Maximizing auto-synchronizer performance, Application example, Example parameters – Basler Electric BE1-25A User Manual
Page 58: Recommended procedure, Maximizing auto-synchronizer performance -2, Application example -2, Example parameters -2, Recommended procedure -2
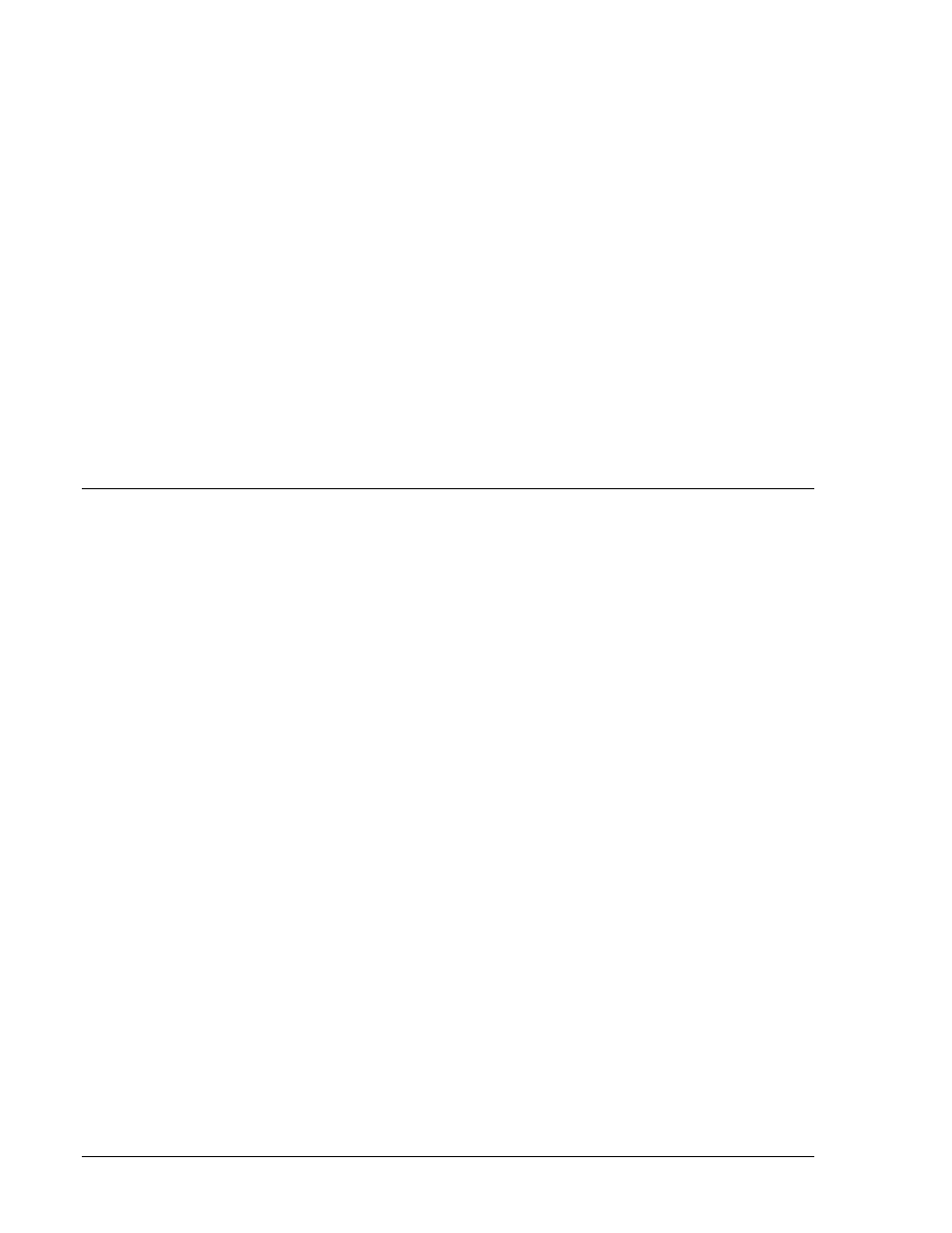
• Setting MAX SLIP too low can result in excessive hunting by the governor. A low inertia system
driven by an internal combustion prime mover is especially prone to this, since the power strokes
can (prior to breaker closure) modulate the fundamental frequency of the generator output. If the
resulting sidebands (or jitter) exceed the MAX SLIP frequency, overshoot and prolonged delay in
reclosing will likely occur.
• Because installations may have different characteristics, there is no standard value for the
generator speed correction pulse width and interval settings. Refer to the following paragraph
Maximizing Auto-Synchronizer Performance for a recommended procedure to achieve values for
the generator speed correction pulse width and interval settings.
• Whenever the LOAD switch is raised, the BE1-25A becomes inactive (non-functional) for 1.0
second.
Maximizing Auto-Synchronizer Performance
Disconnect the breaker from the Auto-Synchronizer output. Select a pulse width and interval setting
based on governor sensitivity. Record the synchronizing time (that time from when the Auto-Synchronizer
initiates correction pulses to when the Auto-Synchronizer issues the breaker close signal).
If excessive overshooting occurs, reduce the correction pulse width and increase the correction pulse
interval. If the generator speed increases too slowly, then increase the correction pulse width and reduce
the correction pulse interval.
Maximum performance is achieved if synchronization occurs within one to two minutes providing that the
Auto-Synchronizer takes control of the generator within a two hertz slip frequency window.
APPLICATION EXAMPLE
Example Parameters
• A generator breaker whose characteristic closing time is 385 milliseconds.
• A maximum allowable slip rate of 0.1 hertz. (This slip rate suggests that our hypothetical
generator is of greater than average size.)
• A generator undervoltage of 65 Vac. (I.e., at this voltage or below, no effort shall be made by the
Auto-Synchronizer to control the generator voltage.)
• For this example, the generator is designated West. This generator breaker closing time is to be
stored as generator breaker 2 in the Auto-Synchronizer memory.
Recommended Procedure
Step 1. Bring the memory register for the test generator into view by depressing the FUNCTION switch
once (MCU display should show 0 in the left-most digit and—in the right-most digit), and then
depress the increment switch twice to select generator breaker 2 (MCU display shows 2 in the
right-most digit).
Step 2. Depress the FUNCTION switch once and observe that the display left-most digit shows 1.
Change the display to read 1.385, the .385 represents the new breaker-closing time in seconds.
This is done by holding and/or stepping the INCREMENT/DECREMENT switch until the desired
number is displayed. (Note the two-speed response as the switch is held depressed. This
feature greatly speeds up the selection process.) Raise the LOAD switch, and hold it raised for
at least two seconds. The display will blank out and then, after about one second, will read
1.385. This is to acknowledge that the characteristic closing time for the breaker that controls
the West generator has been recorded.
Step 3. Depress the FUNCTION switch once and observe that the display left-most digit shows 2. Use
the INCREMENT/DECREMENT switch to select a value/setting for the correction pulse width.
Raise the LOAD switch, and hold it raised for about two seconds. The display will blank out and
then return, indicating that the new correction pulse width has been stored in MCU memory.
Step 4. Depress the FUNCTION switch once and observe that the display left-most digit shows 3. Use
the INCREMENT/DECREMENT switch to select a value/setting for the correction pulse interval.
Raise the LOAD switch, and hold it raised for about two seconds. The display will blank out and
then return, indicating that the new correction pulse interval has been stored in MCU memory.
5-2
BE1-25A Testing
9146600990 Rev S