Verification tests, General, Verification tests -6 – Basler Electric BE1-25A User Manual
Page 62: General -6
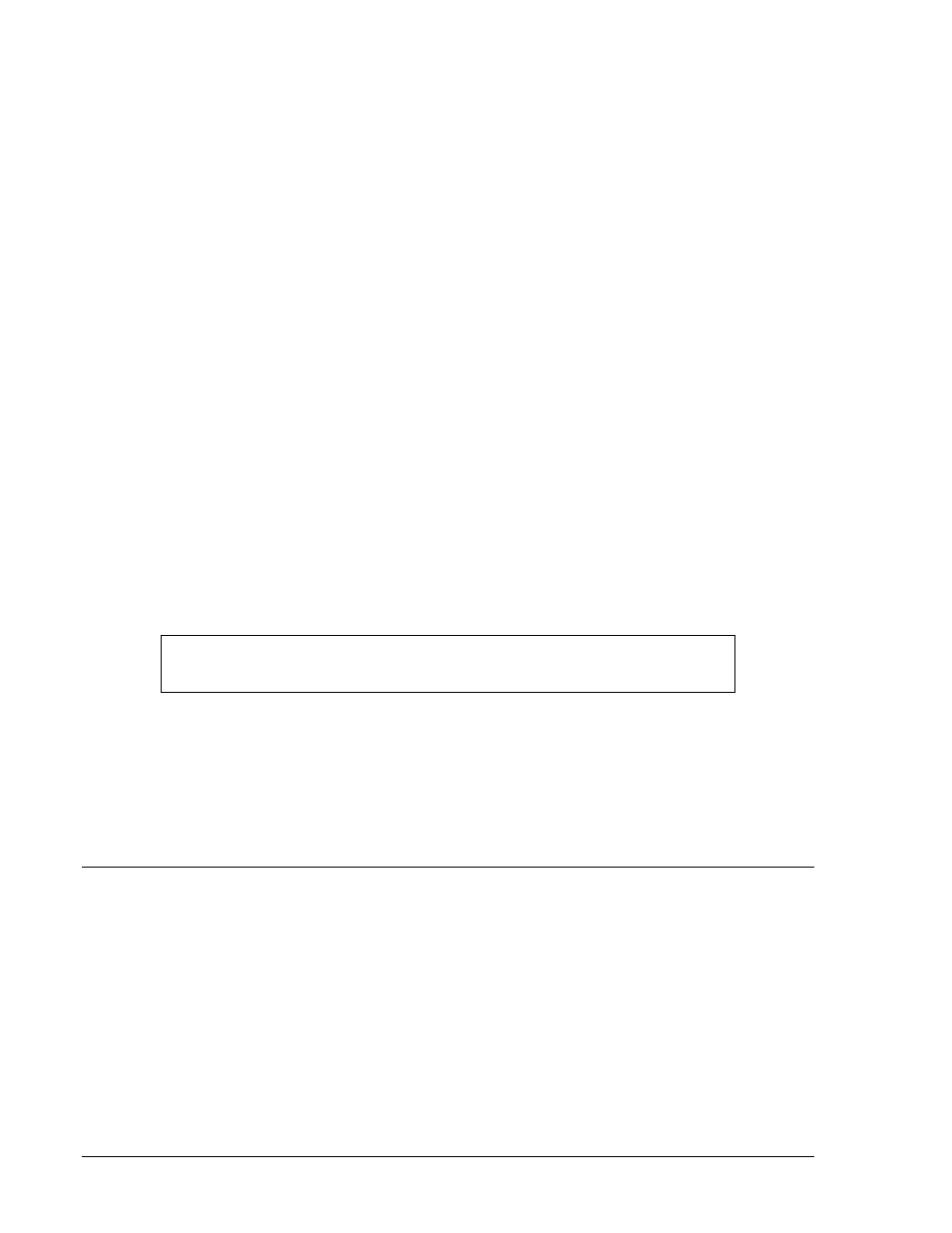
Step 4. With the sensing connections to the BE1-25A (via the rear case terminals) now disconnected,
all inputs for testing must be supplied by the jacks of the test module. At this time the jacks have
the following functions (functions are illustrated in Figure 5-2).
• BUS - Apply simulated bus voltage here.
• GEN - Apply simulated generator voltage here.
• POWER - These jacks are used to supply operating power. (Reference step 4.)
• 52b - Plug in a normally closed momentary pushbutton switch into these jacks to
simulate a 52b signal from the auxiliary contact of the breaker.
• GF>BF - Short these jacks together to simulate the closing of the GF>BF contact
sensing input terminals 13 & 14 of TB1 (reference Figure 5-2). When shorted, the
BE1-25A will not issue a breaker closure signal unless the generator frequency is
greater than the bus frequency.
• GV>BV - (Only used when an A option is installed.) Short these jacks together to
simulate the closing of the GV>BV contact sensing input terminals 11 & 12 of B1
(reference Figure 5-2). When shorted, the BE1-25A will not issue a breaker closure
signal unless the generator voltage is greater than the bus voltage.
• DEAD BUS - (Only used when a D option is installed.) Short these jacks together to
simulate the closing of the dead bus contact input terminals 9 & 10 of TB1 (reference
Figure 5-2). When shorted—AND if the dead bus option is incorporated—the BE1-
25A will issue a breaker-closure signal when the bus voltage drops below the set
threshold that defines a dead bus.
Step 5. Monitor the outputs as follows:
With test module in the test position—Operation of the Breaker Closure (i.e., SYNC) relay
may be monitored at the SIG & COM jacks of the MCU sync module, using an oscilloscope, as
illustrated in Figure 5-2. Each time the SYNC LED turns ON, the SIG voltage should be the
same as the COM jack voltage. At all other times there should be 12 Vdc between these jacks
(with SIG +). (Note that this monitoring procedure only confirms that an operating voltage is
being extended to the output relay. It does not confirm a contact closure by this relay.)
For bench testing (with test module in normal operating position)—If any of the plug-in
(option) relays are present, the pull-in of the relay armature(s) may be observed by opening the
hinged door at the rear of the unit.
Sync output—For many test purposes, the most convenient monitor of the sync output is the
SYNC LED. (Lit when sync relay is closed.) However, the bench test setup of Figure 5-1 has the
advantage of verifying the sync output plug-in relay is working properly.
VERIFICATION TESTS
General
Five test procedures cover the three basic modules (MCU sync module, test module, and power supply).
Testing of the optional modules is covered in individual verification tests. The five test procedures are:
• Undervoltage (UV) Inhibit Verification Test
• Slip Frequency Verification Test
• Sync Signal Verification Test
• Lockout and Reset Verification Test
• Advance Angle Verification Test
NOTE
When the test module is in test position, all output relays are de-energized.
5-6
BE1-25A Testing
9146600990 Rev S