0 controller tuning, Controller tuning – TE Technology TC-720 User Manual
Page 39
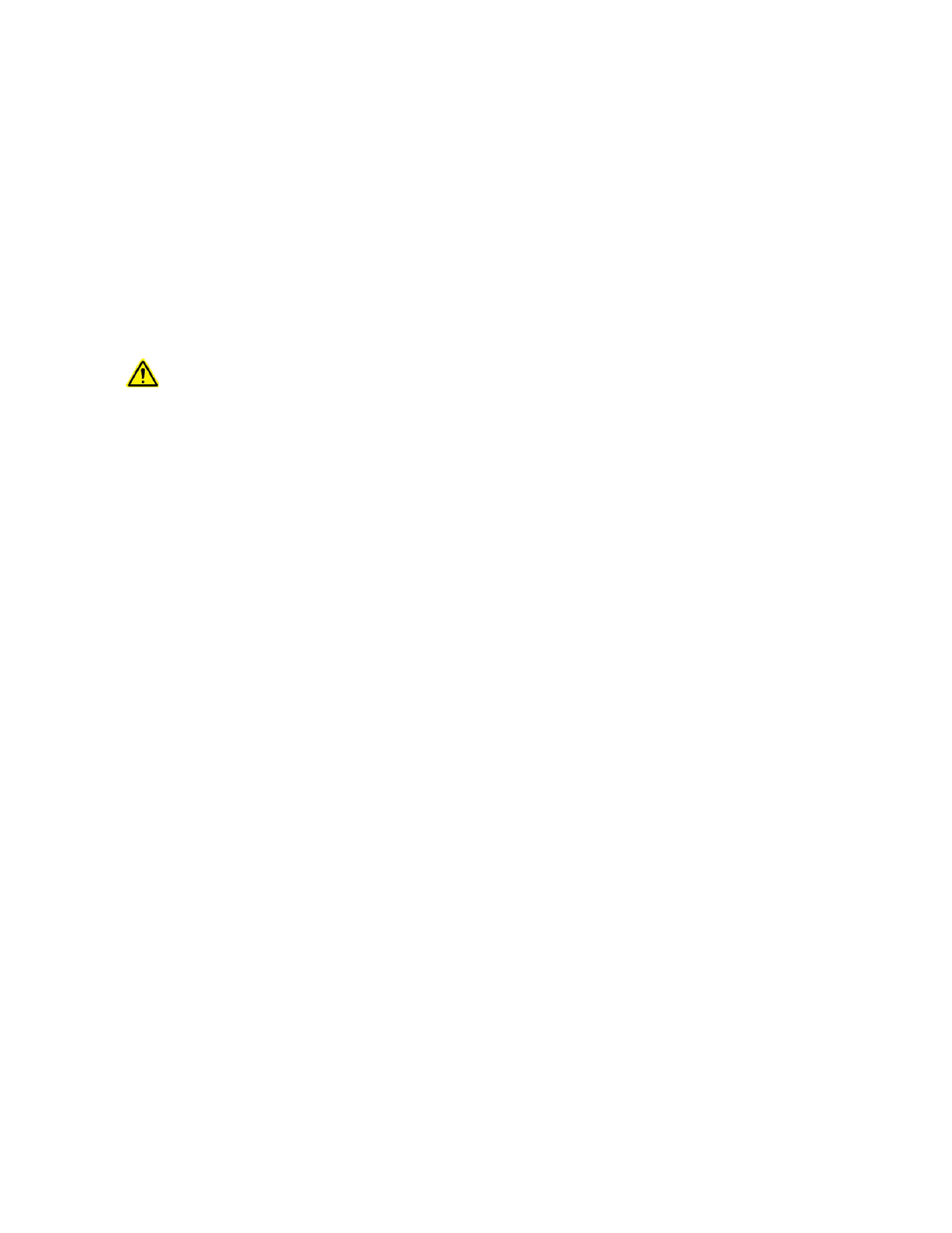
3.0 Controller Tuning
This tuning method follows the Ziegler-Nichols closed-loop tuning principals. Briefly, the controller will first be set to
a high proportional bandwidth setting with no integral or derivative function (integral gain and derivative gain = 0).
Then, the bandwidth is gradually decreased until the temperature approaches set point and a small, sustained
oscillation in temperature is observed. The other tuning parameters are then readjusted based on the time period of
the temperature oscillation (natural period) and the proportional bandwidth needed to cause this oscillation.
Remember, the controller uses a bandwidth adjustment in the control algorithm. This is the inverse of gain. A
smaller bandwidth means a higher gain, and a larger bandwidth means a lower gain. This should be kept in mind if
reviewing online tutorials regarding Ziegler-Nichols closed-loop tuning principals.
Improper tuning of this temperature controller can lead to excessive thermal cycling and/or overheating of
the thermoelectric device, either of which are known to reduce the lifetime of any thermoelectric device.
Care should be taken to prevent the temperature of the thermoelectric device from going beyond the range
specified by the device manufacturer. Care should also be taken so that any thermal cycling of the
thermoelectric device is a result of changes in the controller’s set-point temperature and not instability at a
given set point due to improper selection of the tuning variables.
3.1
Set the desired control temperature in the SET TEMPERATURE menu.
3.2
Set the PROPORTIONAL BW to 20. This is just a starting value; the goal is to determine the proportional bandwidth at
which the temperature of the TE device will first begin to oscillate. You might be able to start with a smaller
bandwidth, depending on the system, thereby reducing the time it takes to determine the proper bandwidth for
good control stability.
3.3
Set the INTEGRAL GAIN and DERIVATIVE GAIN to zero.
3.4
Decrease the PROPORTIONAL BW incrementally, allowing the TE device to reach steady state at each increment,
until the temperature of the TE device begins to steadily oscillate. The system temperature will usually begin to
oscillate before it actually reaches the set point temperature; this is normal. Initially, the bandwidth can be
decreased in initial increments of 5 °C or perhaps even more. Then, once an initial oscillation is observed, increase
the bandwidth in small increments until the amplitude of the oscillation is as small as possible but still definitely
sinusoidal.
Measure the time period of the oscillation in minutes. This will be used to determine the INTEGRAL GAIN setting
below.
3.5
Multiply the current PROPORTIONAL BW setting by 2.2 and enter this as the new bandwidth. The system should now
maintain a steady state temperature near the set point.
3.6
The integral gain is calculated as follows: I = 0.54/T where I is the integral gain and T is the time period, in minutes,
determined in section 3.4 above. Enter this value in the INTEGRAL GAIN setting.
3.7
The derivative gain is often times difficult to use and might cause more trouble than it is worth. If you are not
experienced with process control, you might be better off leaving the DERIVATIVE GAIN set to zero.
If you decide to use derivative gain, the other control parameters should be adjusted first.
a) Instead of multiplying the initial proportional bandwidth setting by 2.2, multiply it by 1.7, and enter this as
the new PROPORTIONAL BW setting.
b) Calculate the integral gain as follows: I = 1.2/T, and enter this into the INTEGRAL GAIN setting.
c) Calculate the derivative gain as follows: D =0.075 x T, and enter this into the DERIVATIVE GAIN setting.
39