Yaskawa G7 Drive User Manual
Page 24
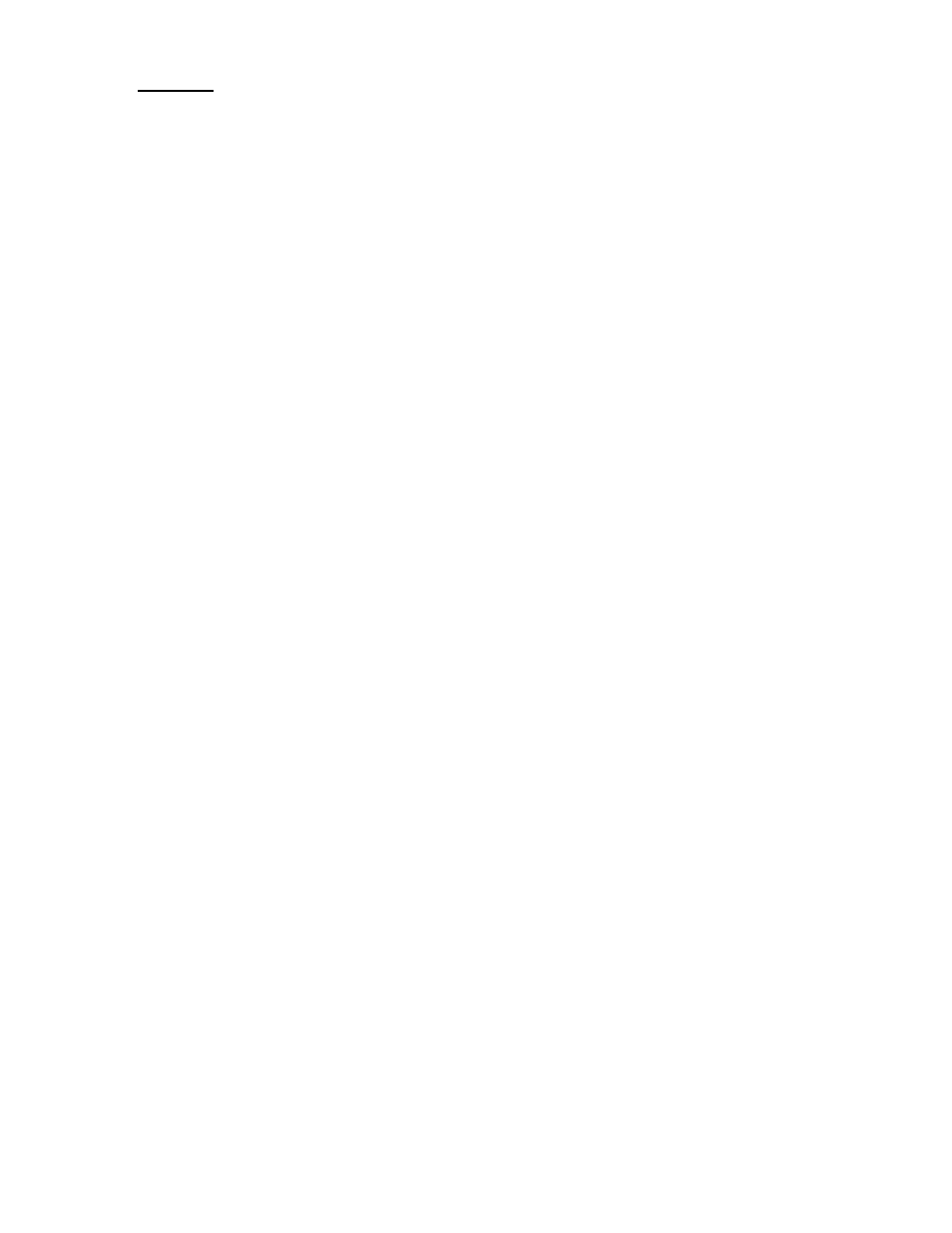
Date: 03/31/09, Rev: 09-03
Page 24 of 30
TM.G7SW.064
5.3 Alignment
The Alignment function builds off of the existing Electronic Line Shaft functionality, and is identical to ELS
except where noted below. In order to use Alignment, the following conditions must be met: the Follower
Disable digital input must be open (H1-XX = 80), the Align by Pulse input must be closed (H1-XX = 89), the
drive must also be in closed loop vector control (A1-02 = 3), and either ELS mode (P1-01 = 4, 5) must be
selected.
Also, if the follower drive is traveling at a speed less than the DC Injection frequency (B2-01) or is traveling
in the negative direction, the Alignment function will be disabled, but standard ELS will continue to function.
Any conditions that cause the ELS position error to be cleared (held at zero) will also disable Alignment.
Alignment is maintained by adding the Displacement Error (difference between the Displacement Reference
U1-94 and the Displacement Feedback U1-95) into the same position error that is used by both ELS
modes. This difference is added only once each time it is measured (once for each master/follower
alignment pulse combination received). If the Disable Alignment Error digital input is closed (H1-XX = 91),
the system will calculate Displacement Feedback, but the Alignment Error will not be summed into the
position error.
The In Alignment multi-function digital output will close when the magnitudes of the Position Error and the
Displacement Error are both less than the Alignment Tolerance (P4-02). The In Alignment digital output can
only be set after making a Displacement Error calculation; therefore the Position Error must be within range
at the moment the Displacement Error is calculated. If the magnitudes of either the Position Error or the
Displacement Error are greater than the Alignment Tolerance, the In Alignment digital output will open. The
In Alignment output will function even if the Disable Displacement Error multi-function digital input is closed.
The In Alignment output will be reset if the Master or Follower Marker signal is lost. If the master encoder
travels more than 1.5 master revolutions since the last Master Marker Pulse, the In Alignment output will be
reset (opened). If the Follower Marker Pulse is not seen for two consecutive Master Marker Pulses, the In
Alignment output will be reset (opened). The In Alignment output will function even if the Disable
Displacement Error input is closed.
When the drive powers up, the Displacement Reference value is loaded from the Initial Displacement
Reference parameter (P4-01). P4-01 will serve as the Displacement Reference as long as the
Displacement Reference network communications register value is at zero (see Section 4.6). When a non-
zero value is written to the Displacement Reference register, this value will become the Displacement
Reference. P4-01 will resume as the Displacement Reference when a zero is written to the Displacement
Reference register.
While P4-01 has control over the Displacement Reference and the Align by Pulse multi-function digital input
is closed, the Advance/Retard Follower inputs will have a second effect of adjusting the Displacement
Reference along with adjusting the current position of the follower motor. The Advance follower input will
move the follower motor forward and will reduce the Displacement Reference by an equal amount. The
Retard follower input will move the follower motor backwards and will increase the Displacement Reference
by an equal amount. This change will only affect the Displacement Reference value, not the actual P4-01
parameter. The Advance/Retard follower inputs will have no affect on the Displacement Reference while the
Displacement Reference register has control. If the P4-01 parameter is changed while it has control over
Displacement Reference, the new P4-01 value will be loaded into the Displacement Reference.
Two parameters are used to ensure that the follower drive is not too reactive when correcting alignment
errors. The first parameter is the Maximum Correction per Revolution (P4-03). This limits the number of
counts of Displacement Error that can be added to the Position regulator each time the master and follower
alignment pulses are read. This value can also help limit Displacement Feedback overshoot and oscillation
issues when bringing the follower into alignment from an initial large Displacement Error. The second
parameter is P3-04 (Position PI Limit), which has the effect of regulating the maximum delta speed with
respect to master speed the follower will travel at to correct alignment errors.