6 cost of production and the major parameters, Ost of production and the major parameters – K-Patents SeedMaster 2 User Manual
Page 10
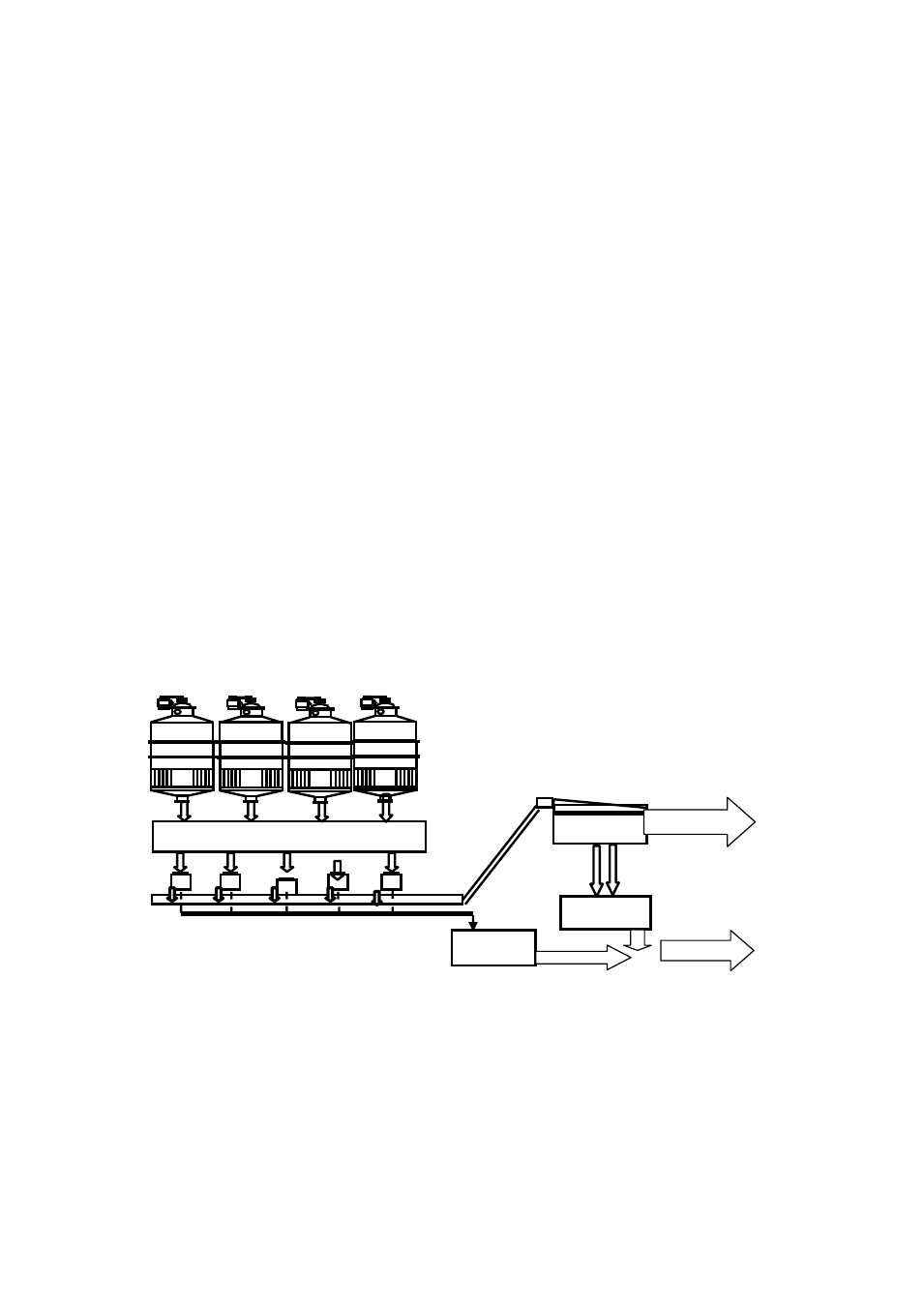
2 SUGAR CRYSTALLIZATION IN BRIEF
10
10
It has been proved that formation of conglomerates mostly happens when the size of the crystals is in the 40
to 250 micron range. This means that the formation of conglomerates in the early phase of crystallization
(not long after seeding) results in large conglomerates at the end of the strike, while smaller conglomerates
in the end product are due to unwanted nucleation (because of too high supersaturation) in the later phases
of the strike. Bad circulation, probably resulting in high local supersaturation in some parts of the pan also
contributes to the formation of conglomerates.
It is quite common nowadays that special products require well defined grain sizes, which call for a tight
crystal size distribution. This can be achieved by good boiling control (including, of course, good control of
supersaturation), or by screening of the product, if it has a wide size distribution. This later method, however,
requires additional machinery, time and energy and naturally increases the cost of production.
Besides wide crystal size distribution conglomerate content also contributes to poor product quality. It is well
known that the colour of the product has strong correlation to conglomerate content, because intergrown
crystals are more likely to retain some of the mother liquor during centrifuging. If conglomerate content is
high, product colour can only be improved with the excessive use of water in the centrifuges, which will
result – because of dissolution - in considerable loss of the crystal mass.
2.6 Cost of production and the major parameters
It has been demonstrated that wide crystal size distribution and conglomerates of varying sizes in the end
product are due to excessive supersaturation, which, if not controlled properly, can be present during the
complete course of crystallization (Figures 2.4 and 2.5). This proves that statements on the decreasing
importance of supersaturation after seeding has been completed are totally unfounded and false.
Conglomerate and fines content have very important effect on the cost of production. Too high fines content
makes centrifuging difficult and results in considerable loss of already crystallized sugar through the screen
baskets of the centrifuges. It is difficult to determine the amount of this loss and quite often it is neglected. It
should be realised, that the number of strikes per shift, often used in practice, is not a correct measure of the
rate of production. Fines and conglomerates result in recirculated sugar only to be melted, concentrated and
crystallized again, the end result of which is
•
waste of time and energy,
•
decreased effective yield of product sugar per strike and shift,
•
increased use of water and
•
increased cost of production.
Fig. 2.6
It is well known that the speed of crystallization is higher if supersaturation is higher, that is the rate of
production increases with increasing supersaturation. It is therefore tempting to push production by
maintaining high supersaturation, but exceeding the safe limit, where spontaneous nucleation begins and
the risk of conglomeration increases, too, is accompanied with the unpleasant consequences discussed
above.
Selecting the correct supersaturation set point trajectory for a strike is therefore a kind of compromise (or
optimisation). However, any type of supersaturation control is un-conceivable without the correct on-line
measurement of supersaturation.
Product
Crystals
Fines and
conglomerates
Recirculated
sugar
Tank
Green liquor
and fines
Product
screen
Melter
Mixer
Centrifugals