5 integral gain, Values: 0.00 to 10.00 (repeats per minute), Default value = 1.00 – TE Technology TC-720 User Manual
Page 34
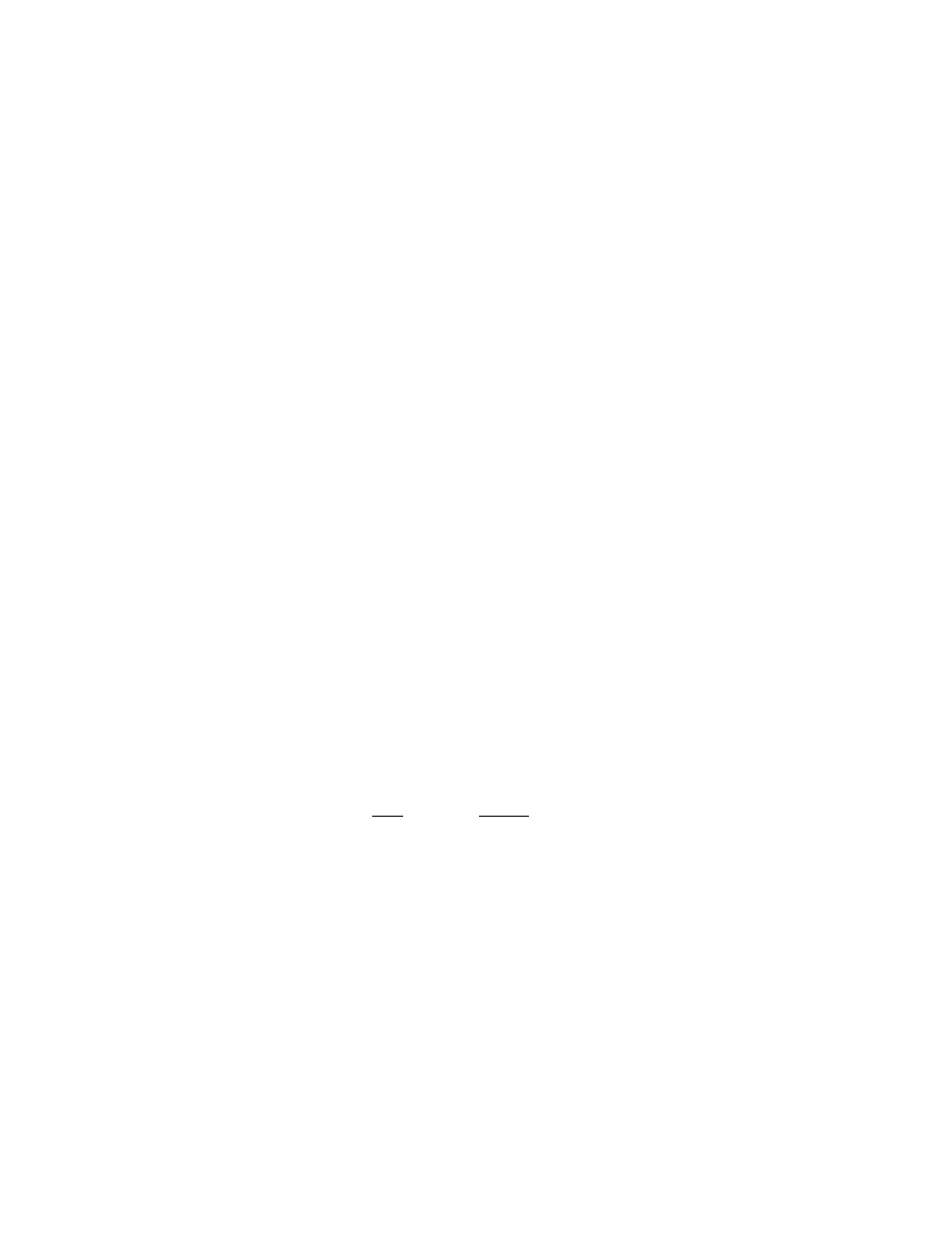
output power. The power will be reduced to 0% when the sensor is at 10.0 °C. If the temperature were to
decrease further, the power would proportionally increase up to +100% (heating mode) if the sensor is at 7.5°C.
(Of course, this example presumes that the INTEGRAL GAIN and DERIVATIVE GAIN are set to zero.)
In practice, the temperature would usually begin to oscillate at some offset from the set point because some
amount of power would always be required to achieve some amount of cooling. The offset is corrected by applying
INTEGRAL GAIN.
If the bandwidth is set too narrow, the temperature will oscillate around the set point. If the bandwidth is too
wide, the controller will be slow to respond or may never reach set point despite INTEGRAL GAIN and/or
DERIVATIVE GAIN settings.
NOTE: The controller uses a bandwidth adjustment in the control algorithm, which is inversely related to the gain.
A smaller bandwidth means a higher gain, and a larger bandwidth means a lower gain.
2.4.5
INTEGRAL GAIN
Values: 0.00 to 10.00 (repeats per minute)
Default value = 1.00
A value 0.00 turns this factor off in the PID algorithm
Description: With just proportional control, the controller’s output would be 0% when the actual temperature
reaches the set temperature. However, some non-zero output power is almost always required to reach the set
point, so using only proportional control would not allow the controller to maintain a stable set point. Therefore,
introducing an integral gain allows for an output power other than 0% when the actual temperature reaches the
set temperature.
The integral function applies an additional amount of output power up at a rate determined by multiplying the
error, the proportional bandwidth, and the integral gain.
For example, suppose the set temperature is 10.0 °C, the bandwidth is set to 5 °C, and the controller oscillates at
around 11.2 °C, corresponding to 48% power with only the PROPORTIONAL BW set.
The error is 1.2 °C, based on the difference between the set point and the temperature the controller settles at
(11.2 °C – 10 °C = 1.2 °C). The proportional bandwidth as used in the equation is 100%/2.5 °C = 40%/°C (the 2.5 °C
is half the total proportional bandwidth). Lastly, let us assume that the integral gain control is then set to 1 repeat
per minute. Thus we have the following:
40%
°𝐶 × 1.2 °𝐶 ×
1
𝑚𝑖𝑛𝑢𝑡𝑒
= 48% 𝑚𝑖𝑛𝑢𝑡𝑒
�
In this example, after one minute of operation the controller calculated that the difference between the desired
set temperature and the actual temperature was +1.2 °C. The INTEGRAL GAIN added an additional 48% output per
minute. This additional 48% output was added to the existing 48% output to yield 96% output. The integral
portion of the output is continuously recalculated at the rate specified by the integral gain setting. The INTEGRAL
GAIN always adds or subtracts from the present output power. Of course, the maximum output is limited to 100%
and the minimum is limited to 0%.
If the integral control is set too high, the temperature will oscillate. If integral control is set too low, it will take a
long time for the temperature to settle to steady state.
34