Vcm controller technical guide 45, Internal trend logging, Force modes or overrides – Orion System VCM Controller User Manual
Page 45
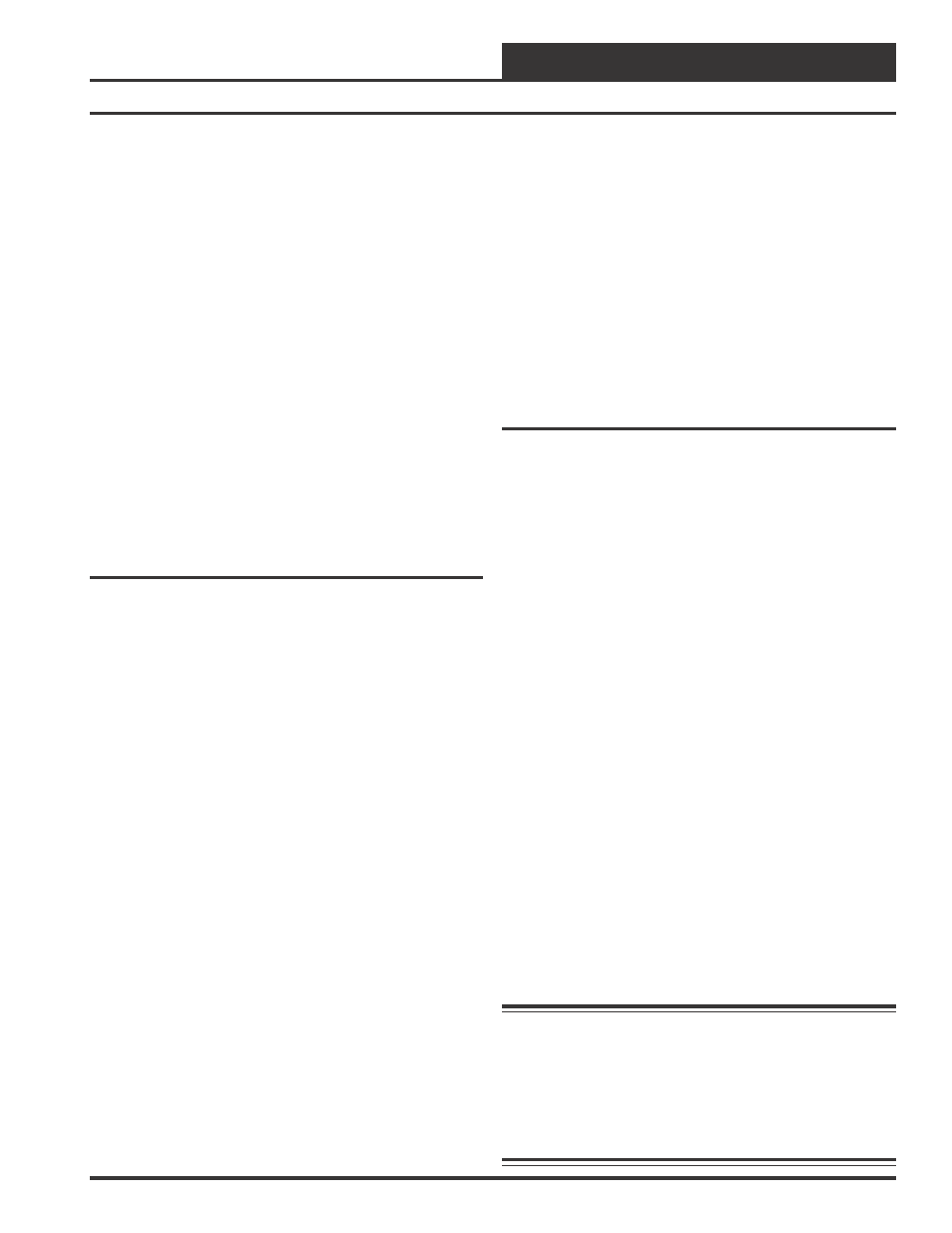
VCM Controller
Technical Guide
45
You can change the time on the VCM Controller through the Modular
Service Tool or the System Manager. You can also broadcast the time
and date to all VCM controllers by using a Personal Computer and the
PRISM II Computer Front End Software.
The Internal Scheduling in the VCM Controller also includes a Self
Teaching Optimal Start Routine that can be activated by entering a value
of 1.0 or greater for the Soak Multiplier Setpoint. The Optimal Start
function can only be used if your VCM Controller has a Space Tem-
perature Sensor installed and it is being used as the Controlling Sensor,
or you are using WattMaster VAV/Zone controllers with the VCM con-
troller. No adjustments other than the Soak Multiplier are required from
the user because the VCM Controller monitors how long it takes to
reach the Target Temperature each day and adjusts the Starting Time
accordingly. That means the first day you operate your HVAC unit it
will not be able to Optimally Start because it does not have a history of
previous Starts and their results. After the first day, the VCM Controller
will begin adjusting the Start Time, and after six Normally Scheduled
Starts have occurred, the Optimal Start Routine will have gathered
enough data to provide an accurate Pre-start based on the learned con-
ditions. This is an ongoing learning process of the six previous starts,
so the unit automatically adjusts for the changing seasons. If you don’t
need this feature but you are using the Space Temperature Sensor as the
Controlling Sensor, you can set the Soak Multiplier to zero to eliminate
the Optimal Start Routines.
Internal Trend Logging
The VCM Controller continuously maintains an Internal Trend Log,
which records a fixed set of values at an interval programmed by the
user. These values can be retrieved only with the PRISM II Computer
Front End Software. If you do not have a computer with PRISM II
Software installed and connected to the system communications loop,
you do not have access to these logs.
There are 120 log positions available. Once the last (120th) position
has been recorded, the log jumps back to the first position and begins
overwriting the old data. This means the user is required to retrieve the
logs at an interval that is shorter than the duration of the last 120 logs.
Shown below are some log intervals and the duration of 120 logs.
1 Minute Interval = 2 Hours
12 Minute Interval = 24 Hours
15 Minute Interval = 30 Hours
30 Minute Interval = 60 Hours
60 Minute Interval = 120 Hours
The fixed items in the log are listed below:
Date
Time
Space Temperature
Return Air Temperature
Outdoor Air Temperature
Active Cooling Setpoint
Active Heating Setpoint
Supply Air Temperature
Active Supply Air Temperature Setpoint
Outdoor Air Humidity
Indoor Air Humidity
Duct Static Pressure
Building Static Pressure
Economizer Signal Percentage
Supply Fan VFD/Zoning Bypass Damper Signal Percentage
Exhaust Fan VFD/Exhaust Damper Signal Percentage
Modulating Heat Signal Percentage
Modulating Cool Signal Percentage
On Board Relay Status (BIT Pattern )
Expansion Board Relay Status (BIT Pattern )
These items and values are explained in greater detail in the PRISM II
Computer Front End Software manual.
Force Modes or Overrides
The VCM Controller relay and analog outputs can be user overridden if
the Modular Service Tool or the PRISM II Computer Front-end Pro-
gram is used. The System Manager cannot be used for these Force
Modes. The Modes of operation for the relays are:
0 = Normal Operation
1 = Forced ON
2 = Forced OFF
The Analog Outputs are Forced if the user specifies a value between 0.0
and 10.0 VDC. To cancel the Force Mode, you must enter a value less
than 0 such as -1.0 VDC.
When the Analog Outputs are Forced, the display on the Modular Ser-
vice Tool or Prism II program can be interpreted as the actual voltage.
During normal operation, the display indicates the percentage signal
applied based on the user defined voltage limits. For example, if the
user defines a 2.0 VDC to 10.0 VDC range, then 50% would be 6.0
VDC instead of the 5.0 VDC applied when the range is 0.0 VDC to
10.0 VDC.
As previously mentioned, Force Modes can only be activated when
using either the Modular Service Tool or the PRISM II Computer Front
End Software. Furthermore, the Override condition can only remain in
effect as long as one of these Operator Interface devices is connected
and communicating with the VCM. That means that you cannot Force
an Override condition and then walk away from the equipment with the
Override still active. The loss of communications, removal or shutdown
of the Operator Interface will automatically terminate the Override within
10 minutes. This is to protect the equipment and to prevent an Override
condition from remaining active indefinitely resulting in inefficient or
dangerous operation of the equipment.
Warning: No equipment protection is available during the
Force Mode of operation. That means you
could start a compressor without running the
Supply Fan or create other conditions that
WILL damage the equipment. WattMaster
Controls, Inc. assumes no responsibility or
liability for the misuse of these user Overrides
that cause damage to the equipment!