Hypertherm MAX200 Service Manual User Manual
Page 155
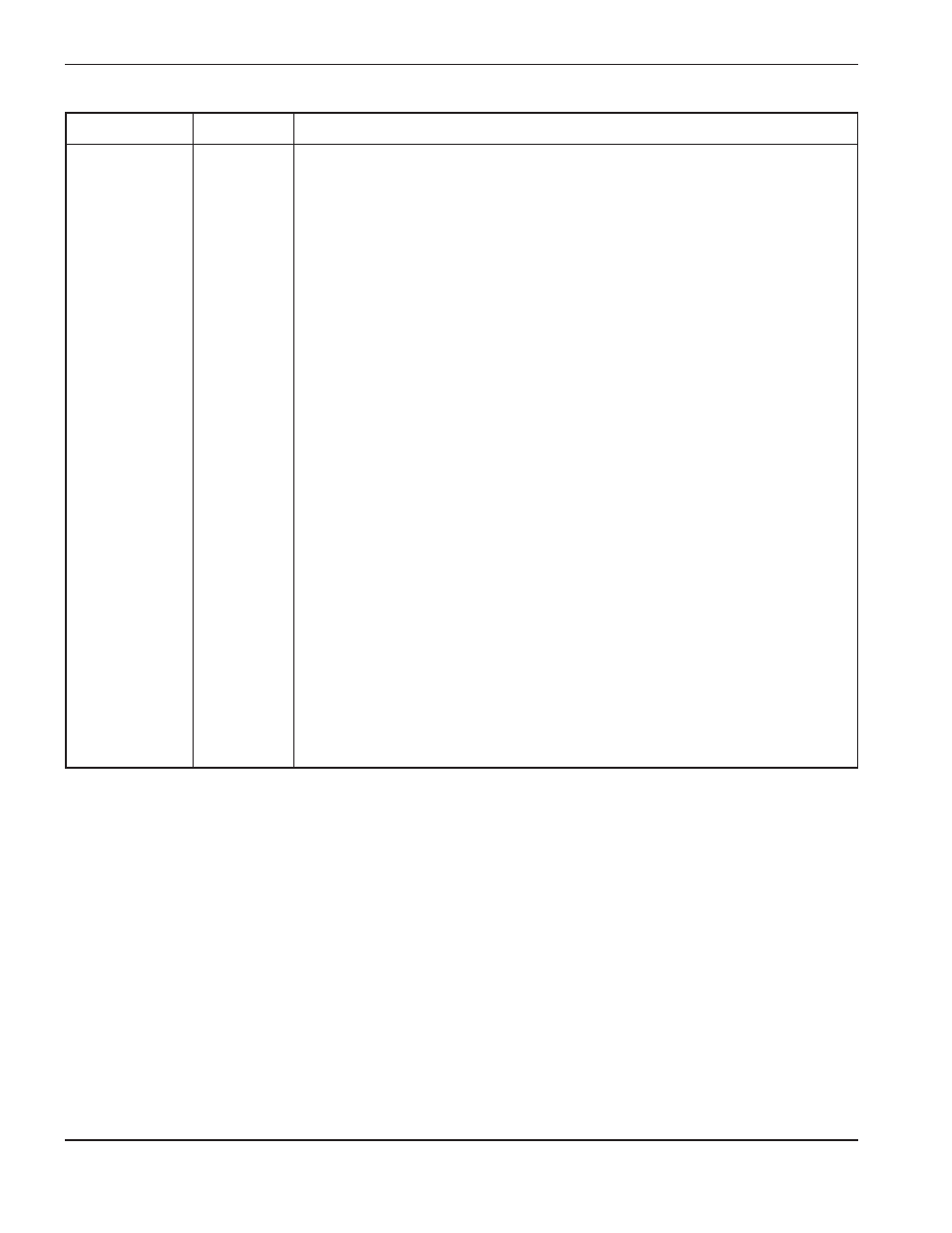
4-60
MAX200
Service Manual
PARTS LIST
Lug
Color
Description and Comments
81
Red
Plasma Emergency Stop (24VAC) – 1X1 pins 28, 33;
80
Yel
cable lugs 80, 81. Open to stop. To use, remove jumper on TB3-80 and 81 in
power supply.
82
Blu
Plasma Start (24VAC) – 1X1 pins 9, 15; cable lugs 82, 83. Close to
83
Blk
start; Open to stop.
173
Sig.
Yel
* Initial Height (12VDC) – 1X1 pins 2, 6; cable lugs 173, 174. Close for
174
Com.
Blk
no IHS; Open for IHS.
171
Sig.
Brn
* Auto Height (!2VDC) – 1X1 pins 3, 7; cable lugs 171, 172.
172
Com.
Blk
Close for no Auto Height; Open for Auto Height.
135
Sig.
Orn
* Current 50% (12VDC) – 1X1 pins 4, 8; cable lugs 135, 136.
136
Com.
Blk
Reduces current to 50% of preset for cornering, etc. Close for 50% current; Open
for 100% current.
87
Sig.
Wht
* Hold (12VDC) – 1X1 pins 1, 5; cable lugs 86, 87. Synchronizes
86
Com
Blk
starting of two or more systems. Close for no start; Open for start.
169
Load
Red
* Relay Down (Solid state relay (dry contacts), rated to switch 24 to
170
Line
Blk
240VAC, 1 amp. DC relay optional.) – 1X1 pins 29, 34; cable lugs 169, 170.
167
Load
Grn
* Relay Up (Solid state relay (dry contacts), rated to switch 24 to
168
Line
Blk
240VAC, 1 amp. DC relay optional.) – 1X1 pins 30, 35; cable lugs 167, 168.
84
Red
** Machine Motion – Delayed – 1X1 pins 31, 36; cable lugs 84, 85.
85
Blu
Contact closes after arc transfer and time delay (set on power supply front panel).
Relay (dry contacts).
79
Red
*** Machine Motion – Advanced – 1X1 pins 32, 37; cable lugs 79, 78.
78
Grn
Contact closes approximately three seconds before arc fires. Relay (dry contacts).
77
Hot
Red
Auxiliary 24VAC, 1 amp. – 1X1 pins 21, 22; cable lugs 77, 76.
76
Neut
Wht
Notes:
1X1 designates connector on rear of power supply. Lug numbers designate wire numbers on end of Interface cable.
* These functions are available only on MAX200s equipped with Torch Height Control option.
** Note that resistor R150 and capacitor C78 are connected in series across the contacts. In some cases one lead of
R150 must be cut from the control PC board as the R-C circuit may provide enough current flow to maintain machine
motion input to cutting machine.
*** Note that resistor R155 and capacitor C79 are connected in series across the contacts. In some cases one lead of
R155 must be cut from the control PC board as the R-C circuit may provide enough current flow to maintain machine
motion input to cutting machine.
Figure 4-24 Machine Interface Cable Diagram – 2 of 2