3 thermal design of enclosure, 1 thermal design – Yaskawa YASNAC PC NC Connecting Manual User Manual
Page 25
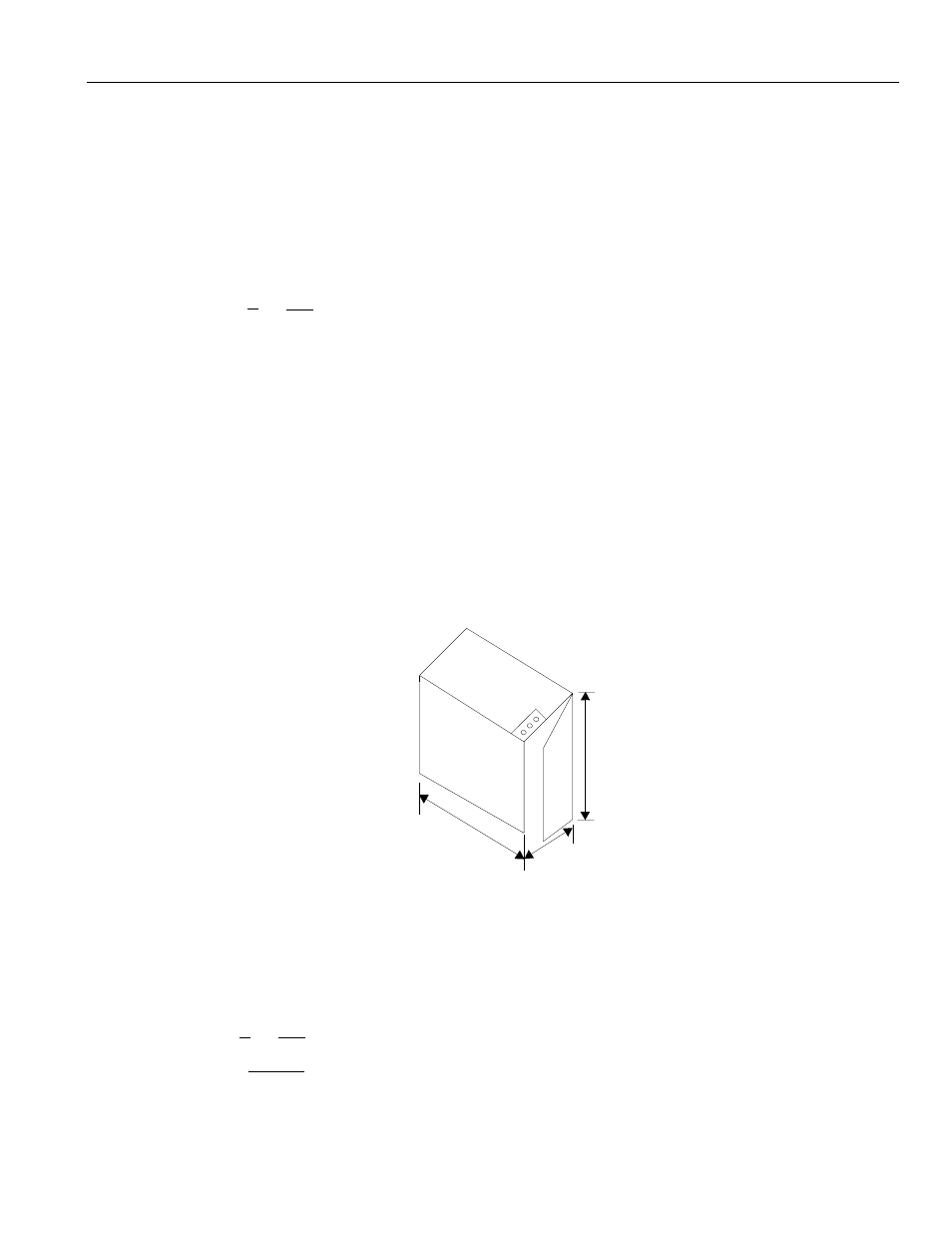
1 - 7
YASNAC PCNC Connecting ManualChapter 1: General
1.3 Thermal Design of Enclosure
1.3.1
Thermal Design
Design of the enclosure should be made on the basis that the average temperature increase of
air within the enclosure (containing the PC NC unit and other components) should be 10
o
C
below the external air temperature.
(1) Temperature Increase within the Enclosure (Average Temperature Increase)
The internal temperature increase (sheet metal enclosure) is generally as follows:
∆Τ=
P
qe
=
P
.
k A
where,
∆Τ :
Internal temperature increase (
o
C)
P : Heat generation in enclosure (W)
qe : Enclosure heat percolation ratio (W/
o
C)
k : Heat transit ratio of sheetmetal (W/m
2o
C)
6W/m
2o
C: With internal cooling fan
4W/m
2o
C: Without internal cooling fan
A : Efficient heat diffusion area of enclosure (m
2
)
1200
700
800
Efficient heat diffusion area is independently located, so bottom area is excluded.
A=4.16m
2.
If the heat generation in the enclosure is supposed to be 246W (113 W in CNC
portion, 104 W in servo portion, and 29 W in I/o portion),
qe
=
.
k A
∆Τ=
P
P
=
246
6 x 4.16
= 9.9 (
o
C)
All dimensions in millimeters
Fig 1.5 Dimensions of Enclosure