Hypertherm HD4070 Rev.8 User Manual
Page 197
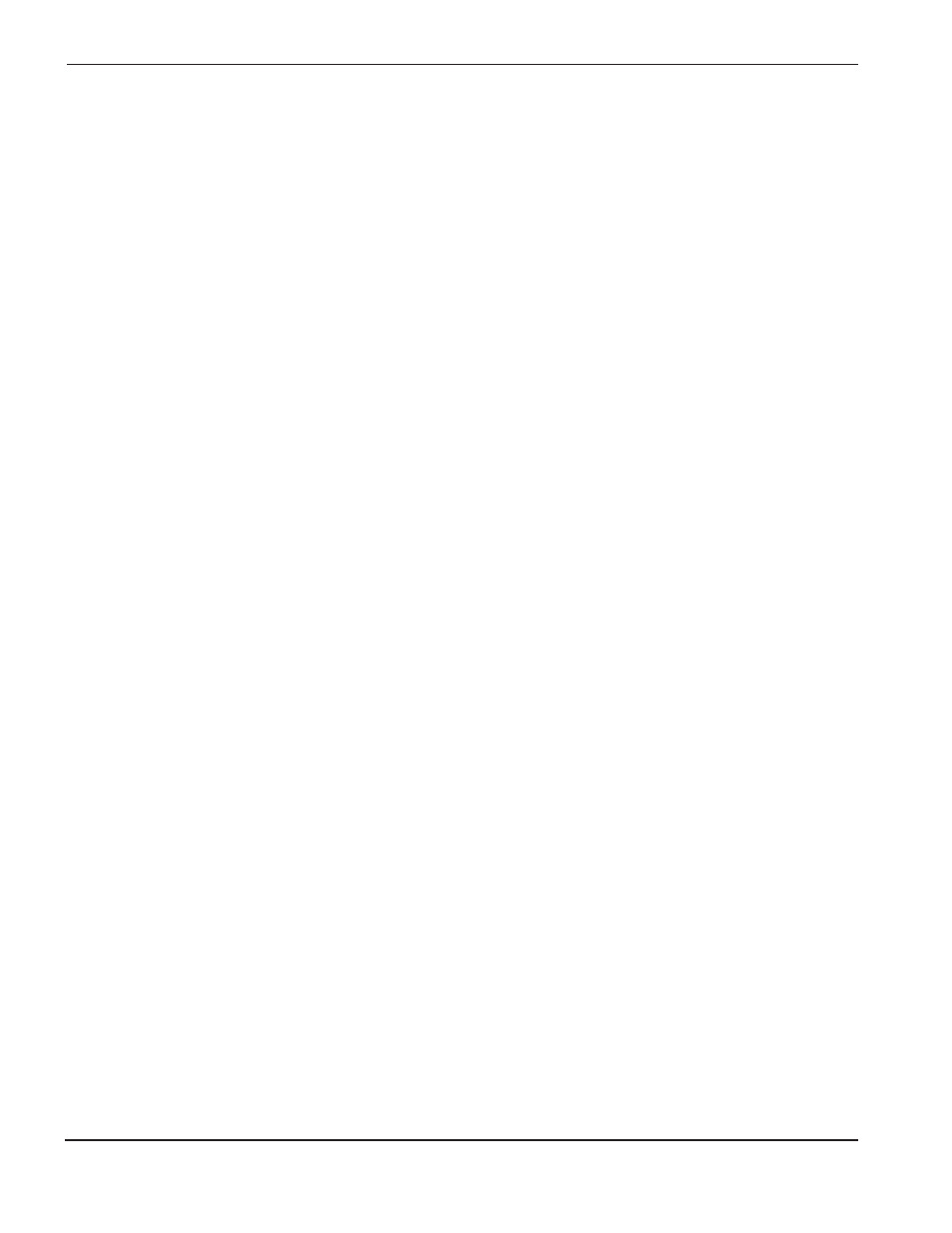
MAINTENANCE
5-50
HD4070
Instruction Manual
7
Coolant system
6. If the plasma equipment in question has a built-in coolant system, inspect the filter element of the coolant
system which is located at the rear of the power supply. If the filter has begun to turn a brownish color,
replacement should be recommended. For HyDefinition systems, a de-ionizing filter should be used. Refer to
the manual for proper part numbers. If the system is a MAX200 or HT2000, a particle filter should be used.
7. Perform a coolant flow test on the system. For MAX200, HT2000, HD1070 and HD3070 systems, flow should
be at least 0.75 gpm (2.8 l/min) on the return line. When testing systems with external water chillers, the
required coolant flow varies according to different size pumps. Refer to appropriate manuals.
Check for coolant leaks. Primary locations to inspect are: 1) the back of the power supply; 2) at the high-
frequency console, if applicable; and, 3) at the torch main body. Check the holding tank for dirt and
particulates. Verify that proper Hypertherm coolant is being used.
Torch main body
8. If the torch contains a water tube for electrode cooling, check the water tube to ensure that it is straight and
has no pitting on the end.
9. Check the current ring inside the torch main body. The current ring should be smooth and not pitted. If slight
pitting is seen, contact Hypertherm Technical Service to assess the likelihood that the torch could be repaired.
If no pitting is observed, clean the current ring with a clean cotton swab and clean water. Do not use alcohol.
Pitting on the current ring generally indicates improper maintenance (i.e. lack of regular cleaning).
10. Clean all threads on the front end of the torch head with clean water and a cotton swab, pipe cleaner or clean
cloth. Do not use alcohol. Damage to the threads usually results from not properly cleaning the torch and
retaining cap threads, so that dirt and particulates accumulate in the threads.
11. Inspect the torch insulator for cracks. Replacement of the torch should be recommended if cracks are found.
12. Inspect all o-rings on the torch body and consumables. Make sure that the correct amount of lubricant is being
applied to these o-rings. Too much lubricant may obstruct gas flows.
13. Ensure that the retaining or shield cap is tightened securely to the torch main body.
14. Check all hose fittings at the rear of the torch for wear. Damage to the fitting threads may indicate that
overtightening has occurred.
15. Ensure that all connections between the torch and torch leads are tight, but do not overtighten.
When removing consumables, always place them on a clean, dry, oil-free surface, since dirty consumables
may cause the torch to malfunction.
Gas flows
16. Check the plumbing from the gas supply source, as follows:
A. Remove and plug the oxygen inlet gas fitting at the gas console.
B. Pressurize the gas system at the source to 8.3 bar (120 psi).
C. Close the gas supply valve at the source. Watch for a pressure drop. If the supply line from the source is a
hose, there may be a 0.3 to 0.5 bar (5 to 7 psi) drop due to stretch.
D. If the pressure continues to drop, find the leaks in the system.