How to get longer consumable life -30 – Hypertherm HT4400 HySpeed Plasma Arc Cutting System User Manual
Page 89
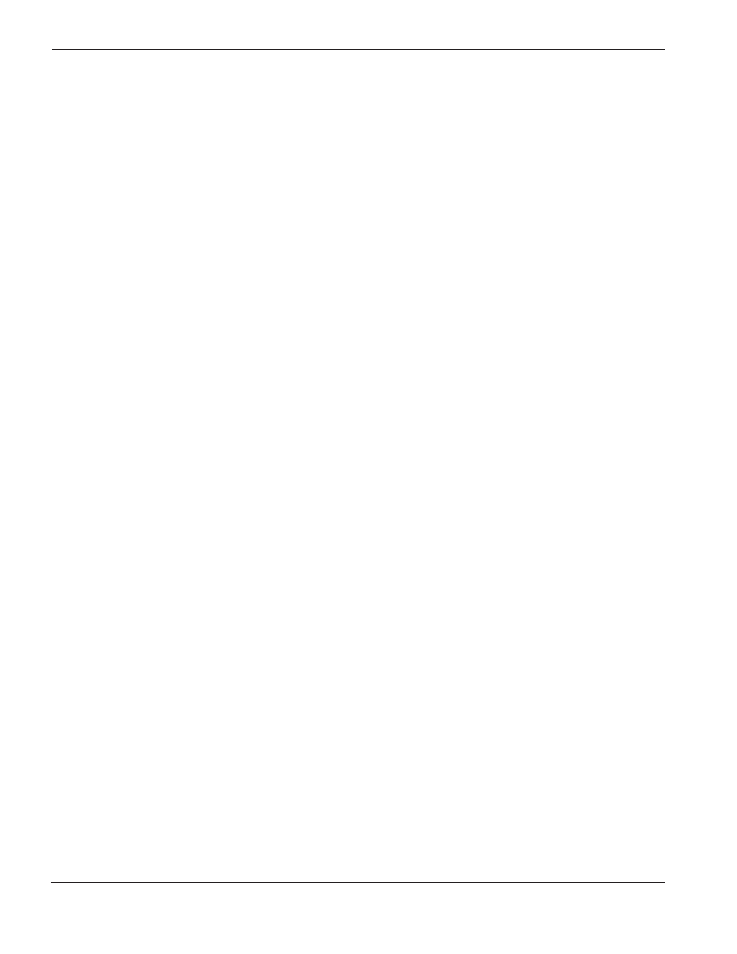
OPERATION
4-30
HT4400
Instruction Manual
2
2. High speed dross occurs when the torch travel speed is too fast and the arc lags behind. It forms as a thin,
linear bead of solid metal attached very close to the kerf. The dross appears to be a fused continuation of
the kerf wall. It is welded to the bottom of the cut and is very difficult to remove. High speed dross can be
reduced in the following ways:
• Decreasing the travel speed will reduce the dross. If changing the speed does not remove the dross,
varying the following parameters will help.
• Lowering the torch-to-work distance by decreasing arc voltage will reduce the dross.
3. Dross may show at certain parts of the cut (the dross comes and goes), if the consumables are worn or
damaged.
4. Dross formation is material dependent.
5. Dross formation is dependent upon metal temperature. Warm and hot metal is much more prone to dross
accumulation than cool metal. For example, the first cut in a series of cuts will mostly likely have the least
amount of dross. As the workpiece heats up, dross levels are likely to increase on the subsequent cuts.
Shape of Cut Surface
The ideal shape of the cut face is straight. Sometimes the cut face becomes either concave or convex. Maintaining
the correct torch height and cut speed are required to keep the cut face straight.
1. A concave cut face (bevel on inside) is due to torch-to-work distance being too low. Increasing the arc
voltage will increase the torch-to-work distance and straighten the cut face.
2. A convex cut face (top of cut rounded) is due to the torch-to-work distance being too high or cutting current
being too high. First, try reducing the arc voltage, and then the cutting current. If there is overlap between
different cutting currents for that thickness, try the lower current consumables.
Smoothness of Cut Surface
Both the plasma jet and the motion of X-Y table will affect the smoothness of the cut surface.
1. The plasma jet can cause random roughness. Change the shield gas O
2
/N
2
ratio for cutting mild steel. A
higher concentration of oxygen in the shield mixture will increase the potential cut speed, but at the
expense of a rougher cutting edge.
2. A regular wavy surface is due to machine motion. Tuning the drives and cleaning the rails will help.
How to Get Longer Consumable Life
The HT4400 plasma system incorporates Hypertherm's patented LongLife
®
process to extend the life of consum-
able parts. Full compliance with the LongLife operating procedures that follow, as well as the gas purity
requirements listed earlier in this section, is necessary in order to optimize the useful life of consumable parts.