1 introduction, 1 intr oduction 1.1 introduction – HEIDENHAIN TNC 320 (340 55x-04) Cycle programming User Manual
Page 36
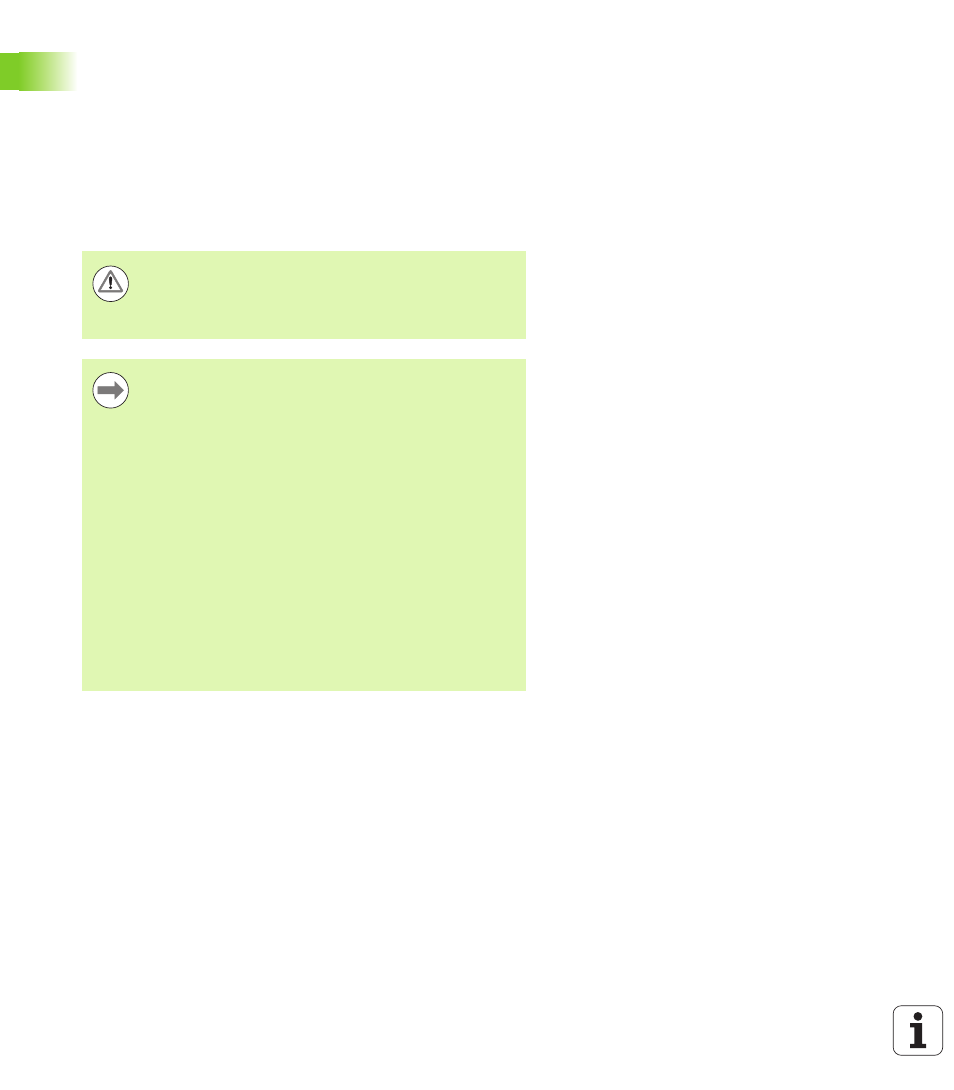
36
Fundamentals / Overviews
1
.1 Intr
oduction
1.1 Introduction
Frequently recurring machining cycles that comprise several working
steps are stored in the TNC memory as standard cycles. Coordinate
transformations and several special functions are also available as
cycles.
Most cycles use Q parameters as transfer parameters. Parameters
with specific functions that are required in several cycles always have
the same number: For example, Q200 is always assigned the setup
clearance, Q202 the plunging depth, etc.
Danger of collision!
Cycles sometimes execute extensive operations. For
safety reasons, you should run a graphical program test
before machining.
If you use indirect parameter assignments in cycles with
numbers greater than 200 (e.g. Q210 = Q1), any change in
the assigned parameter (e.g. Q1) will have no effect after
the cycle definition. Define the cycle parameter (e.g. Q210)
directly in such cases.
If you define a feed-rate parameter for fixed cycles greater
than 200, then instead of entering a numerical value you
can use soft keys to assign the feed rate defined in the
TOOL CALL
block (FAUTO soft key). You can also use the
feed-rate alternatives FMAX (rapid traverse), FZ (feed per
tooth) and FU (feed per rev), depending on the respective
cycle and the function of the feed-rate parameter.
Note that, after a cycle definition, a change of the FAUTO
feed rate has no effect, because internally the TNC
assigns the feed rate from the TOOL CALL block when
processing the cycle definition.
If you want to delete a block that is part of a cycle, the TNC
asks you whether you want to delete the whole cycle.