Voltage acceptance module a2 verification test, Frequency matching module f5 verification test, Voltage acceptance module a2 verification test -10 – Basler Electric BE1-25A User Manual
Page 66: Frequency matching module f5 verification test -10
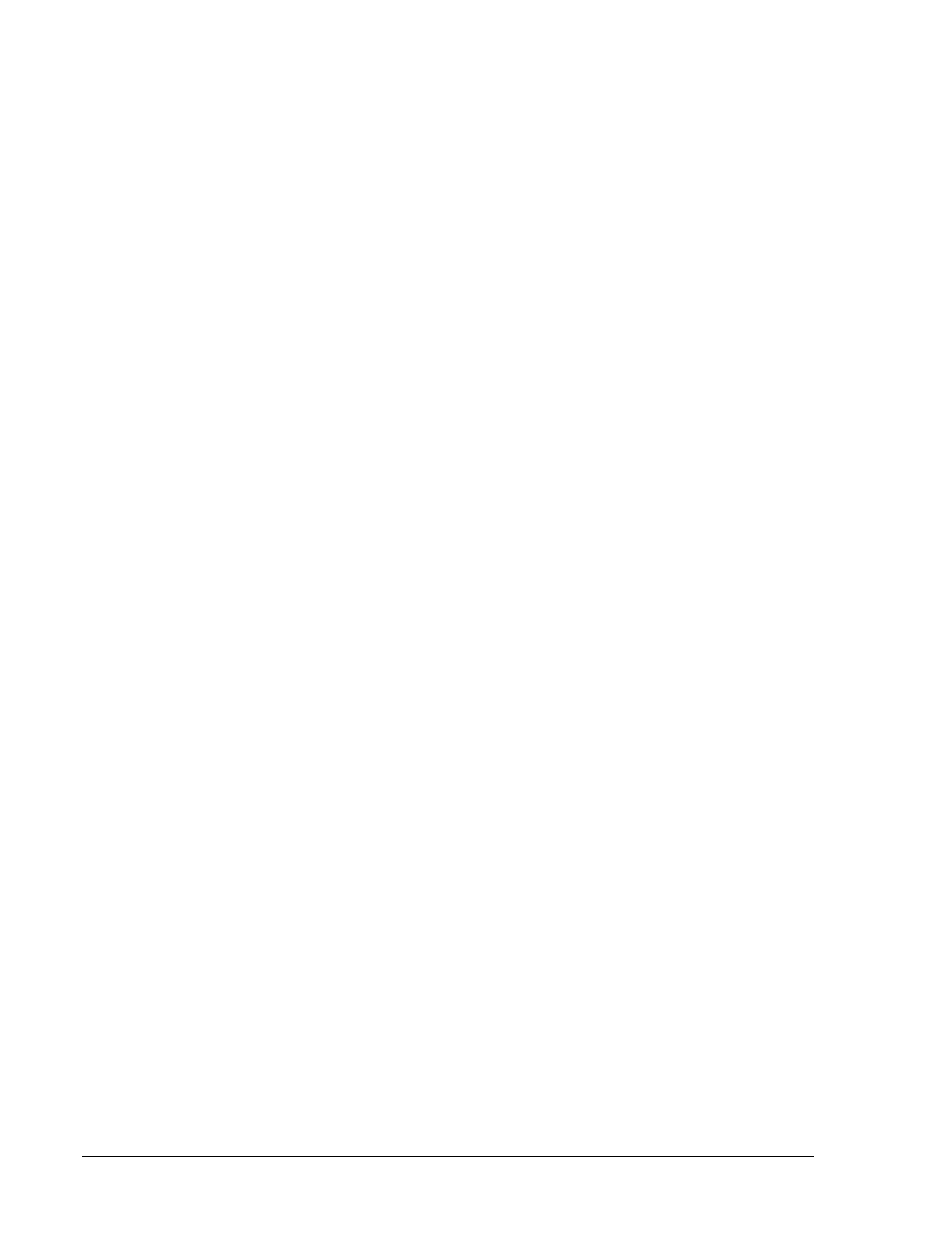
Step 5. Test the GV>BV function by setting the generator voltage to a value 2.0% lower than that of the
bus. Set the VOLTAGE DIFFERENCE control to 5%. Shorting the GV>BV jacks on the test
module should inhibit SYNC LED operation. Removing the short should restore the output.
Voltage Acceptance Module A2 Verification Test
Step 1. Provide the test setup illustrated in Figure 5-1, and move the test module into the offset (i.e.,
test) position.
Step 2. Set the bus voltage to 120 Vac at 60.0 hertz, and the generator voltage to 120 Vac at 60.10
hertz. Set the UPPER LIMIT control to 150, and the LOWER LIMIT control to 80. Set the
VOLTAGE DIFFERENCE control to 10.
Step 3. Increase the generator voltage until the HIGH LED turns ON (approximately 130 Vac).
Step 4. Decrease the generator voltage towards 120 Vac and observe that the HIGH LED turns OFF.
Step 5. Set the bus voltage to 120 Vac at 60.0 hertz, and the generator voltage to 120 Vac at 60.10
hertz. Set the VOLTAGE DIFFERENCE control to 1.
Step 6. Increase the generator voltage until the HIGH LED turns ON (approximately 121 Vac).
Step 7. Decrease the generator voltage towards 120 Vac and observe that the HIGH LED turns OFF.
Step 8. Set the simulated bus voltage to the desired upper limit. Adjust the UPPER LIMIT control until
the HIGH LED just turns OFF. The high limit is now set.
Step 9. Set the simulated bus voltage to the desired lower limit. Adjust the LOWER LIMIT control until
the LOW LED just turns OFF. The low limit is now set.
Step 10. Verify that the SYNC LED will not operate whenever the bus voltage is above or below the
UPPER LIMIT or LOWER LIMIT settings. A LIMIT HIGH LED or a LIMIT LOW LED will confirm
that the bus voltage is out of range.
Frequency Matching Module F5 Verification Test
Step 1. Provide the test setup illustrated in Figure 5-2, and move the test module into the offset (i.e.,
test) position.
Step 2. Establish a slip rate of 1 hertz using the following parameters for generator 1.
On MCU display, set the following parameters and load them into MCU memory.
• Generator select (register 0) = 1.
• Breaker time (register 1) = 0.200 second.
• Correction pulse width (register 2) = 5.0 seconds.
• Correction pulse interval (register 3) = 5.0 seconds.
• Maximum slip (register 4) = 0.250 hertz.
• Generator undervoltage (register 5) = 90 volts.
• Lockout ON/OFF (register 6) = Lon.
On the test setup, set the following parameters.
• Generator voltage = 120 Vac at 59 hertz.
• Bus voltage = 120 Vac at 60 hertz.
• GF > BF switch to OPEN.
• 52b contacts CLOSED.
• Activate RESET switch.
Step 3. Measure the correction pulse width by timing the ON time of the F5 module RAISE LED (time
should be approximately 5.0 seconds). Measure the correction pulse interval by timing the OFF
time of the F5 module RAISE LED (time should be approximately 5.0 seconds). Total time for
ON and OFF is approximately 10.0 seconds. Observe that the SLIP INH LED is ON.
Step 4. Set the generator voltage = 120 Vac at 59.5 hertz.
Step 5. Measure the correction pulse width by timing the ON time of the F5 module RAISE LED (time
should be approximately 2.5 seconds). Measure the correction pulse interval by timing the OFF
5-10
BE1-25A Testing
9146600990 Rev S