System troubleshooting - 2 of 4 -12, System t roubleshooting - 2 of 4 – Hypertherm HT4400 HySpeed Plasma Arc Cutting System User Manual
Page 103
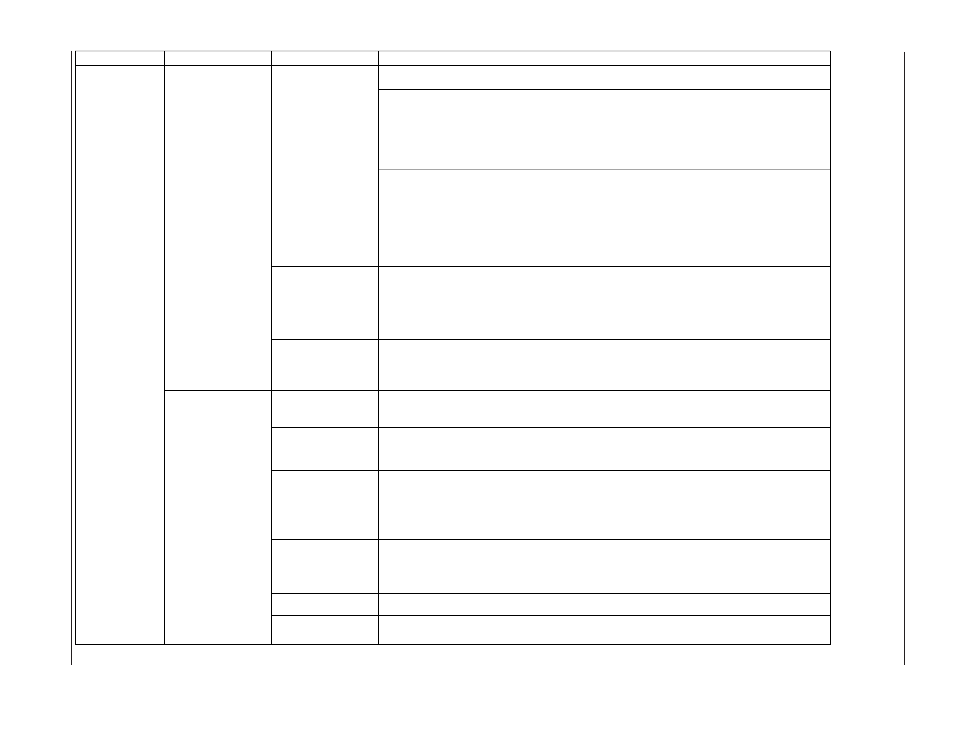
Condition
Result
Cause
Solution
Refer to
Leak Tests in the Operation section of this manual and perform the test
shown.
Make sure the inlet pressure for both plasma and shield pressures are set to the book
values. When cutting, monitor the pressure on each pressure gauge. Be sure that
pressure is not dropping more than +/- 10 psi (+/- 0.7 bar). A good delivery system with
a good regulator will not drop more than 5 psi (0.3 bar). Dips in pressure could be from
a faulty regulator, an insufficient gas source, a leak in the delivery line before the
regulator or a leak/restriction after the pressure regulator.
With inlet pressures set to the book values and gas pressures set up according to the
cut charts in the manual, the plasma preflow and cut-flow pressures should be as
shown in the cut charts. There are pressure values at the bottom of each cut chart for
PG1 and PG2 during cutting. All pressures should be within +/- 5 psi (+/- 0.3 bar) for
preflow, cut-flow and run. If one of these pressures is high and all gas settings are
correct, then there is a restriction in the gas system after the Off-Valve Assembly. If one
of these pressures is low, then there is a leak in the system, an insufficient gas source
or a restriction before the Off-Valve Assembly.
There is an internal
coolant leak within
the torch
Purge preflow for 30 seconds, purge cut-flow gas for 30 seconds and then switch to run
mode. Let system idle for about 15 minutes. Lower torch to 1/2" (12 mm) from the plate
and place a mirror under the torch. Purge preflow for 30 seconds and purge cut-flow for
30 seconds. If moisture begins to deposit on the mirror, then there is a coolant leak
within the torch. Check all o-rings on the torch body and on the bullet connectors on the
back of the torch.
Pierce height too
close to plate or
pierce thickness is
above maximum
Refer to the cut charts in the operation section of the manual for correct pierce height
and maximum pierce thickness.
Pilot arc lead is
shorted to the work-
piece
The resistance of the pilot arc lead to ground or the work lead should be 1 Kohms or
higher.
Pilot arc relay
(CR1) contacts are
welded shut
Locate the pilot arc relay on the center bail. When firing the torch over metal, this relay
should open as soon as the arc is transferred to the plate.
Faulty work lead
connection
A faulty work lead and/or work lead connection increases the time the pilot arc is on
and increases nozzle wear. To determine if the pilot arc is not transferring to the plate
immediately, watch the green LED on the Start Circuit (PCB14) while firing over the
plate.
If the LED illuminates it should only blink quickly. If the LED illuminates for more
than .5 seconds then the arc is not transferring to the plate immediately.
Power supply
output current is
greater than the
current setting
Check output current at CS5 on Analog Board (PCB3), refer to
Current Sense Test in
this section of manual. If the actual output current is higher than the set output current,
check the output current of each chopper.
Shorted torch head Replace the torch.
Piercing too high off
plate
Refer to cut charts in the Operation section of this manual for proper pierce height.
Outside orifice of
nozzle is
countersunk
The system may
have a gas leak, a
faulty pressure
regulator or a gas
restriction
Nozzle orifice
etched on one side,
and/or electrode life
is short, and/or
electrode is black at
the tip
Poor
Consumable
Life
MAINTENANCE
5-12
H
T44
00
Instruction Manual
2
System T
roubleshooting - 2 of 4