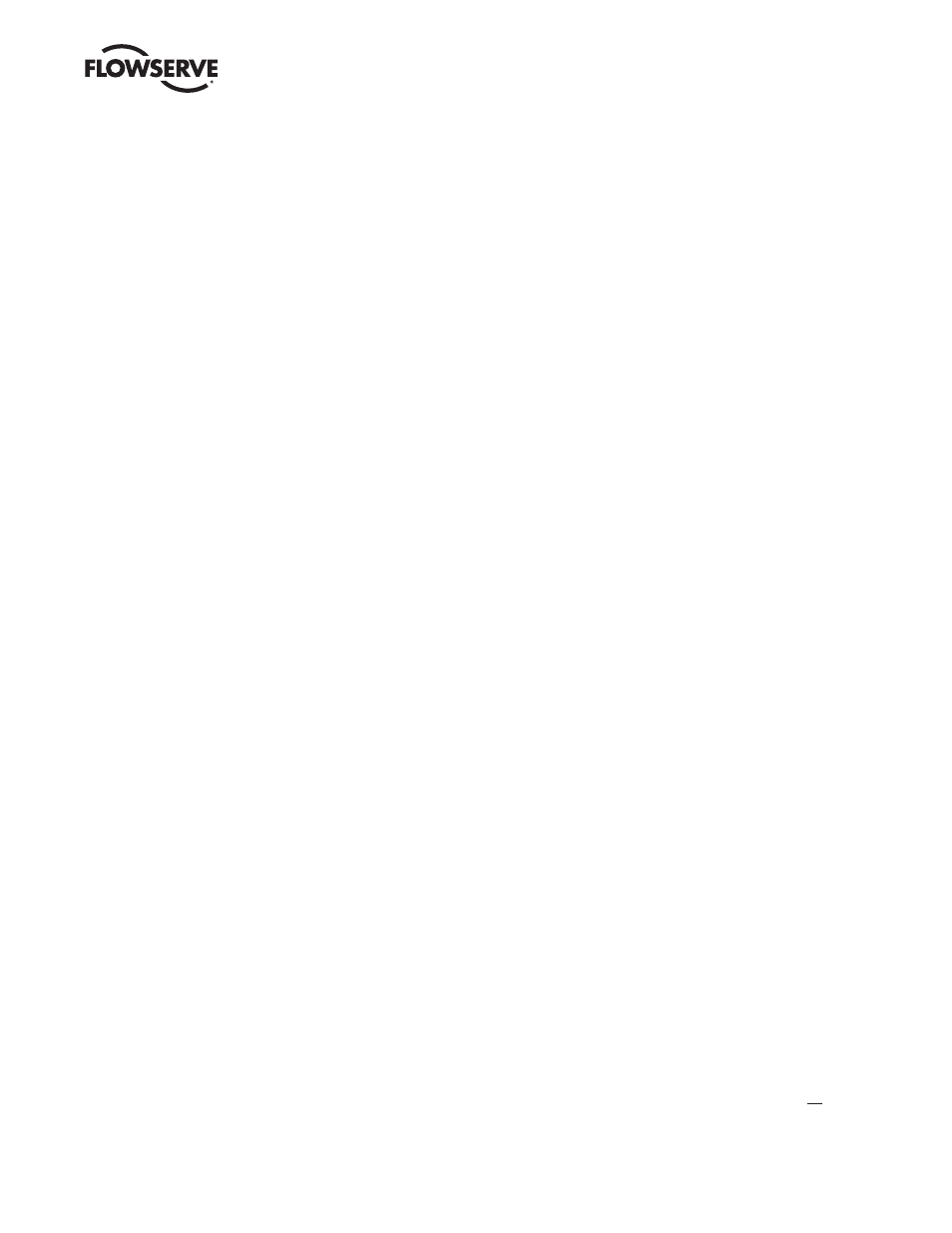
87
Limitorque MX Electronic Actuator FCD LMENIM2306-06 – 10/13
flowserve.com
4. Switch on main power supply.
5. Measure VAC at 23, 24 – should be 110 VAC if actuator is supplied with optional 110 VAC circuit. If no power, check
fuses FS1, FS2 (600 VAC, 1 A, fast acting, 10.3 x 38.1 mm tube) and FS3 (250 VAC, 0.1A, time delay, 5 x 20 mm
glass tube) and replace if necessary. If replacing fuses does not fix the problem, replace damaged board. Contact
Limitorque Service at (434) 528-4400.
6. Measure VDC at 21, 22 – should be 24 VDC, maximum power of 5W. If not, replace damaged board.
7. Replace the control compartment cover (ACP).
5.2.1 Actuator Fails to Operate
Actuator Fails to Operate from LOCAL Controls
1. Place the red selector knob in “LOCAL.”
2. If motor runs but actuator output does not turn, check that declutch lever has returned to motor operation position.
3. Check LCD display for following alarms:
• If motor runs but no actuator movement is detected, check if the display says “JAMMED VALVE” and free if
necessary.
• Inhibit signal may be present or absent at the terminals. Check for signal and adjust as necessary. “INHIBIT
ACTIVE” appears on display.
• Thermal overload of the motor may have been detected. Check motor for high temperature. Thermal overload is
self-resetting when motor cools. “MOTOR OVERTEMP” appears on the display.
4. Check to see if the position limits are set incorrectly on top of one another. See Section 3.5.4, Setting Position
Limits.
Actuator Fails to Operate from REMOTE Controls
1. Check that the actuator will operate from “LOCAL.” If not, then carry out the checks described below.
2. Check that the red knob is in “REMOTE.”
3. ESD signal may be present or absent at the terminals. Check for signal and adjust as necessary. (“ESD ACTIVE”
at display.) If actuator was previously operated in “LOCAL,” then the fault is probably in the remote control circuit.
Check the integrity of the cabling and that the connections to the terminals are in accordance with the wiring
diagram. If motor runs in “LOCAL,” but not “REMOTE,” adjust ESD to be greater than local (“ESD>LOCAL”).
4. Confirm correct monitor relay operation. See Table 3.5.
5.2.2 Jammed Valve Detected
1. Check that position limits have been set correctly. If valve is position-seated, the limits should stop the motor just
before the end-of-travel. Recalibrate the position limits if necessary. See Section 3.5.4, Setting Position Limits.
2. Check that torque settings are correct for the valve. Recalibrate if necessary. See Section 4.6, Torque Setup.
3. Check the condition of the valve and lubrication of the valve stem and thrust bearings. The valve may have
remained in the same position for a long time and become corroded internally or externally. Engage manual over-
ride and employ the handwheel drive to unseat the valve.
4. Verify that the actuator will now operate the valve. Open and close the valve a few times to check for correct opera-
tion throughout the travel.
NOTE: To free a jammed valve from the “CLOSE” or “OPEN” position, engage manual override and attempt to unseat it
using the handwheel drive. If a rising stem valve is jammed in the close position, loosen the fixing bolts that attach the
thrust base to the valve. This will release the compression in the drive components and reduce the effort to unjam the
valve. Partly open the valve, then retighten the bolts.