5 cycles for multipass milling – HEIDENHAIN TNC 310 (286 140) User Manual
Page 147
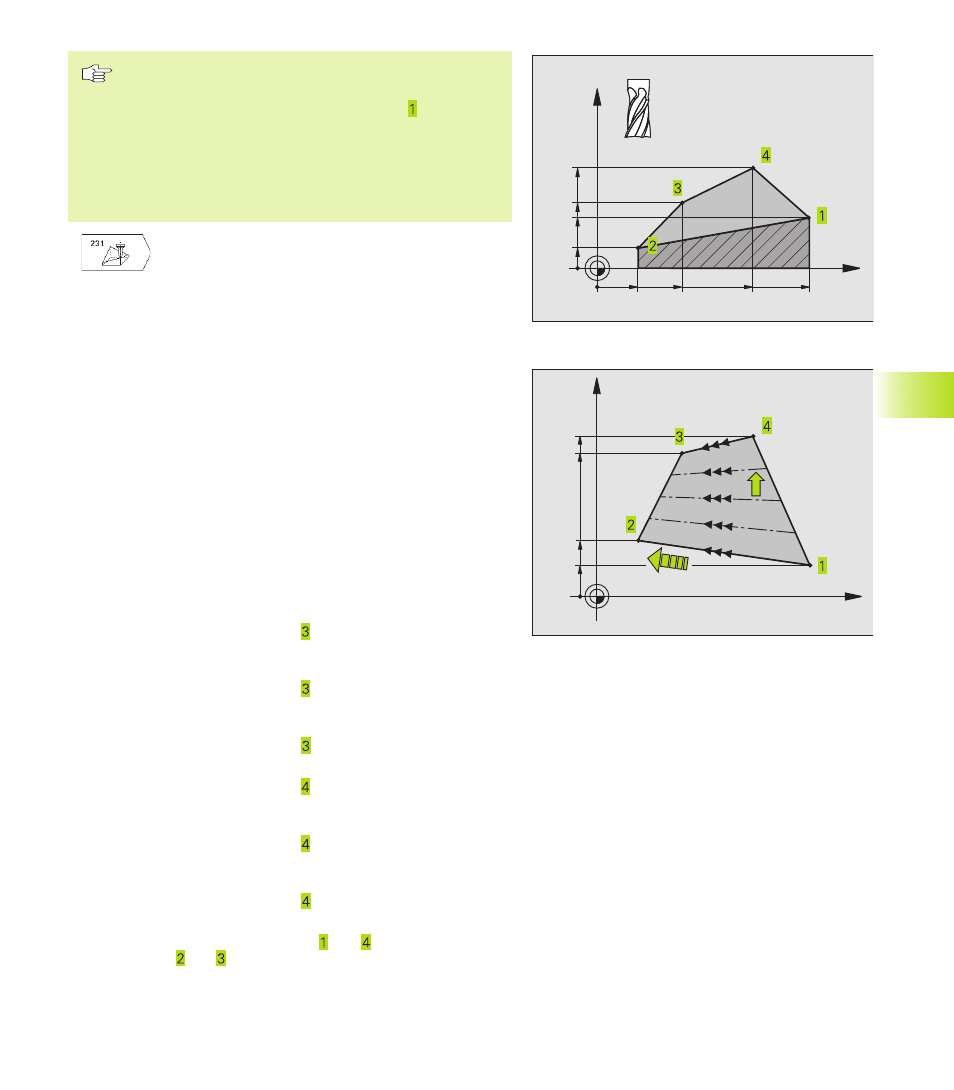
135
HEIDENHAIN TNC 310
Before programming, note the following:
From the current position, the TNC positions the tool in a
linear 3-D movement to the starting point 1. . Pre-position
the tool in such a way that no collision between tool and
clamping devices can occur.
The TNC moves the tool with radius compensation R0 to
the programmed positions.
If required, use a center-cut end mill (ISO 1641).
ú
Starting point in 1st axis Q225 (absolute value):
Starting point coordinate of the surface to be
multipass-milled in the main axis of the working
plane
ú
Starting point in 2nd axis Q226 (absolute value):
Starting point coordinate of the surface to be
multipass-milled in the secondary axis of the working
plane
ú
Starting point in 3rd axis Q227 (absolute value):
Starting point coordinate of the surface to be
multipass-milled in the tool axis
ú
2nd point in 1st axis Q228 (absolute value): Stopping
point coordinate of the surface to be multipass
milled in the main axis of the working plane
ú
2nd point in 2nd axis Q229 (absolute value): Stopping
point coordinate of the surface to be multipass
milled in the secondary axis of the working plane
ú
2nd point in 3rd axis Q230 (absolute value): Stopping
point coordinate of the surface to be multipass
milled in the tool axis
ú
3rd point in 1st axis Q231 (absolute value):
Coordinate of point in the main axis of the working
plane
ú
3rd point in 2nd axis Q232 (absolute value):
Coordinate of point in the subordinate axis of the
working plane
ú
3rd point in 3rd axis Q233 (absolute value):
Coordinate of point in the tool axis
ú
4th point in 1st axis Q234 (absolute value):
Coordinate of point in the main axis of the working
plane
ú
4th point in 2nd axis Q235 (absolute value):
Coordinate of point in the subordinate axis of the
working plane
ú
4th point in 3rd axis Q236 (absolute value):
Coordinate of point in the tool axis
ú
Number of cuts Q240: Number of passes to be
made between points and , and between points
and
8.5 Cycles for Multipass Milling
X
Y
Q229
Q207
N = Q240
Q226
Q232
Q235
X
Z
Q236
Q233
Q227
Q230
Q228
Q225
Q234
Q231
ú
Feed rate for milling Q207:
Traversing speed of the tool in mm/
min when milling the first pass. The
TNC calculates the feed rate for all
subsequent passes dependent of
the stepover factor of the tool (offset
less than tool radius = higher feed
rate, high stepover factor = lower
feed rate)