Functional safety - basic principle, Selecting the transmission type – HEIDENHAIN PWM 20 User Manual
Page 227
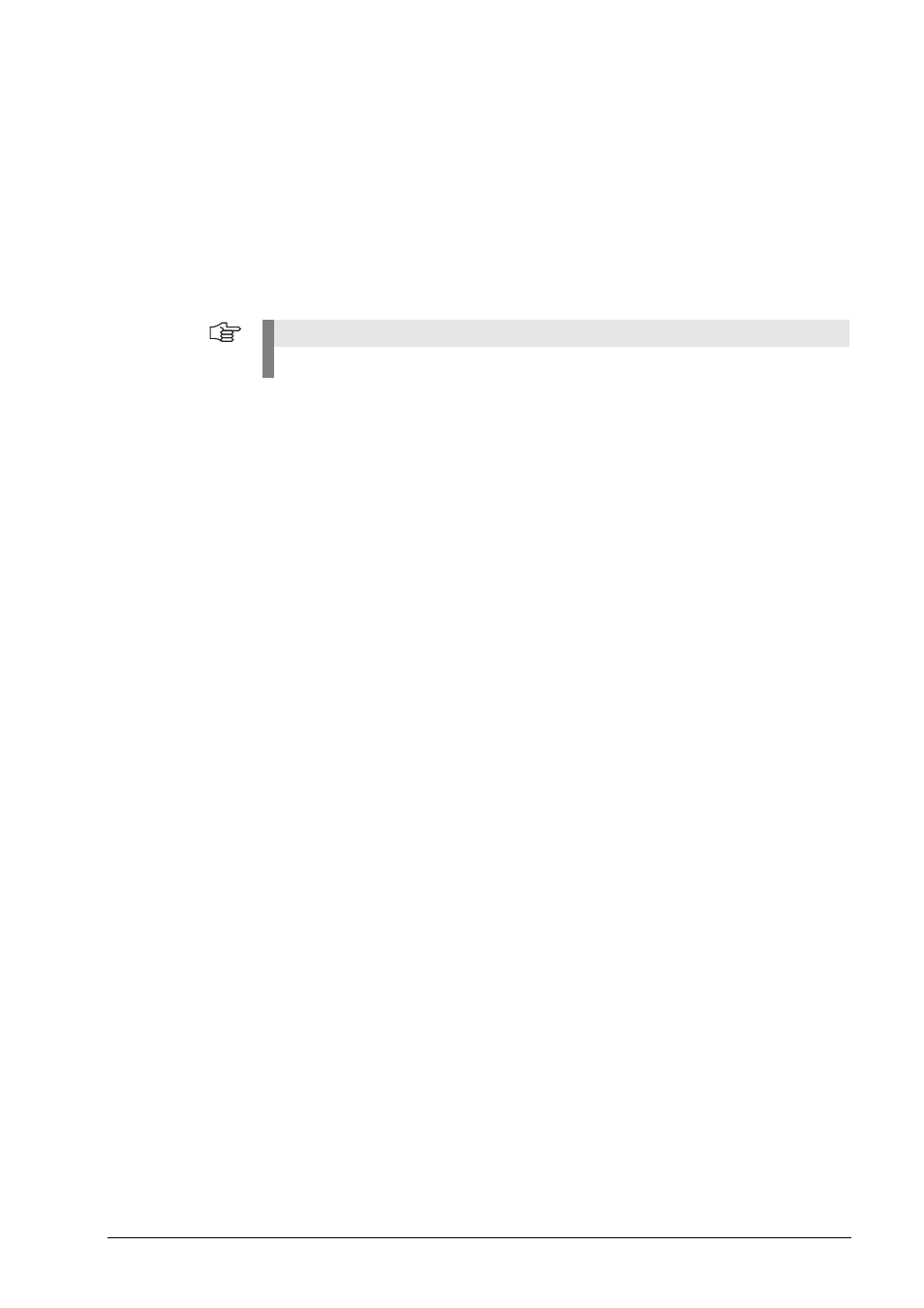
228
HEIDENHAIN ATS Software User's Manual
Reset functions serve to reset the encoder in case of malfunction. Reset is possible instead of
or during position value transmission.
Servicing diagnosis makes it possible to inspect the position value even at standstill. A test
command has the encoder send the required test values.
Functional Safety
– Basic principle
EnDat 2.2 strictly supports the use of encoders in safety-related applications.
The DIN EN ISO 13 849-1 (previously EN 954-1), EN 61508 and EN61800-5-2 standards serve
as the foundation for this. These standards describe the assessment of safety-oriented systems,
for example based on the failure probabilities of integrated components and subsystems. The
modular approach helps manufacturers of safety-related systems to implement their complete
systems, because they can begin with prequalified subsystems.
Selecting the
transmission type
Transmitted data are identified as either position values, position values with additional
information, or parameters. The type of information to be transmitted is selected by MODE
commands. MODE commands define the content of the transmitted information. Every MODE
command consists of three bits. To ensure reliable transmission, every bit is transmitted
redundantly (inverted or double). The EnDat 2.2 interface can also transfer parameter values in
the additional data together with the position value. This makes the current position values
constantly available for the control loop, even during a parameter request.
Control cycles for transfer of position values
The transmission cycle begins with the first falling clock edge The measured values are saved
and the position value is calculated. After two clock pulses (2T), to select the type of
transmission, the subsequent electronics transmit the MODE command “Encoder transmit
position value” (with/without additional information).
The subsequent electronics continue to transmit clock pulses and observe the data line to detect
the start bit. The start bit starts data transmission from the encoder to the subsequent
electronics. Time tcal is the smallest time duration after which the position value can be read by
the encoder. The subsequent error messages, error 1 and error 2 (only with EnDat 2.2
commands), are group signals for all monitored functions and serve as failure monitors.
Beginning with the LSB, the encoder then transmits the absolute position value as a complete
data word. Its length varies depending on which encoder is being used. The number of required
clock pulses for transmission of a position value is saved in the parameters of the encoder
manufacturer. The data transmission of the position value is completed with the Cyclic
Redundancy Check (CRC).
In EnDat 2.2, this is followed by additional information 1 and 2, each also concluded with a CRC.
With the end of the data word, the clock must be set to HIGH.
After 10 to 30 µs or 1.25 to 3.75 µs (with EnDat 2.2, the assignable recovery time tm) the data
line falls back to low. Then a new data transmission can begin by starting the clock.
Note
Encoders with functional safety do not permit feed-through mode with the PWM 20!