Troubleshooting, 2 troubleshooting – Bronkhorst EL-FLOW Prestige User Manual
Page 47
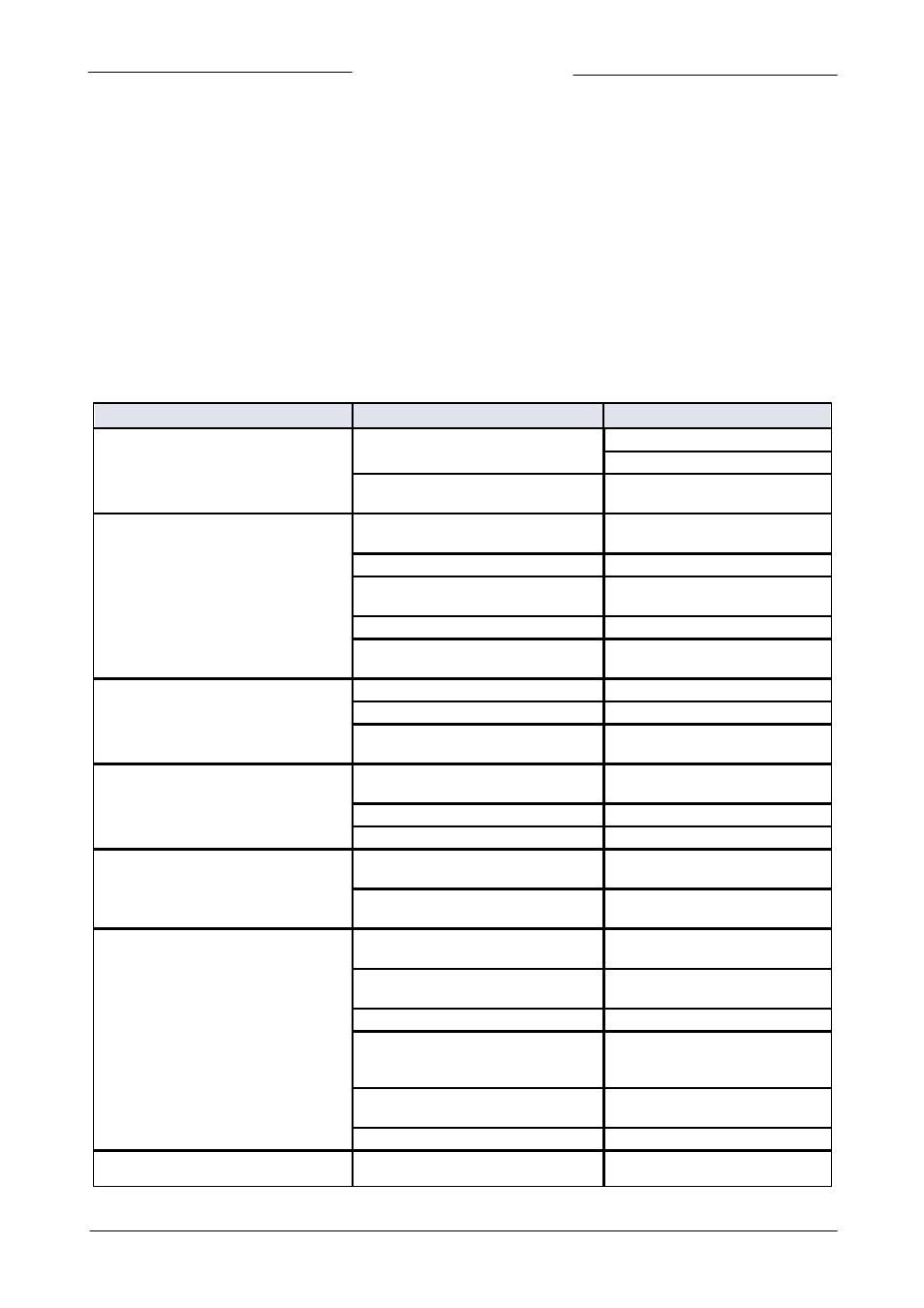
Bronkhorst High-Tech B.V.
EL-FLOW Prestige
47
9.17.084
5.2
Troubleshooting
In this section a number of possible errors/malfunctions of the instrument are listed.
LED indications
See section 3.7 for interpretation of specific LED indications of the instrument
Factory reset
In case (re)setting of the instrument has led to unexpected or non-recoverable behavior, it is possible to reset the instrument to the
settings applied at the factory during production. Use the 'Restore Settings' tab under 'Instrument Settings' in FlowPlot or use the
micro switch on top of the instrument (section 3.8) to restore the instrument to the original factory settings. Note that any
changes made to the instrument communication settings will not be restored after a factory reset. If digital communication with
the instrument can not be re-established, see section 3.4 to overrule the actual 9-pin sub-D communication settings with the
'Configuration Mode' (using the micro switch) and use the RS232 communication mode to re-establish communication.
Troubleshooting list
Symptom
Possible cause
Action
No power (LEDs not burning)
No power supply
Check power supply
Check cable connection
Internal fuse blown due to long lasting
shortage
Return to factory
Zero output signal
No setpoint accepted, incorrect control
mode
Check analog/digital control mode
(section 4.2.2)
No setpoint given, setpoint too low
Give setpoint >2%
Valve in 'Safe State' (normally closed
valves)
Remove cause of 'Valve Safe
State' (see section 3.1.2)
Pcb/sensor failure
Return to factory
Laminar flow element blocked/
contaminated
Return to factory
Maximum output signal (131.07%)
Flow too high, valve fully open
Close valve
Pcb/sensor failure
Return to factory
Valve in 'Safe State' (normally opened
valves)
Remove cause of 'Valve Safe
State' (see section 3.1.2)
Setpoint cannot be achieved
Pressure difference across instrument
insufficient to achieve requested flow rate
Check inlet/outlet pressure
Valve blocked or damaged
Return to factory
Stoppage
Remove contamination
Flow signal is gradually decreasing without
setpoint change
Pressure difference across instrument
insufficient to achieve requested flow rate
Check inlet/outlet pressure
Process gas condensation occurs
Decrease pressure or increase gas
temperature
Oscillating controller output
Controller adjustment wrong, PID settings
too fast
Set '
254
Controller Speed (Kspeed)' to
lower value
Inlet/outlet pressure too high or too low
Adjust pressure/set correct
instrument pressure with FlowTune
Wrong gas selected
Set correct process gas with FlowTune
Inlet pressure control is oscillating
Replace pressure regulator or increase
buffer volume between controller
instruments (section 2.3)
'Cross-talk' with other controller
instruments in process line
Increase buffer volume between
controller instruments (section 2.3)
Valve is damaged
Return to factory
Non-zero output signal when valve is closed Valve is leaking (through valve)
Check valve specifications for leak-