Undervoltage (uv) inhibit verification test, Slip frequency verification test, Sync signal verification test – Basler Electric BE1-25A User Manual
Page 63: Undervoltage (uv) inhibit verification test -7, Slip frequency verification test -7, Sync signal verification test -7
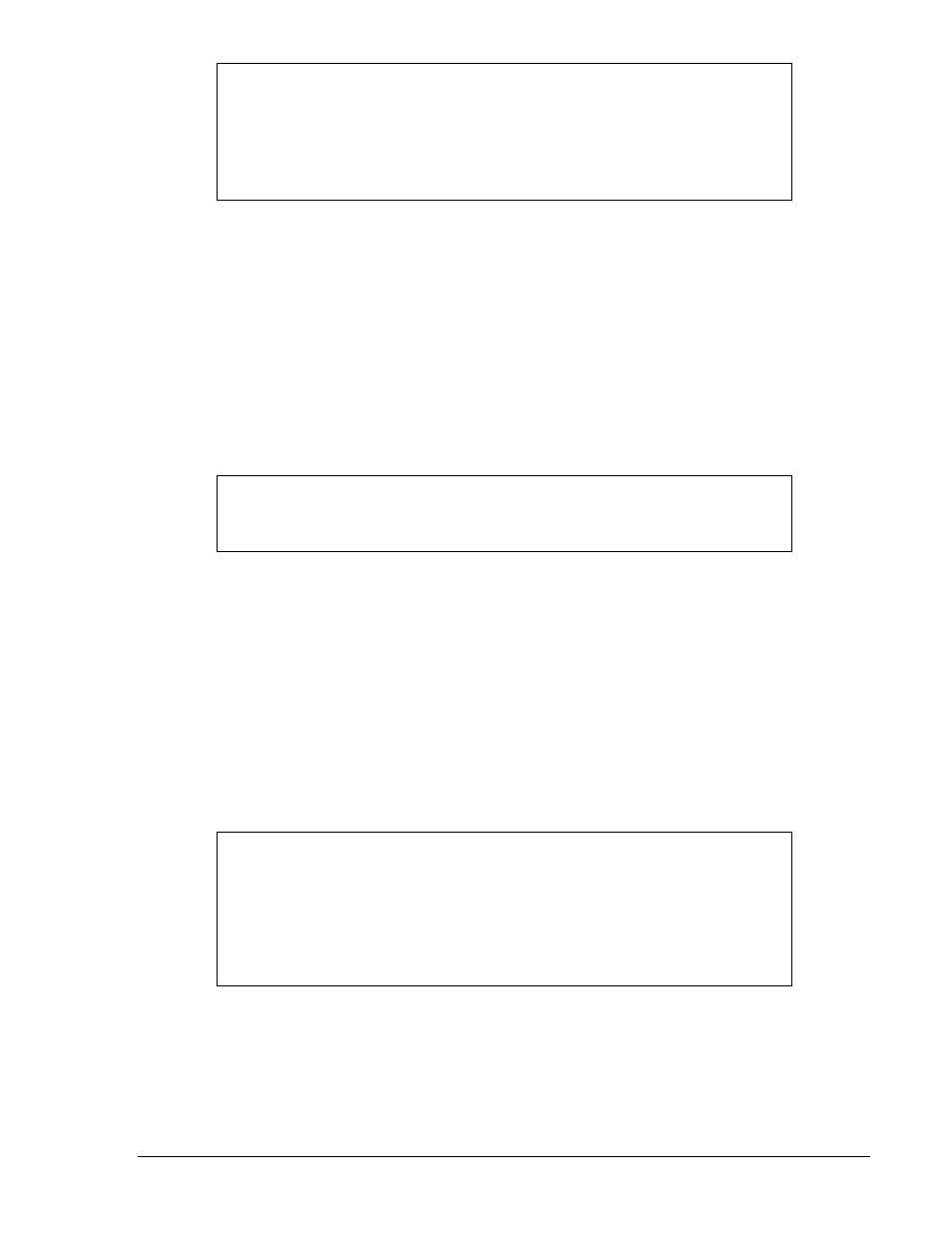
Undervoltage (UV) Inhibit Verification Test
Step 1. For a bench test, connect the unit as in Figure 5-1. Otherwise connect the unit as described
previously in steps 1 through 4, and illustrated in Figure 5-1. Leave GF>BF, GV>BV, and dead
bus open (i.e., OFF) at this time. Set the simulated bus and generator voltages at 120 Vac, 60
hertz.
Step 2. Set the GEN UV register to 40 Vac. Reduce the simulated generator voltage until the GEN UV
LED turns ON. This should occur as the simulated generator voltage goes below 40
±1.5 Vac.
(Beginning here, the word simulated shall be understood without repeating it.)
Step 3. Return the GEN UV register to 110 Vac: the GEN UV LED should remain ON. Increase the
generator input voltage until the GEN UV LED turns OFF. This should occur as the input voltage
rises above 110
±1.5 Vac.
Slip Frequency Verification Test
Step 4. Set the GEN UV register to 40 Vac. Set the MAX SLIP register for 0.500 hertz.
Step 5. Adjust the bus input and the generator input to 120 Vac at 60.00 hertz.
Step 6. Slowly adjust the generator input frequency lower. At 59.49
±0.01 hertz, the SLIP HIGH LED
should turn ON. Slowly move the generator frequency above and below the threshold and
observe that the LED acknowledges the slip frequency status within the stated tolerance.
Sync Signal Verification Test
Step 7. With the bus input at 120 Vac, 60.00 hertz, adjust the generator input to 120 Vac at 59.90 hertz.
Set MAX SLIP (the #4 register) for 0.250 hertz. Rotate the GENERATOR SELECT control knob
to the generator position of choice. Set the register of the active breaker to 0.40 seconds.
Step 8. Using an external synchroscope, check that the SYNC LED turns ON at 14
±3°, and OFF at 0°.
The breaker closure output (as monitored by a lamp (Figure 5-1), or an oscilloscope (Figure
5-1)) should follow the SYNC LED.
Step 9. Install a jumper at the GF>BF jacks of the test module. The SYNC LED should immediately stop
flashing. Remove jumper to bring back the flashing SYNC LED. (The flashing is caused by the
slip rate. Note that (with this jumper applied) the generator frequency must be greater than that
of the bus for a sync output to be initiated.)
NOTE
Verification test procedures for Auto-Synchronizers prior to serial number 300,
and for discontinued Options B3, B5, F1, F2, F3, F4, and V4, are given in Section
7.
All option modules should NOT be installed when performing the basic
verification tests because they affect the basic unit effective parameters.
NOTE
If there is a slip rate, the SYNC LED will begin flashing (instead of extinguishing)
as synchronization is detected.
NOTE
Always load in all new breaker timer settings, and always verify the active
breaker by momentarily selecting item d from the MCU readings menu. (Breaker
settings, unlike other settings, must be loaded before they can take effect.)
When a sync output closure is initiated, the sync output contact will be held
closed for the duration of the Breaker Operating Time setting (or 250 ms
minimum).
9146600990 Rev S
BE1-25A Testing
5-7