Cutting techniques -29, How to get better cut quality -29, Cutting techniques – Hypertherm HT4400 HySpeed Plasma Arc Cutting System User Manual
Page 88
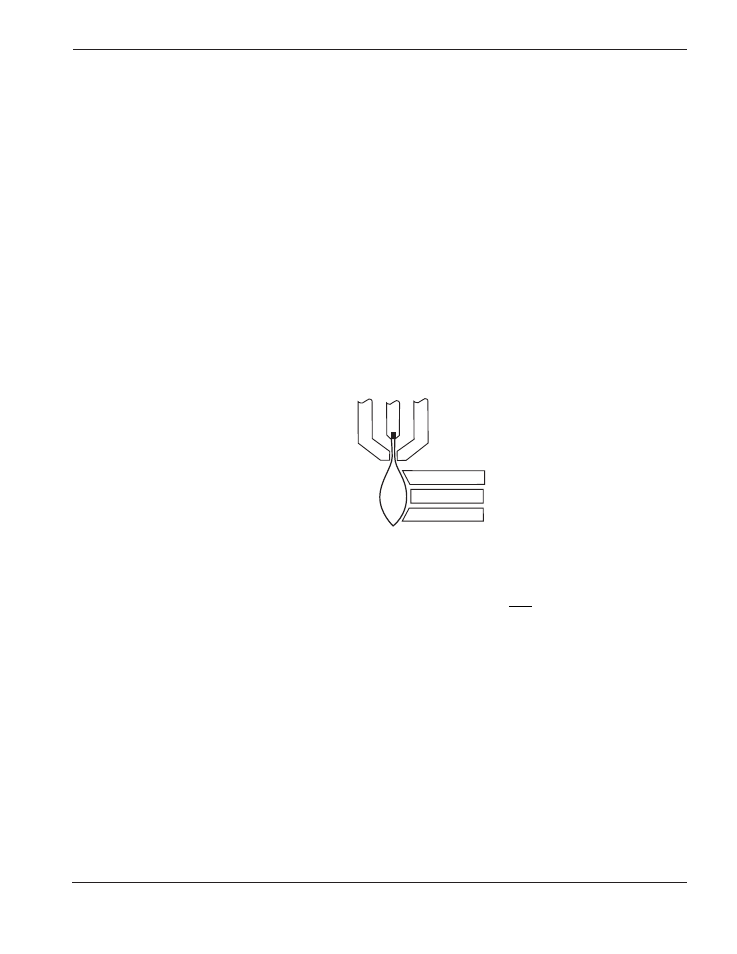
Negative Bevel
Positive Bevel
Zero Bevel
Torch too low
Torch too high
OPERATION
HT4400
Instruction Manual
4-29
2
Cutting Techniques
How to Get Better Cut Quality
In order to get the best cut quality, ensure the HT4400 plasma system is set up according to the Daily Start-Up
procedure in this section. The 3 major components of cut quality are: cut angle, dross, and shape (flatness) and
smoothness of the cut surface.
Cut Angle
Cut angle is defined as either positive or negative. A positive cut angle is when there is more material removed
from the top of the kerf than at the bottom (V-shaped cut). A negative cut angle is when there is more material
removed from the bottom of the cut than at the top (undercut).
The 2 most common cut angle faults are as follows:
1. The average cut angle of 4 sides is off by 3 to 4°. Angles greater than this can be caused by:
• Torch-to-work distance. If cut angles are all positive or all negative, torch-to-work distance is most likely
the problem. Vary the arc voltage to correct the cut angle.
• Damaged consumable parts. If the nozzle orifice is worn uniformly, the cut angle will show positive.
Change or check consumables by referring to Changing Consumable Parts in this section.
• Machine travel is in the wrong direction. The square cut angle is on the right with respect to the forward
motion of the torch.
2. Non-uniform cut angles (one side positive and the other negative), this is caused by:
• Damaged or worn consumable parts, especially the nozzle and shield. Change or check consumables
by referring to Changing Consumable Parts in this section.
• Torch is out of vertical alignment to workpiece. Ensure that the torch is at right angles to the workpiece
(0° and 90°) to get a clean, vertical cut. Use a square to align the torch.
Dross Conditions
Dross can occur in the following ways:
1. Low speed dross happens when the torch travel speed is too slow and the arc shoots ahead. It forms as a
heavy, bubbly deposit at the bottom of the kerf and can be easily removed. Normally, increasing the speed
will reduce the dross.