Error code troubleshooting- 1 of 4 -15, Error code troubleshooting (1 of 4) – Hypertherm HD4070 Rev.8 User Manual
Page 162
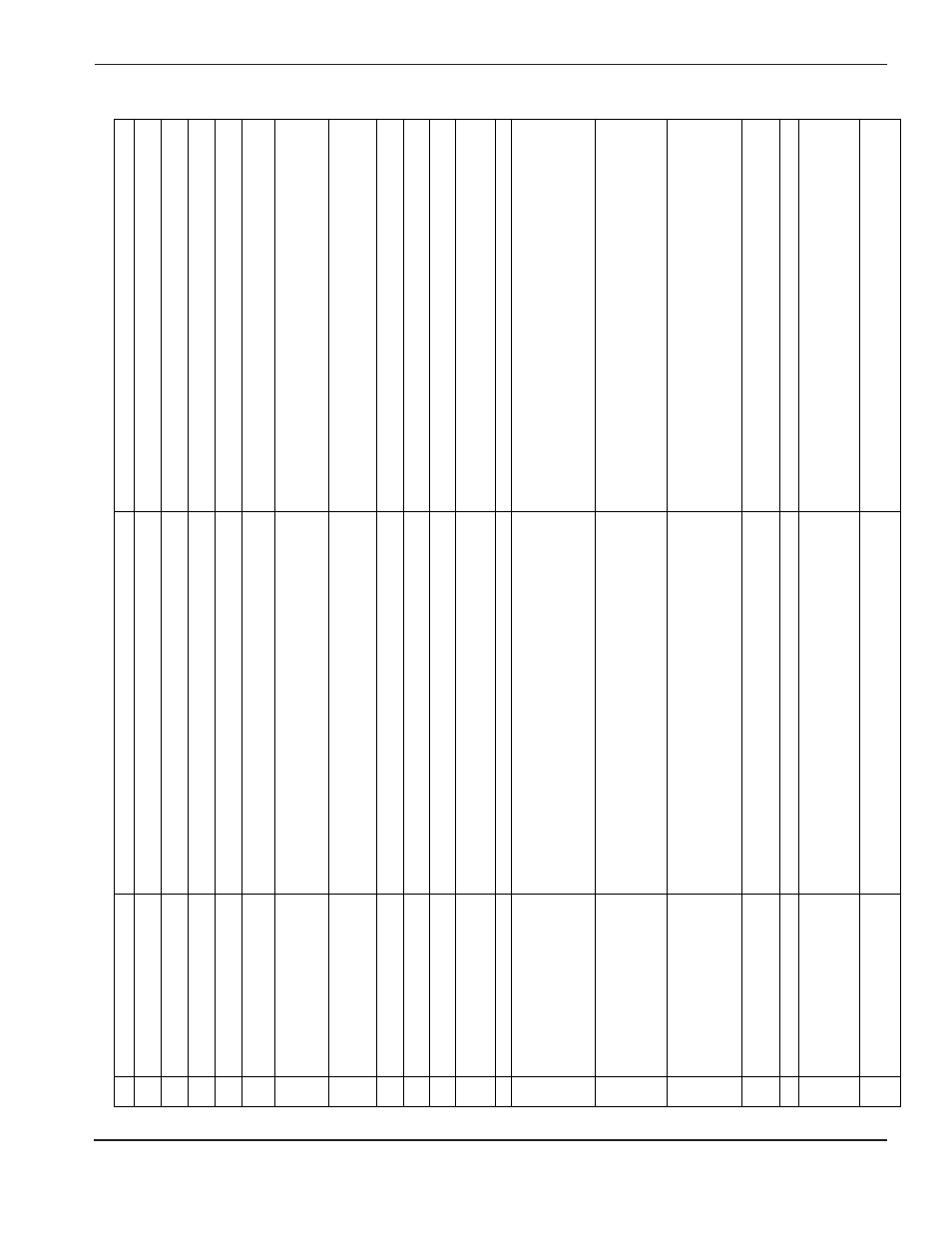
MAINTENANCE
HD4070
Instruction Manual
5-15
4
Error Code Troubleshooting (1 of 4)
ID #
Error Code or Message
Description
Corrective action
3
LOW PRESSURE WARNING
Supply gas pressure is 10psi (.34 Bar) under required specification. System
will continue to run.
Adjust supply gas pressure
4
HIGH PRESSURE WARNING
Supply gas pressure is 10psi (.34 Bar) over required specification. System
will continue to run.
Adjust supply gas pressure
5
LOW VOLTAGE WARNING
Input power is 15% under required specification.
Check for correct input power to power suppl
y
6
HIGH VOLTAGE WARNING
Input power is 15% over required specification.
Check for correct input power to power suppl
y
9
FLOW-SWITCH IS TESTED FOR
OFF CONDITION
Refer to error code #109.
Refer to error code #109.
20
NO PILOT ARC
Incorrect current setting, consumables, or gas preflow settings. Disconnected
or defective cables. Shorted consumables or torch head. Disconnected or
defective pilot arc relay, pilot arc controller or ignition console. Faulty SSR on
relay board, located in gas console.
(1) Verify current setting, consumables, or gas preflow settings. (2) Verify
that torch head or consumables are not shorted. (3) Make sure pins, sockets
and plugs are properly seated.
21
NO ARC TRANSFER
No current was detected by current sensor within 2 seconds of issuing
plasma start.
(1) Verify Proper initial height. (2) Verify all cables and wires for continuity,
including work cable and torch leads. (3) Properly seat pins, sockets and
plugs. (4) Replace faulty current sensor, plasma interface or breakout board.
22
PLASMA SYNC TIMEOUT
Plasma sync input from CNC controller has remained active and has delayed
ignition for over one minute.
Check CNC interface wiring and software.
23
LOST ARC BEFORE TRANSFER
Lost current from chopper 1 and/or 2 before arc transfer.
Position torch 4" to 8" above plate and perform chopper current test (See pg.
In the instruction manual).
24
LOST CURRENT
Loss of current from Chopper 1 or 2 after transfer was established. Signal
comes from control PCB.
(1) Perform chopper current test. (2) Verify that work cable is in good
condition and properly connected. (3) Check for defective torch leads.
26
LOST TRANSFER
Arc extinguished or current not sensed after transfer was established.
(1) Verify initial pierce height. (2) Check rampdown programming for errors.
(3) Check for defective torch leads. (4) Verify that work cable is in good
condition and properly connected.
27
LOST PHASE
System has detected a loss or drop of voltage on the incoming AC power.
Check contact points in main contactor and/o
r incoming power.
36
THC AT LOWER LIMIT
The Command THC uses proximity switches to detect upper and lower limits
of travel. During initial height sensing (IHS), the torch did not reach the work
piece and retracted to home position. During cutting the torch hits the lower
limit.
To verify proper operating proximity or switches, the torch must have full range
of travel. (1) Reposition torch so it contacts the workpiece during IHS.
(2) Check lower limit switch by changing THC to manual mode from operating
screen 13. Jog torch to lower limit position to activate switch. On THC control
PCB: LED- D50 should be on. Jog torch up to deactivate switch. D50 should go
off. If test fails, check lower limit switch and cable and Replace if required.
37
THC AT HOME LIMIT
During IHS the torch retracted or did not move from home limit
.
(1) Reposition torch in holder. (2) Try a lower IHS speed or a higher stall
force. (3) Check the home limit switch by changing THC to manual mode
from operating screen 13. Jog torch to home limit position to activate switch. On
THC control PCB: LED- D49 should be on. Jog torch down to deactivate switch.
D49 should go off. (4) If test fails, check home limit switch and cable and
Replace if required.
38
THC MOTION FAILURE
Torch did not reach home position during full retract. Encoder failed during a
cut.
(1) Verify that torch lifter motion is not blocked. (2) Test limit switch by
following step 3 above. (3) Check limit switch and cable, replace if required.
(4) Check for an encoder problem by changing THC to manual mode. Jog torch
up. On THC control PCB, lights D58 and D59 should blink alternately. If test
fails, check lower and home limit switches and replace if required. (5) Check
continuity of cable from lifter to control module.
39
NOZZLE CONTACT AT HOME
Ohmic contact wire shorted to ground.
(1) Verify that Ohmic contact wire is not shorted to ground. (2) Verify all
cables and wires for continuity. (3) Replace faulty plasma interface or THC
control board.
40
THC START AT INIT
THC start signal is ON during power up.
Check for shorting of THC ribbon cables.
41
THC MOTOR CURRENT FAULT
Cable not installed, External interlock not satisfied, Torch lifter motion
restricted, Motor drive PCB failure or Lifter motor failure.
(1) Check for cable installation and good connections. On THC control PCB,
Motor drive interface, D51 should be on. (2) On THC control PCB, Ext
interlock Ok, D16 should be ON, if not, jumper machine interface cable at CNC,
pins 19 and 37, on plug J6. (3) Verify that torch lifter motion is not restricted.
(4) Replace lifter motor or motor drive PCB.
44
LOW GAS PRESSURE
Gas pressure dropped below 105psi (7.2Bar). Interlock is tripped, the current
process is stopped and the arc is not allowed to fire.
Adjust supply gas pressure to specification. Check for pressure drop between
gas console and supply regulator. Recommend regulators be within 10
feet/3meters of gas console.
ID #'s 0-50:
The sytem does not shut do
wn when a w
a
rning message is displa
y
ed.
T
o
clear the message
, adjustments ma
y ha
v
e
to be
made
.