Introduction, Operating precautions, Dielectric test – Basler Electric BE1-25A User Manual
Page 57: Application, General information, Section 5, Testing -1, Introduction -1, Operating precautions -1, Dielectric test -1
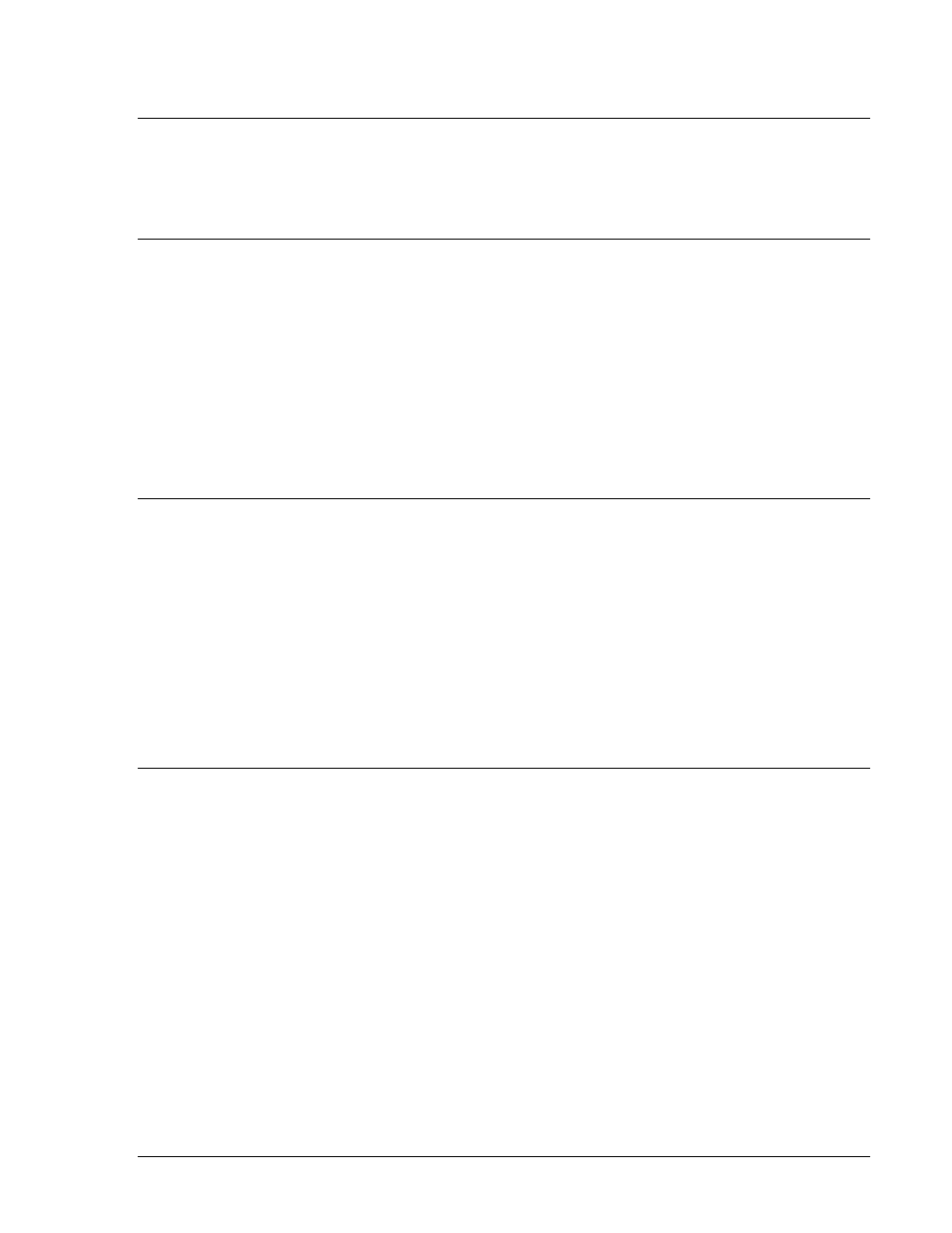
SECTION 5
• TESTING
INTRODUCTION
BE1-25A Auto-Synchronizers are calibrated and tested for correct operation at the factory and all
calibration pots are sealed. Immediately upon receipt of the relay, or after extended service, it is
recommended that the VERIFICATION TESTS in this section be performed. These comprehensive tests
verify all operating parameters.
OPERATING PRECAUTIONS
Before operation, note the following precautions.
• Always be sure that external operating (monitored) conditions are stable before removing a BE1-
25A unit from service.
• The BE1-25A is a solid-state device and has been type tested in accordance with the
requirements defined below under Dielectric Test. If a wiring insulation test is required on the
switchgear or panel assembly of which this unit is a part, see Dielectric Test below.
• Be sure that the BE1-25A case is hard wired to earth ground using the ground terminal (A1) on
the rear of the unit.
• When the unit is in service, the controls should be protected by the plastic cover supplied. This
limits access to the control settings.
DIELECTRIC TEST
In accordance with IEC 255-5 and ANSI/IEEE C37.90-1978, one-minute dielectric (high potential) tests up
to 1500 Vac (45-65 hertz) may be performed. Note that:
• Decoupling capacitors are employed from all terminals to ground. Accordingly, a leakage current
of approximately 20 milliamperes is to be expected when high potting at 1500 Vac, 60 hertz.
• Varistors are connected across all terminal-pairs of terminal strip TB1, and across terminals 21/22
of TB2. Do NOT high pot from terminal to terminal across these varistors. Normal high pot
procedures (high potting from terminal to frame) are not affected by these varistors.
• A one megohm resistor is used in the contact sensing input circuit between the minus supply and
the chassis. High potential testing on these contact sensing inputs (TB1, terminals 3, 4, 5, 6, 9,
10, 11, 12, 13, 14, 15, and 16), (TB2, terminals 21 and 22) may damage the internal resistor. Use
a high resistance tester (megger) or alternate means to test these contacts.
APPLICATION
General Information
Although operation of BE1-25A Auto-Synchronizers is straightforward, the following suggestions are
offered.
• When using the LOAD switch, there is a built-in delay before the display responds to the
command. This delay is for the purpose of security — so that a deliberate action is required to
effect a change, not an accidental bump. (If the switch is released before display
acknowledgment, the original setting is retained.)
• Dashes in the display indicate an open input or out-of-range condition.
• When power is first applied to the unit, the display defaults to Function P, at which position the
display functions as a digital synchroscope. This default also occurs whenever the unit is RESET.
• In an ideal system, a smoother closing results when the generator speed and voltage are exactly
in synchronism with the system. Depending on the system, this usually is not possible. Closing
from the high side with GF > BF usually results in less stress on system components. Contact
sensing inputs can be set so that the synchronizer only allows closing when GF > BF and/or GV >
BV.
9146600990 Rev S
BE1-25A Testing
5-1