6 minimizing positioning time, 1 autotuning, 2 servo gain – Yaskawa Sigma Mini User Manual
Page 93
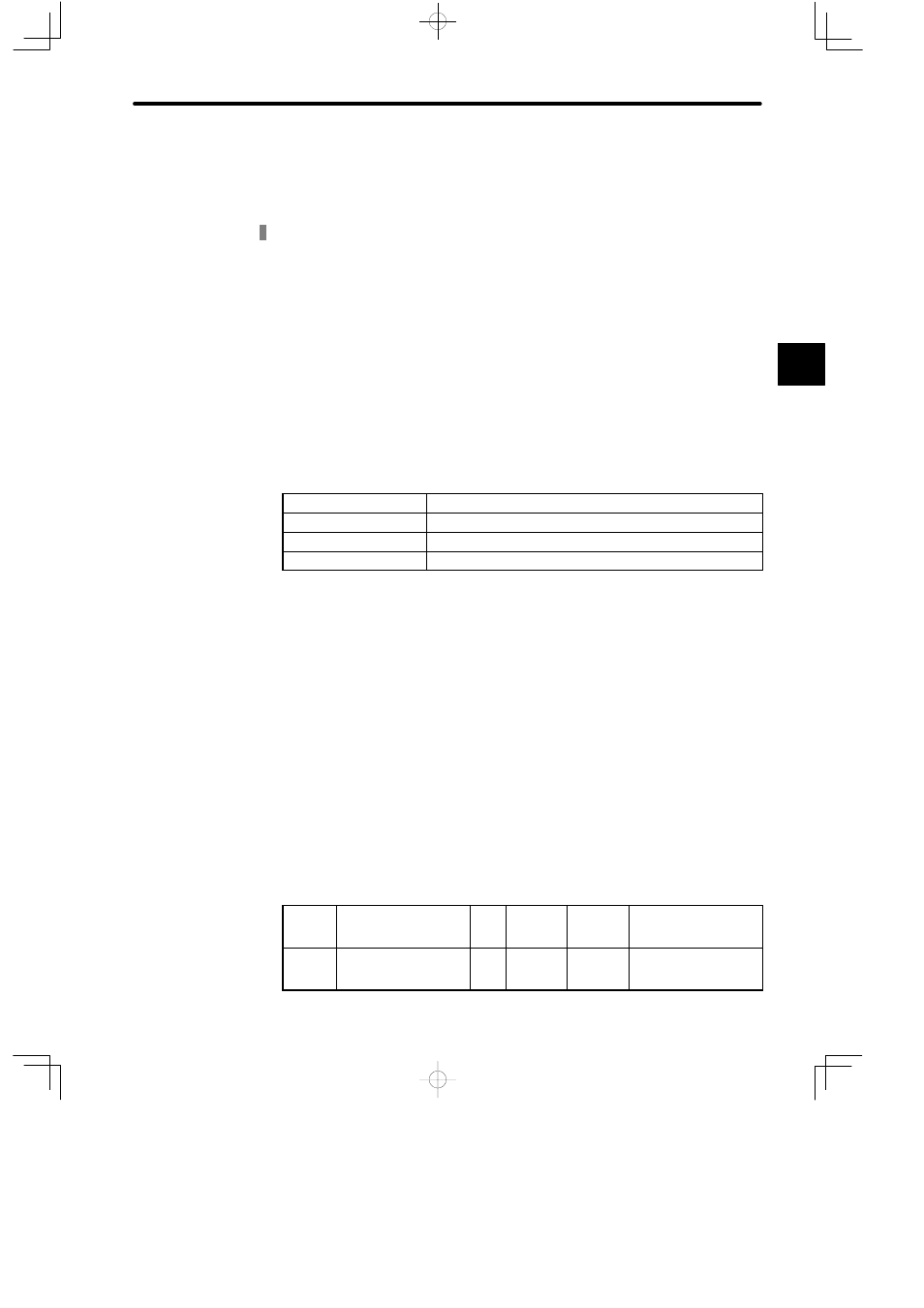
2.6Minimizing Positioning Time
— 2-49 —
2.6
Minimizing Positioning Time
This section describes how to minimize positioning time.
2.6.1 Autotuning
If speed loop gain and position loop gain for the servo system are not set properly, positioning
may become slow. Techniques and experience are required to set these servo gain values
according to machine configuration and machine rigidity.
Σ-Series Servopacks have an autotuning function that automatically measures machine
characteristics and sets the necessary servo gain values. With this function, even first-time
servo users can easily perform tuning for servo gain. Servo gain values are set in parameters.
The following parameters can be automatically set by the autotuning function.
Parameter
Meaning
Cn-04
Speed loop gain
Cn-05
Speed loop integration time constant
Cn-1A
Position loop gain
For details of how to perform autotuning, refer to 3.2.3 Autotuning
2.6.2 Servo Gain
Check and reset the servo gain when:
• Automatically set servo gain values need to be checked after autotuning.
• Each servo gain value checked after autotuning is to be directly set for another Servopack.
• Response performance needs to be further enhanced after autotuning, or servo gain val-
ues need to be reset for a system with lower response performance.
Setting Speed Loop
Set the following parameters related to speed loop as necessary.
Cn-04
LOOPHZ
Speed Loop Gain (Kv)
Unit:
Hz
Setting
Range: 1
to 2000
Factory
Setting:
80
For Speed/Torque
Control and Position
Control
Cn-05
PITIME
Speed Loop Integration
Time Constant (Ti)
Unit:
ms
Setting
Range: 2
to 10000
Factory
Setting:
20
For Speed/Torque
Control and Position
Control
2