Pid block description, Pid ideal and pid robust, Pid tuning parameters – Flowserve 400MD Logix User Manual
Page 53: Mode-restricted writes to pid parameters
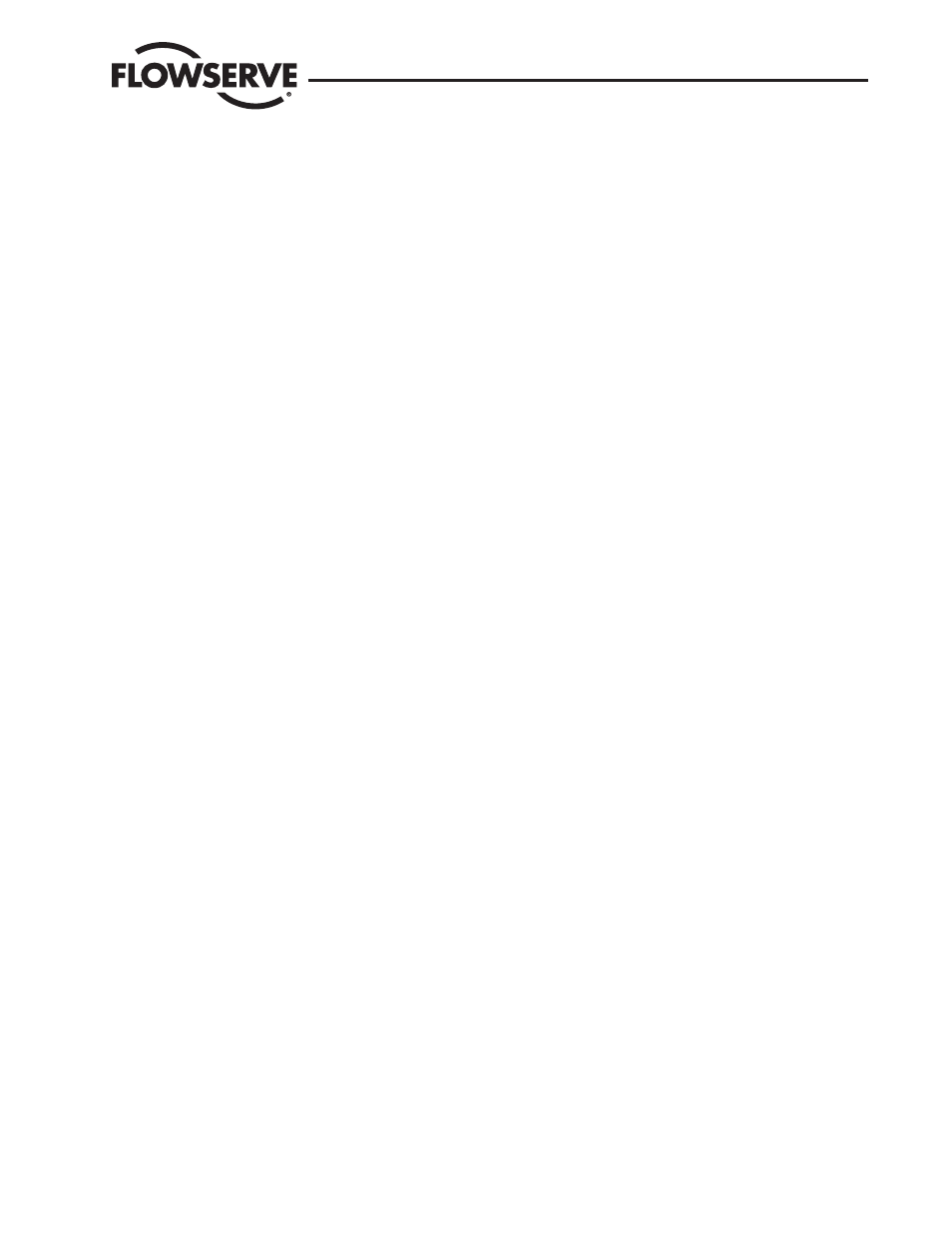
PID Block Description
PID control function block is an algorithm that produces an output signal in response to the measured variable and the set-point. The PID function block
allows the user to choose either a standard PID control equation (Ideal) or a robust PID equation defined by Honeywell. This selection is defined in the
PID_FORM parameter.
The output has three terms: Proportional, Integral and Derivative. The output is adjusted by tuning constants. Three tuning constants are
contained in the ideal PID equation.
The robust PID uses four tuning constants.
1. GAIN is the tuning constant of the Proportional term.
2. RESET is the tuning constant of the Integral term.
3. RATE is the tuning constant of the Derivative term. RATE is usually modified by a lag, which is set at some fixed ratio higher than the rate
time to create a rate gain. No lag occurs with the rate in this implementation.
4. OUT_LAG is the fourth tuning constant used in the robust PID, it adds roll off to the output response. The action is similar to PID with rate
gain.
PID Ideal and PID Robust
The ideal equation is a parallel or non-interacting implementation of PID control using three tuning constants. It automatically fixes OUT_LAG to 16 times
the RATE time constant. This produces response characteristics equivalent to the algorithms used in TPS products.
The robust equation is the same parallel implementation of ideal PID control but allows the engineer to set the OUT_LAG and effectively change the rate
gain.
ALGO_TYPE is a configuration parameter that contains one of three selected algorithm types, A, B, or C.
Where:
•
A RATE, GAIN and RESET all act on the error between set point and measured variable.
•
B RATE acts on the measured variable only, GAIN and RESET use the error.
•
C RATE and GAIN act on the measured variable only, and RESET uses the error.
PID Tuning Parameters
Table 8.10 lists the valid ranges for the tuning parameters for the PID block. Note that OUT_LAG parameter cannot be configured when ideal PID is
selected (PID_FORM = 1) and can be configured when robust PID is selected (PID_FORM = 2).
The values given for these tuning parameters are valid under the following conditions:
•
The values assume that the minimum configured PID function block execution period (Ts) is 0.125 seconds.
•
Algorithm type setting (i.e. A, B, or C) has no effect on the validation of these tuning parameters.
•
The PID function block will reject all values outside the ranges.
Mode-restricted Writes to PID Parameters
Writing to certain PID block parameters are restricted by the block’s TARGET and/or ACTUAL mode. The MODE_BLK.TARGET or MODE_BLK.
ACTUAL parameter must equal one of the modes in the ‘Write Restrictions Column’ in Table 8.8 before the user can write values to the pa-
rameters listed.
Note: Do not select anything in CONTROL_OPTS in order to set the PID action to reverse acting.
Logix 3400MD Digital Positioner LGENIM3405-02 11/13
53