Yaskawa Sigma-5 Large Capacity Users Manual: Design and Maintenance-Command Option Interface User Manual
Page 199
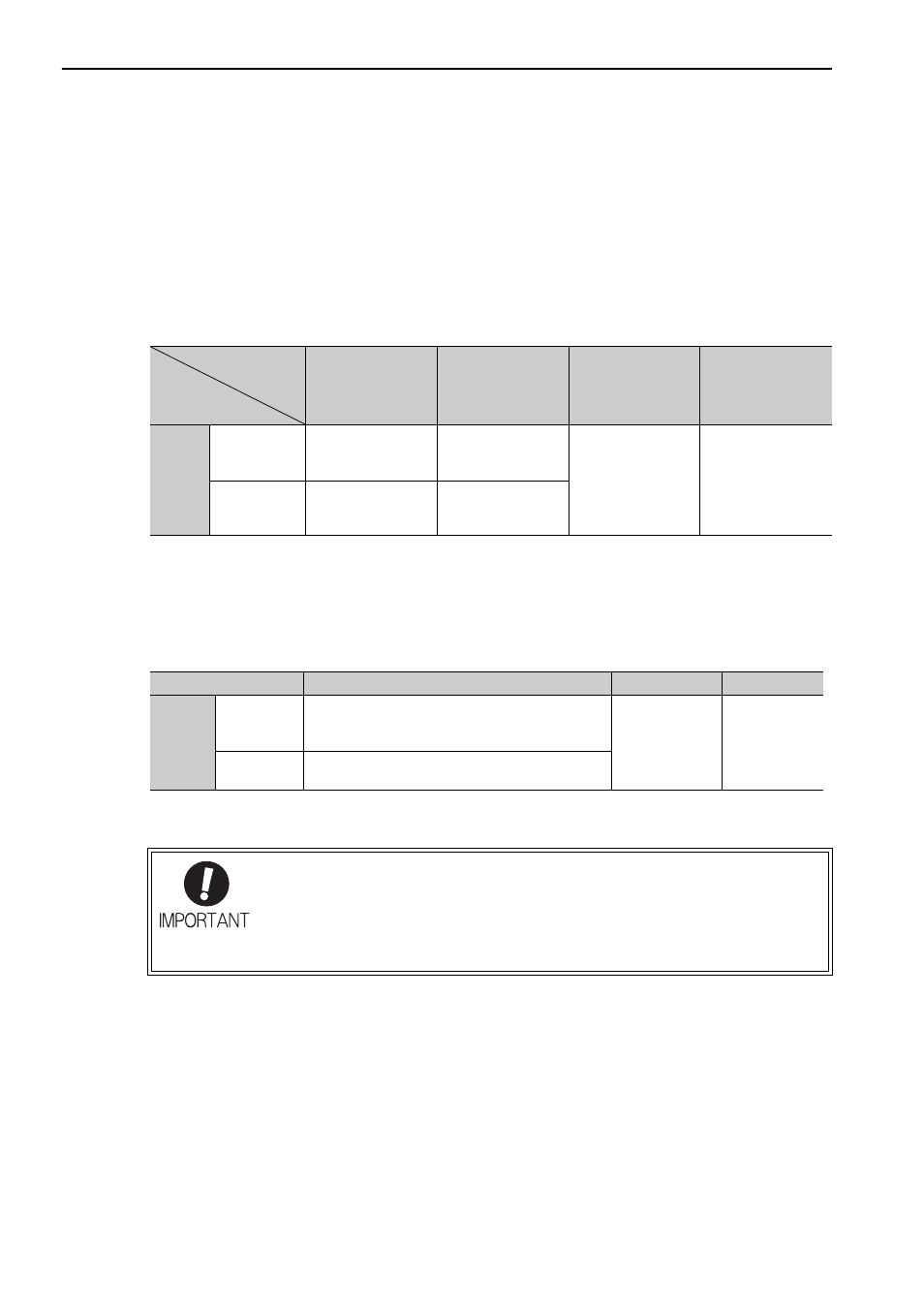
5 Adjustments
5.5.2 One-parameter Tuning Procedure
5-40
Friction Compensation
This function compensates for changes in the following conditions.
• Changes in the viscous resistance of the lubricant, such as the grease, on the sliding parts of the machine
• Changes in the friction resistance resulting from variations in the machine assembly
• Changes in the friction resistance due to aging
Conditions to which friction compensation is applicable depend on the tuning mode. The friction compensa-
tion setting in F408.3 applies when the mode is 0 or 1. Tuning Mode = 2 and Tuning Mode = 3 are adjusted
with the friction compensation function regardless of the friction compensation setting in P408.3.
Feedforward
If Pn140 is set to the factory setting and the tuning mode setting is changed to 2 or 3, the feedforward gain
(Pn109), speed feedforward input, and torque feedforward input will be disabled.
Set Pn140.3 to 1 if model following control is used together with the speed feedforward input and torque feed-
forward input from the host controller (through the command option module).
For details on the speed feedforward input and the torque feedforward input, refer the the manual of the con-
nected command option mocule.
Tuning Mode = 0
Tuning Mode = 1
Tuning Mode = 2
Tuning Mode = 3
Pn408
n.0
[Factory
setting]
Adjusted without the
friction compensation
function
Adjusted without the
friction compensation
function
Adjusted with the
friction compensation
function
Adjusted with the
friction compensation
function
n.1
Adjusted with the
friction compensation
function
Adjusted with the
friction compensation
function
Mode
Friction
Compensation
Selecting
Parameter
Function
When Enabled
Classification
Pn140
n.0
[Factory
setting]
Model following control is not used together with the
speed/torque feedforward input.
Immediately
Tuning
n.1
Model following control is used together with the
speed/torque feedforward input.
• Model following control is used to make optimum feedforward settings in the SERVO-
PACK when model following control is used with the feedforward function. Therefore,
model following control is not normally used together with either the speed feedfor-
ward input or torque feedforward input from the host controller. However, model fol-
lowing control can be used with the speed feedforward input or torque feedforward
input if required. An improper feedforward input may result in overshooting.