Frame mounting tabs, Robot-to-frame considerations, Mounting – Adept s650HS Quattro User Manual
Page 47
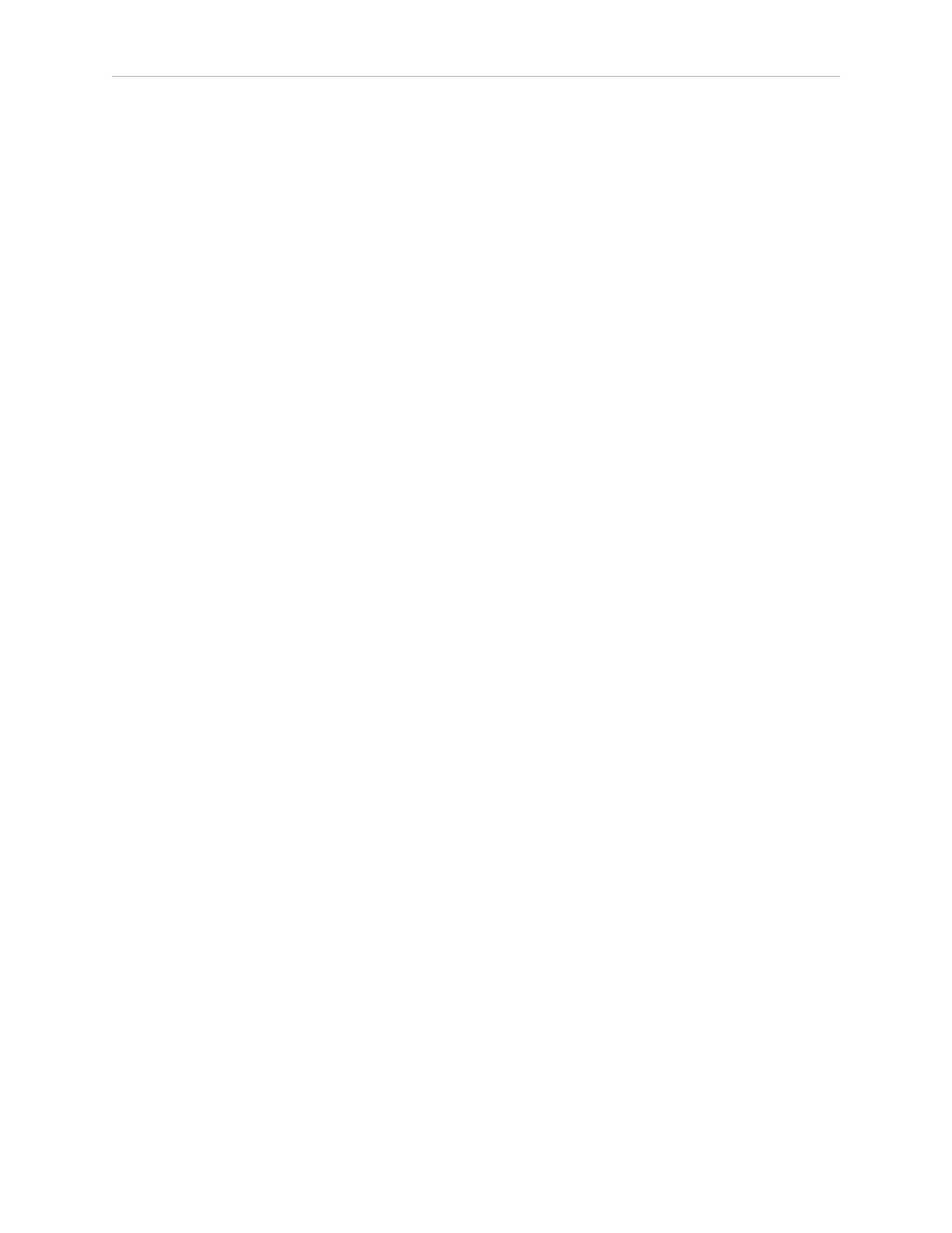
Chapter 3: Robot Installation - HS
Any robot’s ability to settle to a fixed point in space is governed by the forces, masses, and
accelerations of the robot. Since “every action has an equal and opposite reaction”, these forces
are transmitted to the robot frame and cause the frame and base of the robot to move and
possibly vibrate in space. As the robot system works to position the tool flange relative to the
base of the robot, any frame or base motion will be “unobservable” to the robot system, and
will be transmitted to the tool flange. This transmitted base motion will result in inertial
movement of the tool flange mass, and will cause disturbance forces to be introduced into the
robot control system. These disturbance forces cause “work” to be done by the robot servo
control system which may result in longer settling times for robot operations.
It is important to note that, even after the system reports the robot to be fully settled, the tool
flange will still be moving by any amount of motion that the suspended base of the robot may
be experiencing.
Frame Mounting Tabs
To achieve the correct compression of the sealing gaskets, the mounting tabs on the frame
must be 12.7 mm, +1.3, -0.7 mm thick (0.5 in., +0.05, -0.028 in.).
Because the junction of the robot base mounting pad and the frame mounting pad is sealed
with a gasket, the frame mounting pads must be at least as big as the robot base mounting
pads. If the frame pad does not cover the entire robot pad, the gasket will not seal properly.
The design of the Quattro HS robot mounting bolts and seals requires fairly tight tolerances for
the robot mounting holes in the frame. These should be 17.25 ± 0.75 mm (0.68 ± 0.03 in.) in
diameter.
Robot-to-Frame Considerations
The Quattro robot has a moderately-complex mounting requirement due to the nature of the
parallel-arm kinematics and the need to minimize the robot size and mass. Arm Travel
Volume (s650 shown) on page 118 shows the inner arm travel and how it may encroach on
the robot mounting points. As a starting point, for a frame that is 2 meters in each direction,
(allowing use of the full range of the Quattro s650 robots), you should attempt to attain a frame
frequency of 25 Hz.
For specialized applications, such as heavy payloads and/or aggressive moves, you may want
to attain a frame frequency of 40 Hz.
In general, a smaller frame will yield a higher frequency. If you aren’t going to use to entire
work envelope, you can increase the frequency simply by using a smaller frame.
A lower frequency frame, more aggressive robot moves, and heavier payloads will all
contribute to longer settling times.
Mounting
Mounting Hole Dimensions, Quattro HS Robots on page 113 shows the mounting hole pattern
for the Quattro HS robot. Note the hole location and mounting pad tolerances for position and
flatness.
Deviation from this flatness specification will, over time, cause a possible loss of robot
calibration.
Adept Quattro User's Guide, Rev F
Page 47 of 196