Frame orientation, Frame construction, Robot-to-frame considerations – Adept s650HS Quattro User Manual
Page 31: Mounting
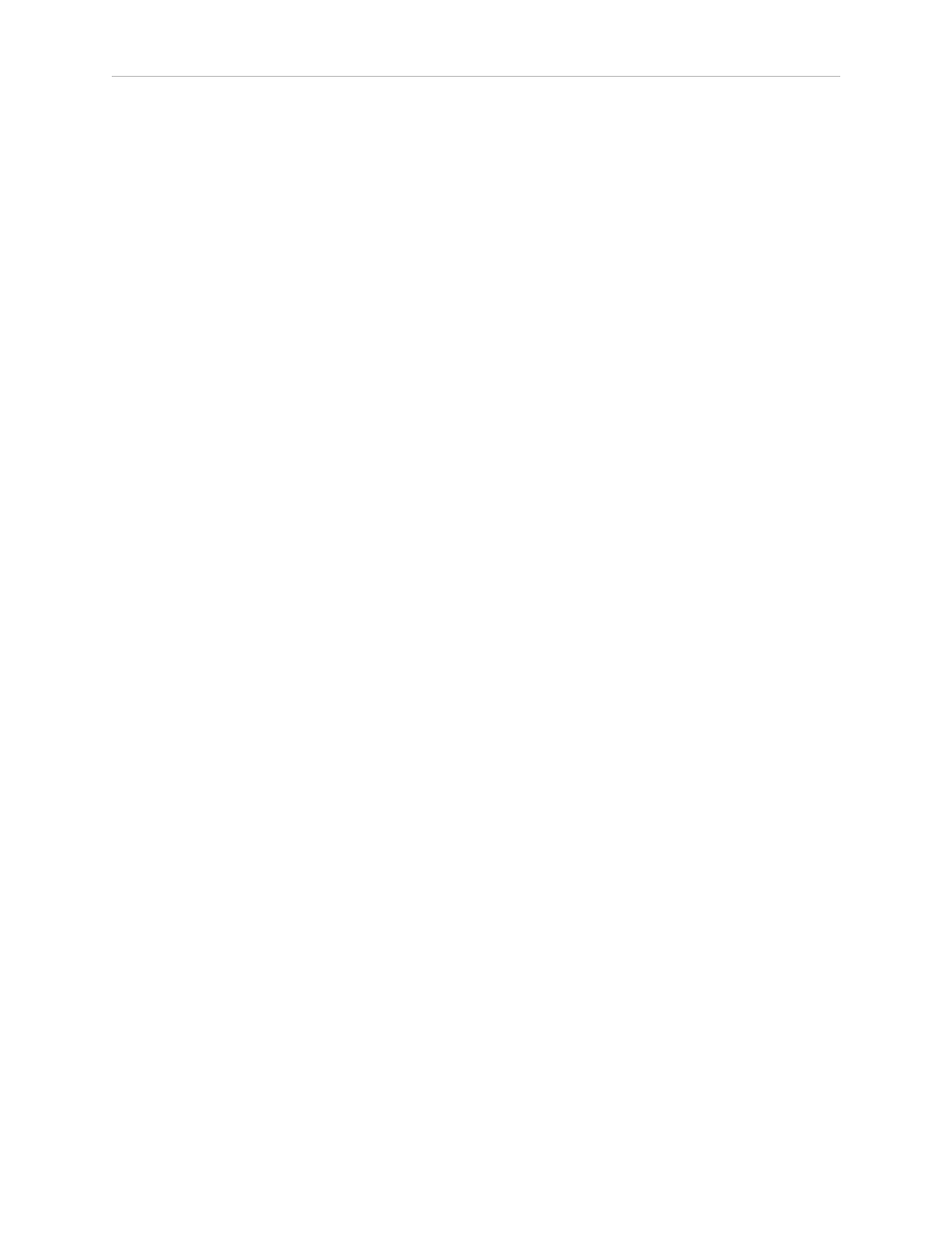
Chapter 2: Robot Installation - H
It is important to note that, even after the system reports the robot to be fully settled, the tool
flange will still be moving by any amount of motion that the suspended base of the robot may
be experiencing.
Frame Orientation
The sample robot frame design is stiffer in one direction than the other. This is to
accommodate conveyor belt applications where the robot is moving with much more
acceleration across a conveyor belt than along it. The conveyor should generally be aligned so
that the belt travel is along the robot World Y-axis, and the mid-height frame members cross
the belt at a 90° angle. The across-the-belt dimension of the frame should be minimized to get
the best performance of the robot in that direction. While this frame design assumes a 1.8 m
across-the-belt frame dimension, a 1.5 m dimension would offer increased stiffness and
possibly increased robot performance at high accelerations and payloads. The mid-height
horizontal members are important to the frame stiffness, and should be located as close to the
belt as possible.
For applications requiring high accelerations along the direction of belt travel, consideration
should be given to strengthening the frame in that direction.
Frame Construction
Typically, the frame is constructed of welded steel members. Hygiene-sensitive applications
may call for stainless steel fabrication, with care taken to seal up all possible voids and grind
smooth all weld joints. For other applications, it may be suitable to manufacture the frame of
carbon steel and paint the resulting assembly. The frame design presented here is based on a
stainless steel construction using 10 mm thick members. It may be reasonable to use a reduced
thickness for carbon steel assemblies. Some customers may choose to use tubular members, or
turn horizontal members at 45° angles to facilitate water runoff from the flat frame surfaces.
Robot-to-Frame Considerations
The Quattro has a moderately-complex mounting requirement due to the nature of the parallel-
arm kinematics and the need to minimize the robot size and mass. Arm Travel Volume (s650
shown) on page 118 shows the inner arm travel and how it may encroach on the robot
mounting points. As a starting point, for a frame that is 2 meters in each direction, (allowing
use of the full range of the Quattro s650 robots), you should attempt to attain a frame
frequency of 25 Hz.
For specialized applications, such as heavy payloads and/or aggressive moves, you may want
to attain a frame frequency of 40 Hz.
In general, a smaller frame will yield a higher frequency. If you aren’t going to use to entire
work envelope, you can increase the frequency simply by using a smaller frame.
A lower frequency frame, more aggressive robot moves, and heavier payloads will all
contribute to longer settling times.
Mounting
The robot mounts in four locations, as detailed in the drawings. The holes are tapped for an
M16 x 2.0 bolt. The Adept Quattro robot may be mounted from the top or bottom of the frame.
A crane or forklift should be used to position the robot. If lifted from above, the robot must be
lifted by user-supplied eyebolts and slings.
Adept Quattro User's Guide, Rev F
Page 31 of 196