Normal data transfer – ProSoft Technology MVI56-103M User Manual
Page 102
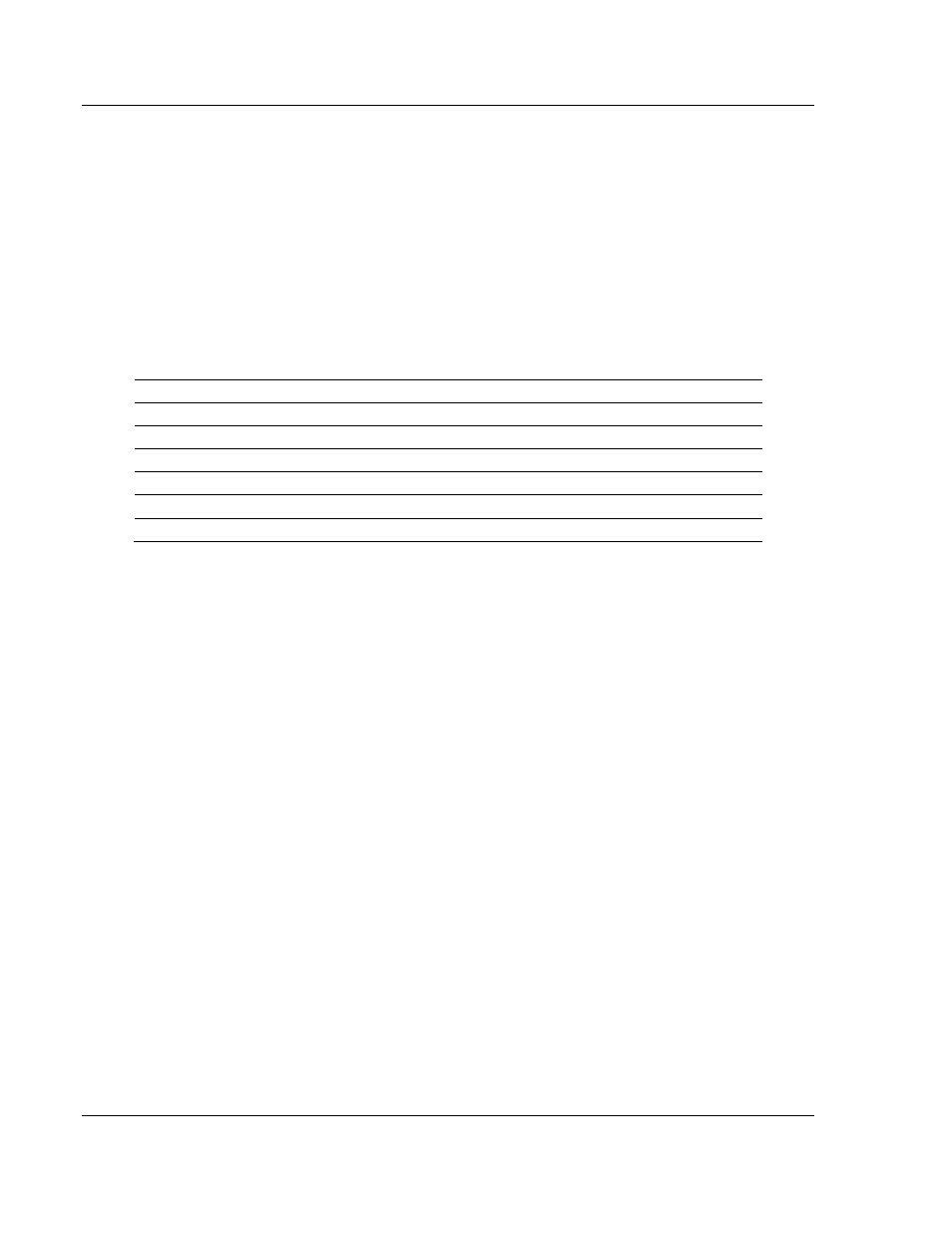
Reference
MVI56-103M ♦ ControlLogix Platform
User Manual
IEC 60870-5-103 Master Communication Module
Page 102 of 152
ProSoft Technology, Inc.
February 22, 2013
5.3
Normal Data Transfer
Normal data transfer includes the transferring of data received by or to be
transmitted to the Master drivers and the status data. These data are transferred
through read (input image) and write (output image) blocks.
Refer to Module Configuration for a description of the data objects used with the
blocks and the ladder logic required. The following topics discuss the structure
and function of each block.
5.3.1 Read Block
These blocks of data transfer information from the module to the ControlLogix
processor. The following table describes the structure of the input image.
Offset
Description
Length
0
Reserved
1
1
Write Block ID
1
2 to 201
Read Data
200
202 to 247
Error/Status Data
46
248
Spare
1
249
Read Block ID
1
The Block Identification Code (word 249) is used to signal to the ControlLogix
processor that a new block is ready for processing and informs the processor of
the contents of the block. If the value of the code is set to1, the block contains
the first 200 words of data contained in the database of the module.
Additionally, the status data contained in the block should be copied to the status
data area in the module. This information can be used to determine the "health"
and activity of the module. For a detailed listing of the Status area and its
contents, refer to Status Data Area (page 114).
The block also contains the Write Block Identification (ID) code the module
expects to receive from the processor (word 1 in the block) in the next output
image. Under normal data transfer conditions, the ladder logic should use this
code to build the output image, unless a special output block has been triggered
to be sent instead.