6 dynamic collision monitoring (software option), Function – HEIDENHAIN iTNC 530 (340 49x-04) ISO programming User Manual
Page 96
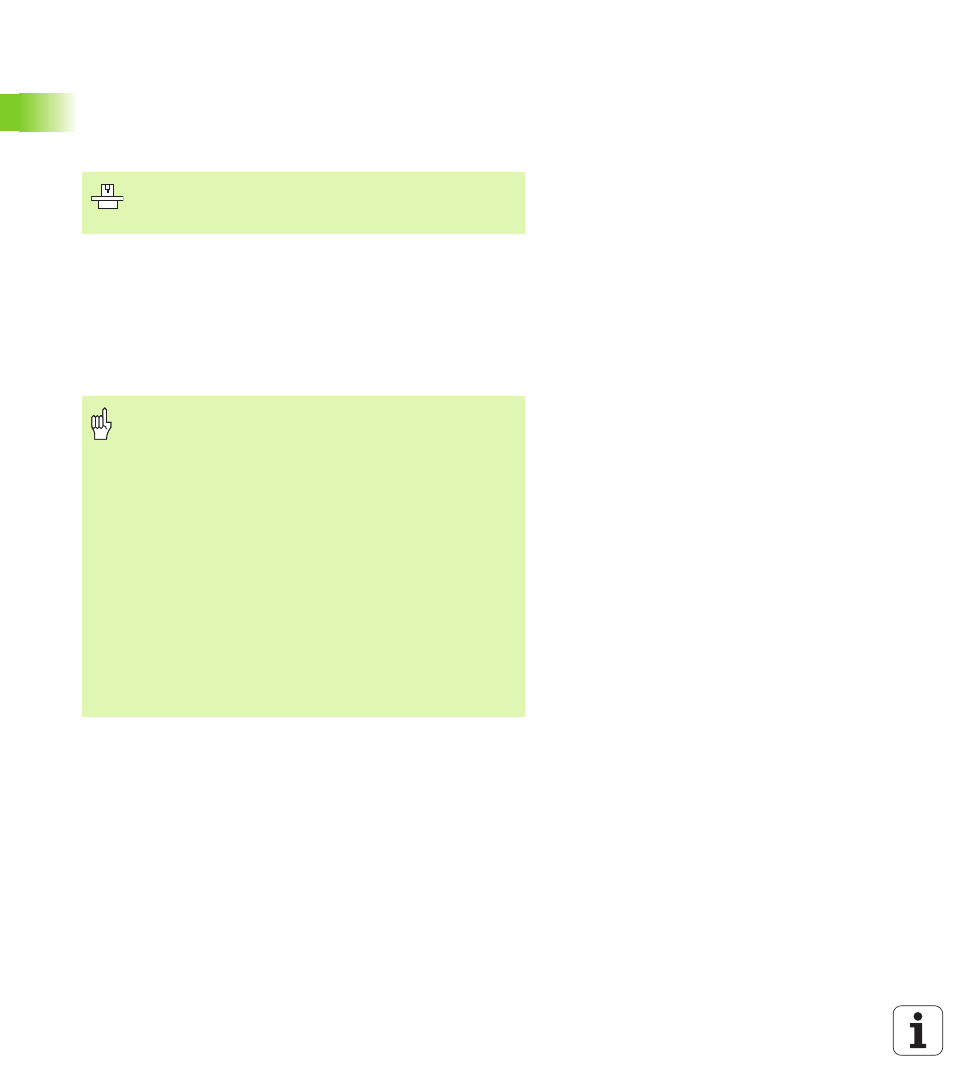
96
2 Manual Operation and Setup
2.6 Dynamic Collision Monit
o
ri
ng (Sof
tw
ar
e Option)
2.6 Dynamic Collision Monitoring
(Software Option)
Function
The machine manufacturer can define any objects that are monitored
by the TNC during all machining operations. If two objects monitored
for collision come within a defined distance of each other, the TNC
outputs an error message. The TNC can display the defined collision
objects graphically in a Program Run mode of operation (see “Graphic
depiction of the protected space (FCL4 function)” on page 99).
The TNC also monitors the current tool with the length and radius
entered in the tool table for collision (assuming a cylindrical tool).
The Dynamic Collision Monitoring (DCM) must be adapted
by the machine manufacturer for the TNC and for the
machine. Refer to your machine manual.
Keep these constraints in mind:
DCM helps to reduce the danger of collision. However,
the TNC cannot consider all possible constellations in
operation.
Collisions of defined machine components and the tool
with the workpiece are not detected by the TNC.
DCM can only protect those machine components from
collision that your machine tool builder has correctly
defined with regard to dimensions and position in the
machine coordinate system.
The TNC can monitor the tool only if a positive tool
radius has been defined in the tool table. The TNC
cannot monitor tools with a radius of 0 (as is often used
in drilling tools).
For certain tools (such as face milling cutters), the
diameter that would cause a collision can be greater than
the dimensions defined in the tool-compensation data.