Yaskawa G7 Drive User Manual
Page 21
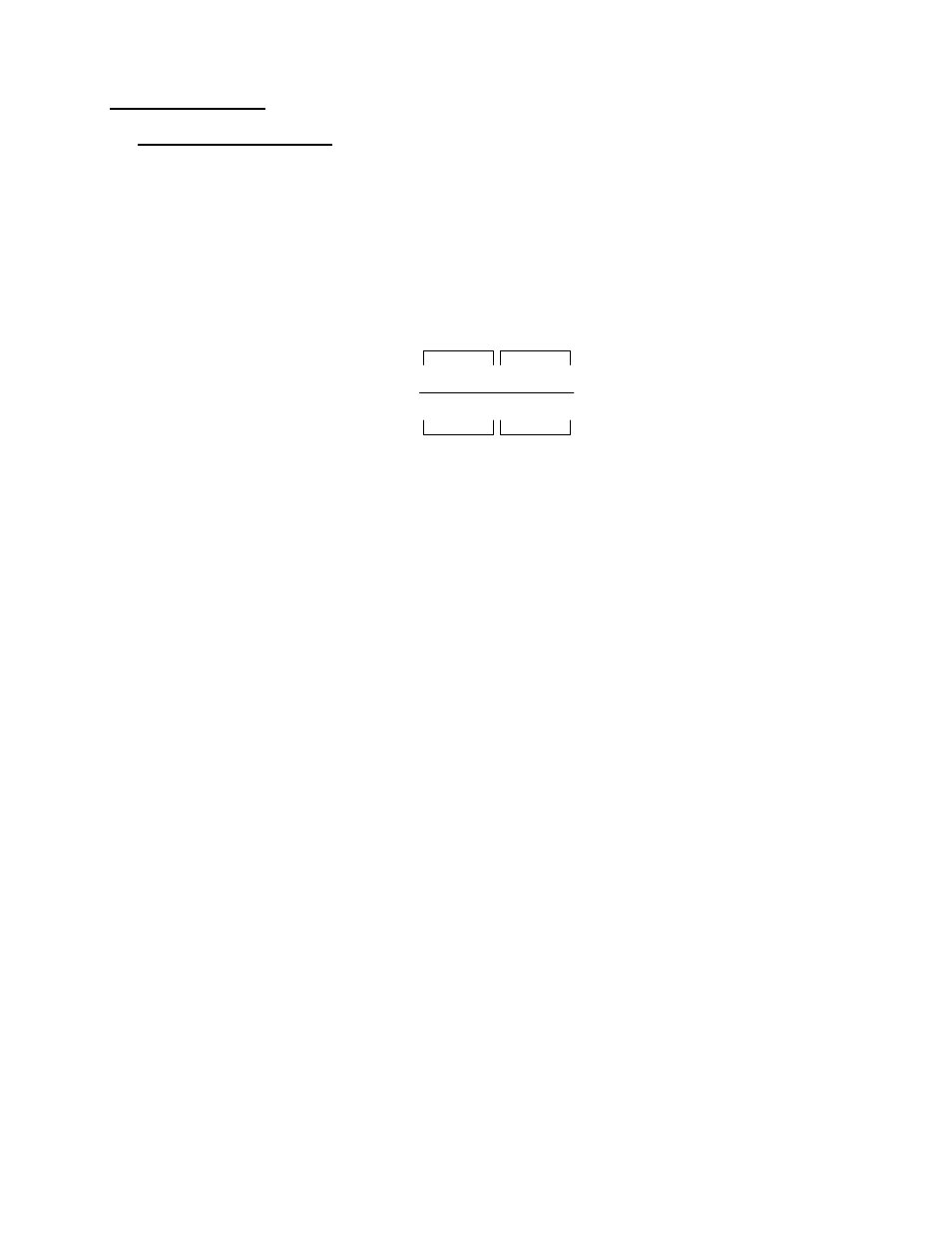
Date: 03/31/09, Rev: 09-03
Page 21 of 30
TM.G7SW.064
5.0 Function Description
5.1 Basic Electronic Lineshaft
When the Follower Mode Selection P1-01 = 1 ~ 3 (speed follower mode), the follower drive will follow the
speed of the master encoder signal. Using the gear ratio parameters P1-03 ~ P1-06, the follower drive can
be made to run at a ratio of the master speed. The alternate gear ratio (P1-07 and P1-08) can be selected
using the Ratio 2 Select multi-function digital input (H1-0X = 81). The basic gear ratio formula is:
Follower Frequency Reference = Master Encoder Frequency Reference x (Numerator / Denominator)
For the primary gear ratio, the formula is:
Master
Encoder
Frequency
Reference
(U1-90)
X
X X X X X X X X
X X X X X X X X
=
Follower
Frequency
Reference
(U1-91)
P1-03
P1-04
P1-05
P1-06
The pairs of numerator and denominator parameters are used together to form an 8-digit number divided by
an 8-digit number. For ratio’s that can be expressed using 4-digit numbers or less, simply use P1-03/P1-04.
Gear ratio 2 can only be expressed as a 4-digit number divided by a 4-digit number.
The gear ratio needed for the application must be able to be exactly expressed by the above formula. This
includes the complete remainder. If the ratio cannot be exactly expressed, the follower will drift in phase
over time.
The gear ratio can be further adjusted using the Digital Ratio Adjustment P2-01), the Analog Ratio
Adjustment (H3-05/09 = 20), the MOP Adjust multi-function inputs (H1-0X = 84 ~ 86), and the Network
Communication Ratio Adjustment (Modbus register 61CH). These adjustments are summed and then
added to 100% to produce the total gear ratio adjustment, which is multiplied by the master encoder
frequency (after gear ratio calculation). See Figure 8 at the end of the document.
When Follower Mode Selection P1-01 = 4 or 5 (ELS modes), the drive will track follower position relative to
the master encoder. A PI regulator is applied to the position error. The output of the position PI regulator is
used to trim the speed reference calculated from the master encoder signal, gear ratio parameters, and
gear ratio adjustment. In this manner, the position of the follower motor will be synchronized with the
position of the master encoder. The Advance Follower (H1-0X = 82) and Retard Follower (H1-0X = 83)
multi-function inputs can be used to change the position of the follower relative to the master. See Figure 7
at the end of the document.
When the gear ratio of the drive is changed instantaneously in ELS mode (either due to the gear ratio
parameters being changed during run or because of a change of state of the Ratio 2 Select multi-function
input), the drive will ramp to the new ratio using Accel/Decel Time 2 (C1-03/C1-04). The position error will
be held to zero during the ratio change until the drive re-enters Speed Agree (based on the Ratio Change
Speed Agree Width P3-07).