Unit description – BINDER FDL 115 User Manual
Page 19
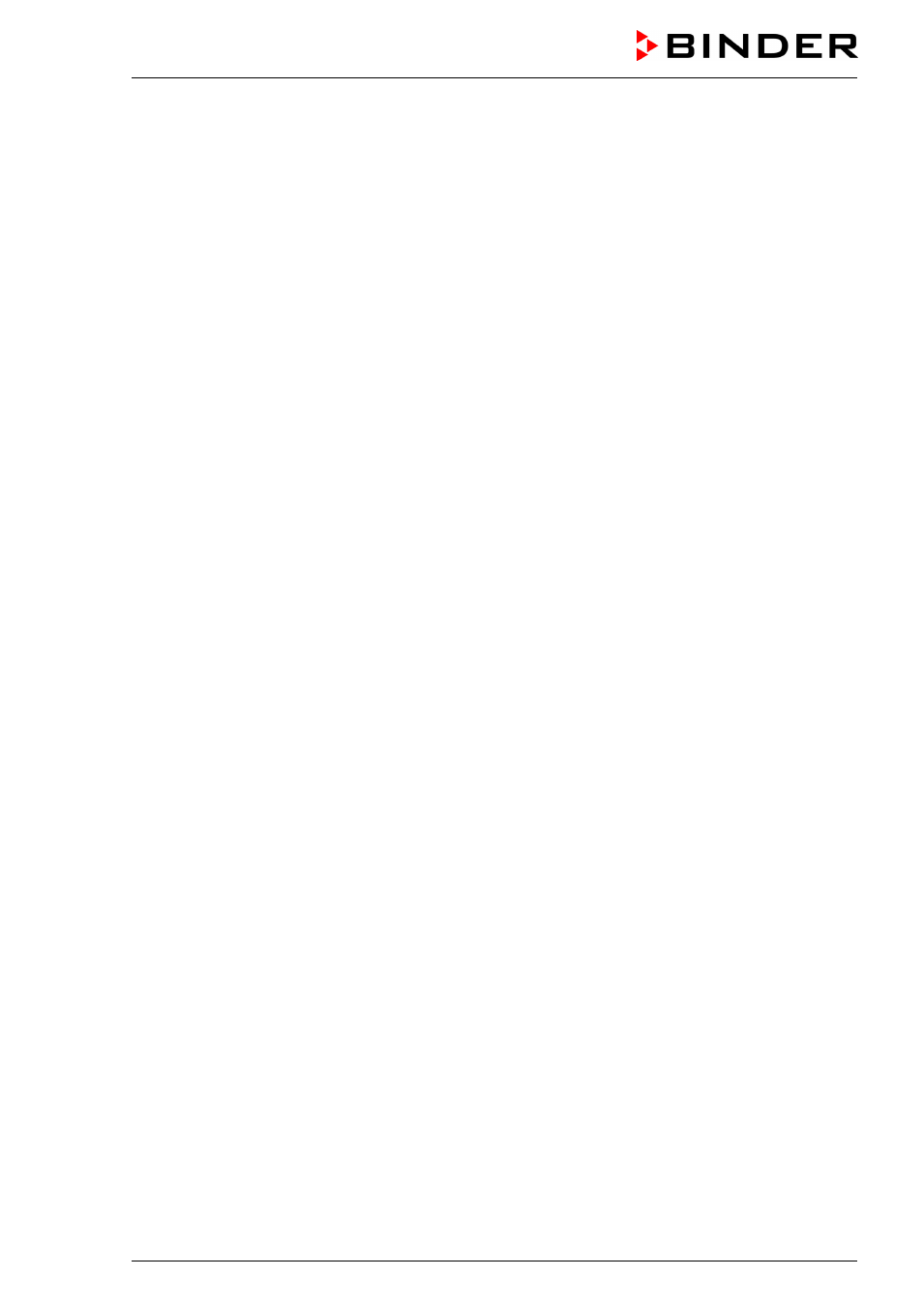
FDL (E2.1) 02/2015
page 19/75
2.
Unit description
The safety drying oven FDL 115 was built according to EN 1539:2009 (“Dryers and ovens, in which
flammable substances are released. Safety requirements”).
The fan in the rear of the safety drying oven delivers a constant amount of fresh air through the working
area irrespective of the drying temperature. A large-area filter removes dust from the incoming air (per-
meability up to approx. 1 micrometer).
A flow monitor in the upper part of the device (pressure differential switch) monitors the stream of exhaust
air. In the event of failure, the monitoring system turns the heater off immediately and shows this status
with a visual signal: red indicator light “AIR” (3) (see Figure 4).
After turning on the chamber with the main power switch, pressing the “START” pushbutton will start the
fan and the prepurge procedure. The indicator light “AIR” (3) in the operating panel lights up as long as
the heating has not yet been released by the air-flow monitoring. As an additional indication there is an
acoustical signal which can be reset on the controller with the “EXIT” key. The chamber heating is re-
leased after approx. 2 minutes of prepurge with monitoring the stream of exhaust air. When opening the
door, fan and heating turn off. To restart the drying process new prepurge is required.
The drying temperature is also monitored constantly by the temperature safety device (2). In case the
temperature exceeds the maximum permissible temperature, the heating will be turned off immediately
and this status registered by an audible and a visual signal – indicator light (2a). In case of failure, it is
impossible to restart the drying oven before the reset key (2b) was reset.
BINDER safety drying ovens with forced convection FDL are equipped with the electronic program con-
troller RD3 with digital display. This permits programming of temperature cycles.
The APT.line™ heating system ensures high level of spatial and time-based temperature precision,
thanks to the direct and distributed air circulation into the interior. The fan supports exact attainment and
maintenance of the required temperature accuracy.
All functions of the multifunctional program control can be set simply and conveniently via the easy to
understand function keypad of the RD3 temperature program controller. This controller is equipped with
touch function keys and a digital display and permits exact temperature setting and programming tem-
perature cycles. The FDL provides almost unlimited possibilities of adapting to individual customer re-
quirements based upon extensive programming options and on the week program timer and real time
clock of the controller.
All unit functions are easy and comfortable to use thanks to their clear arrangement. Major features are
easy cleaning of all unit parts and avoidance of undesired contamination.
The inner chamber and the interior side of the doors are made of stainless steel V2A (German material
no. 1.4301, US equivalent AISI 304). When operating the chamber at temperatures above 150 °C, the
impact of the oxygen in the air may cause discoloration of the metallic surfaces (yellowish-brown or blue)
by natural oxidation processes. These colorations are harmless and will in no way impair the function or
quality of the unit. The housing is RAL 7035 powder-coated. All corners and edges are also completely
coated.
The safety drying oven FDL comes equipped with a serial interface RS 422 for computer communication,
e.g. via the communication software APT-COM™ 3 DataControlSystem (option, chap. 13.1). For further
options, see chap. 17.4.
The units can be operated at an ambient temperature of 18 °C / 64.4 °F up to 40 °C / 104 °F in a temper-
ature control range by 5 °C above ambient temperature up to +300 °C / 572 °F.