Hypertherm MAX200 Service Manual User Manual
Page 66
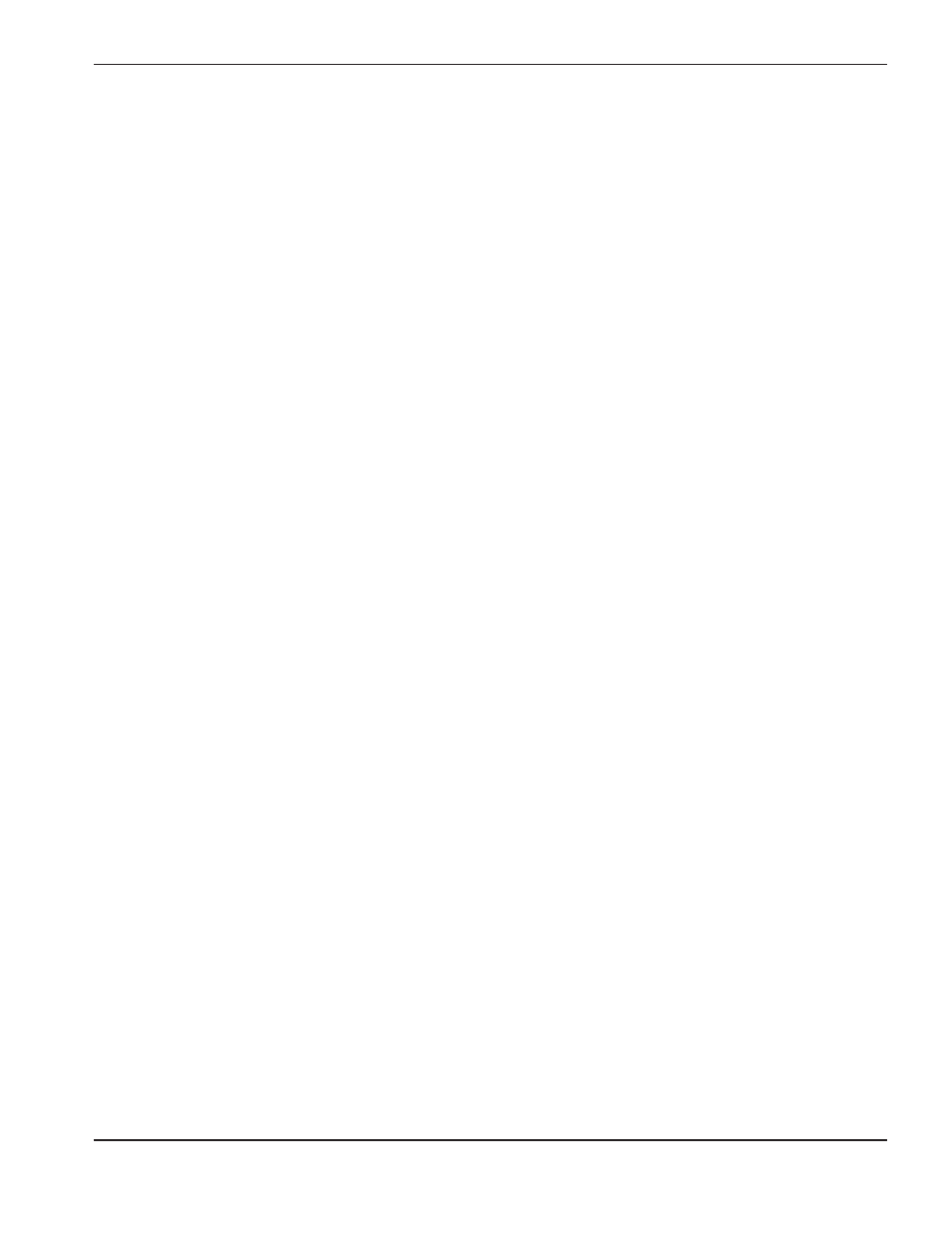
MAX200
Service Manual
3-25
1-97
MAINTENANCE
Problem
Possible Causes and Solutions
• On Machine-Torch system: Cutting machine switch
(normally open) to terminals 82&83 of TB3 of power
supply.
• TB3 to REC3 of PCB6 .
• REC3 of PCB6 to REC1 of PCB7.
Repair and/or replace defective component(s), if necessary.
9.2. Control Board PCB7 or LT2 bulb is defective.
Check to see if D5 and D33 on PCB7 are illuminated (see
Figure 3-16). If these indicators are illuminated and wiring
checkout as described above is O.K., LT2 may not be
getting 24VAC from Control Board. Proceed as follows (see
Figure 4-2 for location of LT2):
• Monitor between points 64&65 with an AC volt meter.
(64&65 are terminal points to the LT2 bulb)
• Press START. Voltage between these points should read
24VAC. If there is no 24VAC, use the 013-2-179 wiring
diagram and check wires and conncectors from LT2 to
REC1 of PCB7. Repair and/or replace defective
component(s), if necessary.
If wiring is OK, replace PCB7.
• If there is 24VAC between points 64&65 after START is
pressed, replace bulb LT2.
10.
The unit stops cutting during
cut, or cuts poorly.
10.1. The work clamp is not connected or it is broken.
Connect or repair the work clamp.
10.2. Arc not transferring to workpiece.
Check work clamp and cable connecting clamp to
workpiece. Good contact must be made in order for the
arc to transfer to the workpiece.
10.3. There is insufficient air or gas pressure.
Check gas inlet pressure specifications under Cut Charts
in Operation section of MAX200 Instruction Manual
(#800870 or #800980).
Check plasma and shield gas pressures in TEST and RUN
modes as specified under Cut Charts in Operation section
of MAX200 Instruction Manual (#800870 or #800980).