Cycle parameters – HEIDENHAIN TNC 320 (340 55x-04) Cycle programming User Manual
Page 202
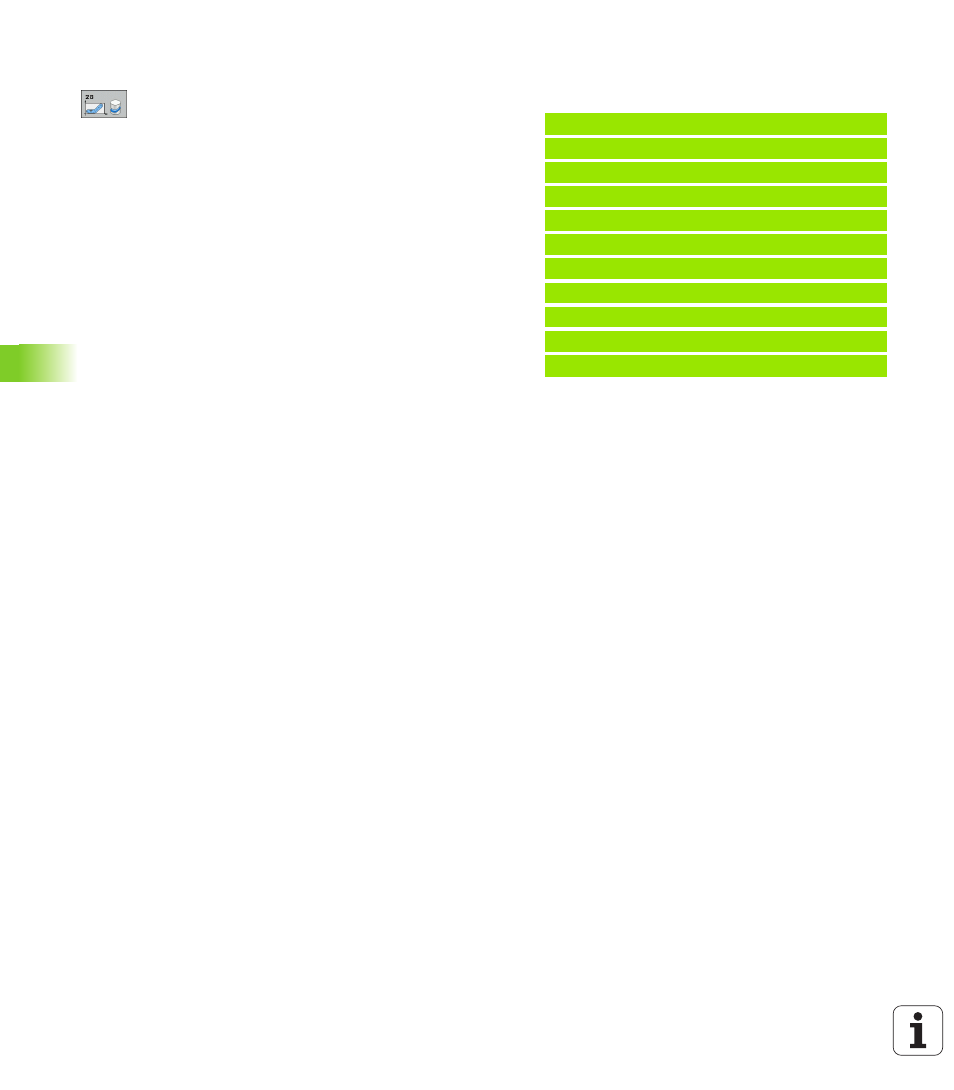
202
Fixed Cycles: Cylindrical Surface
8.3 C
Y
LINDER SURF
A
C
E Slot Milling (Cy
c
le 28, DIN/ISO: G128,
Sof
tw
a
re
-Option 1)
Cycle parameters
U
Milling depth Q1 (incremental): Distance between
the cylindrical surface and the floor of the contour.
Input range: -99999.9999 to 99999.9999
U
Finishing allowance for side Q3 (incremental):
Finishing allowance on the slot wall. The finishing
allowance reduces the slot width by twice the
entered value. Input range –99999.9999 to
99999.9999
U
Setup clearance Q6 (incremental): Distance between
the tool tip and the cylinder surface. Input range 0 to
99999.9999
U
Plunging depth Q10 (incremental): Infeed per cut.
Input range: -99999.9999 to 99999.9999
U
Feed rate for plunging Q11: Traversing speed of the
tool in the spindle axis. Input range 0 to 99999.9999,
alternatively FAUTO, FU, FZ
U
Feed rate for milling Q12: Traversing speed of the
tool in the working plane. Input range 0 to
99999.9999, alternatively FAUTO, FU, FZ
U
Cylinder radius Q16: Radius of the cylinder on which
the contour is to be machined. Input range 0 to
99999.9999
U
Dimension type? ang./lin. Q17: The dimensions for
the rotary axis of the subprogram are given either in
degrees (0) or in mm/inches (1).
U
Slot width Q20: Width of the slot to be machined.
Input range –99999.9999 to 99999.9999
U
Tolerance? Q21: If you use a tool smaller than the
programmed slot width Q20, process-related
distortion occurs on the slot wall wherever the slot
follows the path of an arc or oblique line. If you define
the tolerance Q21, the TNC adds a subsequent
milling operation to ensure that the slot dimensions
are a close as possible to those of a slot that has been
milled with a tool exactly as wide as the slot. With
Q21 you define the permitted deviation from this
ideal slot. The number of subsequent milling
operations depends on the cylinder radius, the tool
used, and the slot depth. The smaller the tolerance is
defined, the more exact the slot is and the longer the
remachining takes. Recommendation: Use a
tolerance of 0.02 mm. Function inactive: Enter 0
(default setting) Input range 0 to 9.9999
Example: NC blocks
63 CYCL DEF 28 CYLINDER SURFACE
Q1=-8
;MILLING DEPTH
Q3=+0
;ALLOWANCE FOR SIDE
Q6=+0
;SETUP CLEARANCE
Q10=+3
;PLUNGING DEPTH
Q11=100
;FEED RATE FOR PLNGNG
Q12=350
;FEED RATE FOR MILLING
Q16=25
;RADIUS
Q17=0
;TYPE OF DIMENSION
Q20=12
;SLOT WIDTH
Q21=0
;TOLERANCE