3 t ool compensation – HEIDENHAIN TNC 310 (286 140) User Manual
Page 64
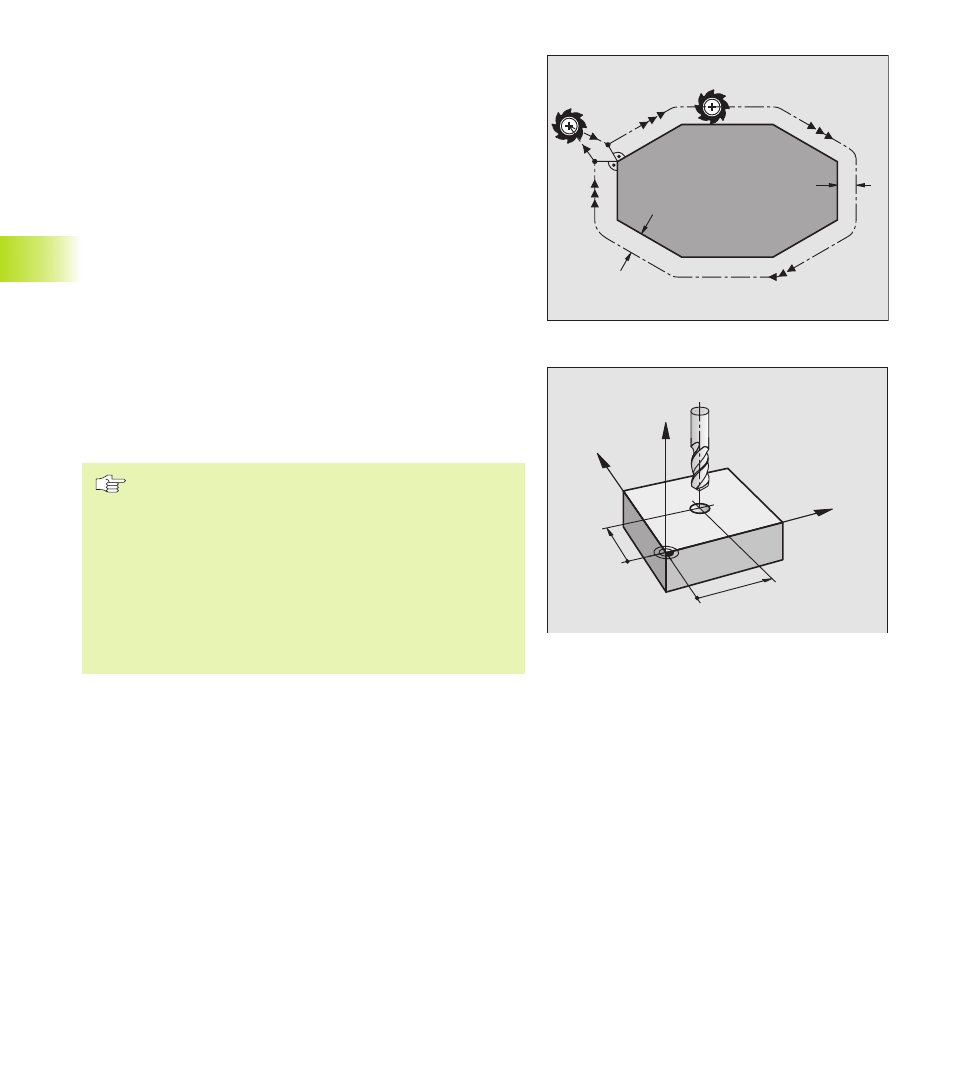
52
5 Programming: Tools
For tool radius compensation, the TNC takes the delta values from
the TOOL CALL block into account:
Compensation value = R + DR
TOOL CALL,
where
R
is the tool radius R from the TOOL DEF block or tool
table
DR
TOOL CALL
is the oversize for radius DR in the TOOL CALL block
(not taken into account by the position display)
Tool movements without radius compensation: R0
The tool center moves in the working plane to the programmed
path or coordinates.
Applications: Drilling and boring, pre-positioning
(see figure at center right)
Tool movements with radius compensation: RR and RL
RR The tool moves to the right of the programmed contour
RL The tool moves to the left of the programmed contour
The tool center moves along the contour at a distance equal to the
radius. “Right” or “left” are to be understood as based on the
direction of tool movement along the workpiece contour (see
illustrations on the next page).
Between two program blocks with different radius
compensations (RR and RL) you must program at least
one block without radius compensation (that is, with R0).
Radius compensation does not come into effect until the
end of the block in which it is first programmed.
Whenever radius compensation is activated with RR/RL
or canceled with R0, the TNC positions the tool
perpendicular to the programmed starting or end
position. Position the tool at a sufficient distance from
the first or last contour point to prevent the possibility of
damaging the contour.
5.3 T
ool Compensation
R
R
R0
RL
Y
X
Z
X
Y