HEIDENHAIN TNC 320 (340 55x-04) Cycle programming User Manual
Page 236
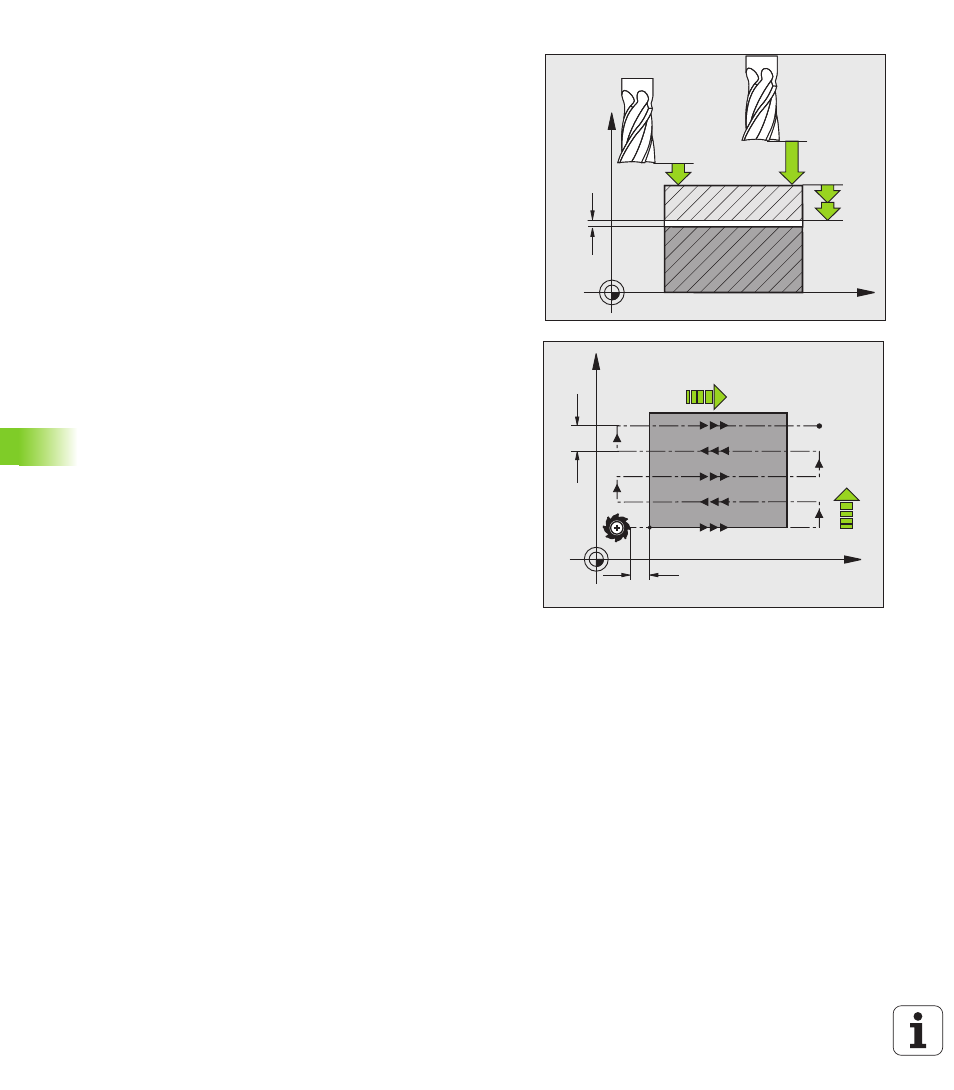
236
Fixed Cycles: Multipass Milling
1
0
.4 F
A
CE MILLING (Cy
c
le 232, DIN/ISO: G232)
U
Maximum plunging depth Q202 (incremental value):
Maximum amount that the tool is advanced each
time. The TNC calculates the actual plunging depth
from the difference between the end point and
starting point of the tool axis (taking the finishing
allowance into account), so that uniform plunging
depths are used each time. Input range 0 to
99999.9999
U
Allowance for floor Q369 (incremental): Distance
used for the last infeed. Input range 0 to 99999.9999
U
Max. path overlap factor Q370: Maximum stepover
factor k. The TNC calculates the actual stepover from
the second side length (Q219) and the tool radius so
that a constant stepover is used for machining. If you
have entered a radius R2 in the tool table (e.g. tooth
radius when using a face-milling cutter), the TNC
reduces the stepover accordingly. Input range 0.1 to
1.9999
U
Feed rate for milling Q207: Traversing speed of the
tool during milling in mm/min. Input range: 0 to
99999.9999; alternatively FAUTO, FU, FZ
U
Feed rate for finishing Q385: Traversing speed of the
tool in mm/min, while milling the last infeed. Input
range: 0 to 99999.9999; alternatively FAUTO, FU, FZ.
U
Feed rate for pre-positioning Q253: Traversing
speed of the tool in mm/min when approaching the
starting position and when moving to the next pass.
If you are moving the tool transversely to the material
(Q389=1), the TNC moves the tool at the feed rate for
milling Q207. Input range 0 to 99999.9999,
alternatively FMAX, FAUTO
X
Z
Q202
Q200
Q204
Q369
X
Y
Q357
Q253
Q207
k