Frequency reference control, Torque reference control – Yaskawa DeviceNet Option Card CM05x User Manual
Page 52
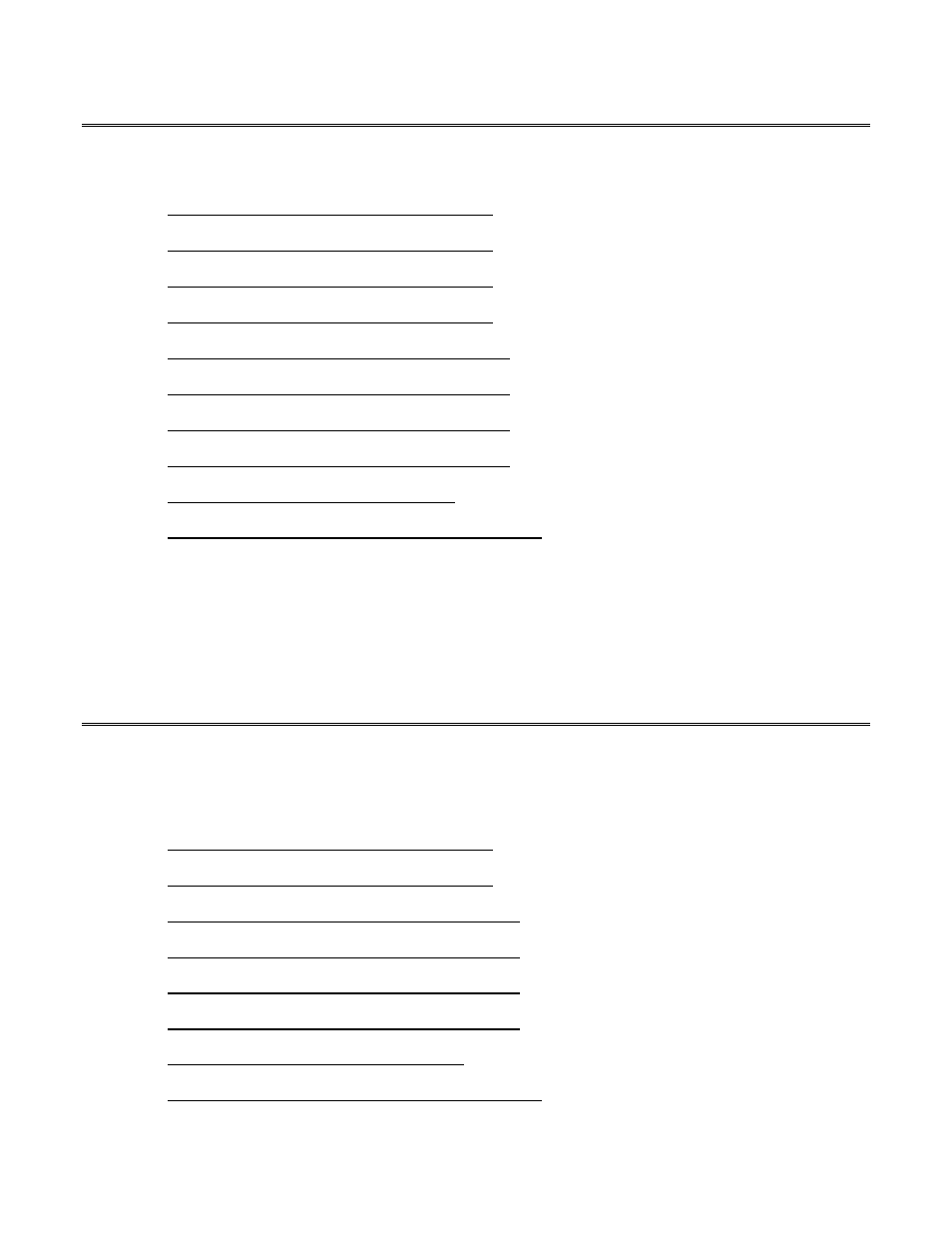
Drive Operation on DeviceNet 7-11
Frequency Reference Control
When controlling the speed of the Drive from the DeviceNet network, frequency reference can be accessed in
various ways:
1. Assembly 20 (Class 4, Instance 20, Attribute 3)
Bytes 2 and 3 of this assembly provide speed control in RPM. See Appendix B.
2. Assembly 21 (Class 4, Instance 21, Attribute 3)
Bytes 2 and 3 of this assembly provide speed control in RPM. See Appendix B.
3. Assembly 22 (Class 4, Instance 22, Attribute 3)
Bytes 2 and 3 of this assembly provide speed control in RPM. See Appendix B.
4. Assembly 23 (Class 4, Instance 23, Attribute 3)
Bytes 2 and 3 of this assembly provide speed control in RPM. See Appendix B.
5. Assembly 120 (Class 4, Instance 120, Attribute 3)
Bytes 2 and 3 of this assembly provide speed control in Hz. See Appendix B.
6. Assembly 122 (Class 4, Instance 122, Attribute 3)
Bytes 2 and 3 of this assembly provide speed control in Hz. See Appendix B.
7. Assembly 124 (Class 4, Instance 124, Attribute 3)
Bytes 2 and 3 of this assembly provide speed control in Hz. See Appendix B.
8. Assembly 126 (Class 4, Instance 126, Attribute 3)
Bytes 2 and 3 of this assembly provide speed control in Hz. See Appendix B.
9. AC Drive Class 42, Instance 1, Attribute 8
This attribute provides speed control in RPM. See Appendix A.
10. Yaskawa Command Class 100, Instance 1, Attribute 2
This attribute provides speed control in Hz. See Appendix A.
If the Drive speed is being controlled with Polled I/O messages, then Assembly 20, 21, 22, 23, 120, 122, 124 or
126 are the only methods available from the list above.
Methods 1, 2, 3, 4 and 8 conform to the DeviceNet AC Drive Device Profile. See Chapter 8 for more information.
Torque Reference Control
In the F7 and G7 Drive, Flux Vector Control mode (A1-02=3) allows the Drive to be in Torque Control. When the
reference source is controlled from the DeviceNet Option Board (b1-01=3), the torque reference to the Drive may
be set via DeviceNet. When controlling the torque of the Drive from the DeviceNet network, torque reference
can be accessed in various ways:
1. Assembly 22 (Class 4, Instance 22, Attribute 3)
Bytes 4 and 5 of this assembly provide torque control in N-m*(2
torque_scale
). See Appendix B.
2. Assembly 23 (Class 4, Instance 23, Attribute 3)
Bytes 4 and 5 of this assembly provide torque control in N-m*(2
torque_scale
). See Appendix B.
3. Assembly 121 (Class 4, Instance 121, Attribute 3)
Bytes 2 and 3 of this assembly provide torque control in % of rated. See Appendix B.
4. Assembly 122 (Class 4, Instance 122, Attribute 3)
Bytes 2 and 3 of this assembly provide torque control in % of rated. See Appendix B.
5. Assembly 125 (Class 4, Instance 125, Attribute 3)
Bytes 4 and 5 of this assembly provide torque control in % of rated. See Appendix B.
6. Assembly 126 (Class 4, Instance 126, Attribute 3)
Bytes 4 and 5 of this assembly provide torque control in % of rated. See Appendix B.
7. AC Drive Class 42, Instance 1, Attribute 12
This attribute provides torque control in N-m*(2
torque_scale
). See Appendix A.
8. Yaskawa Command Class 100, Instance 1, Attribute 3
This attribute provides torque control in % of rated. See Appendix A.