17 additional information, 1 esc clock source, 2 power-on sequence – BECKHOFF EtherCAT Technology Section I User Manual
Page 114: Additional information, Esc clock source, Power-on sequence, Table 59: esc power-on sequence
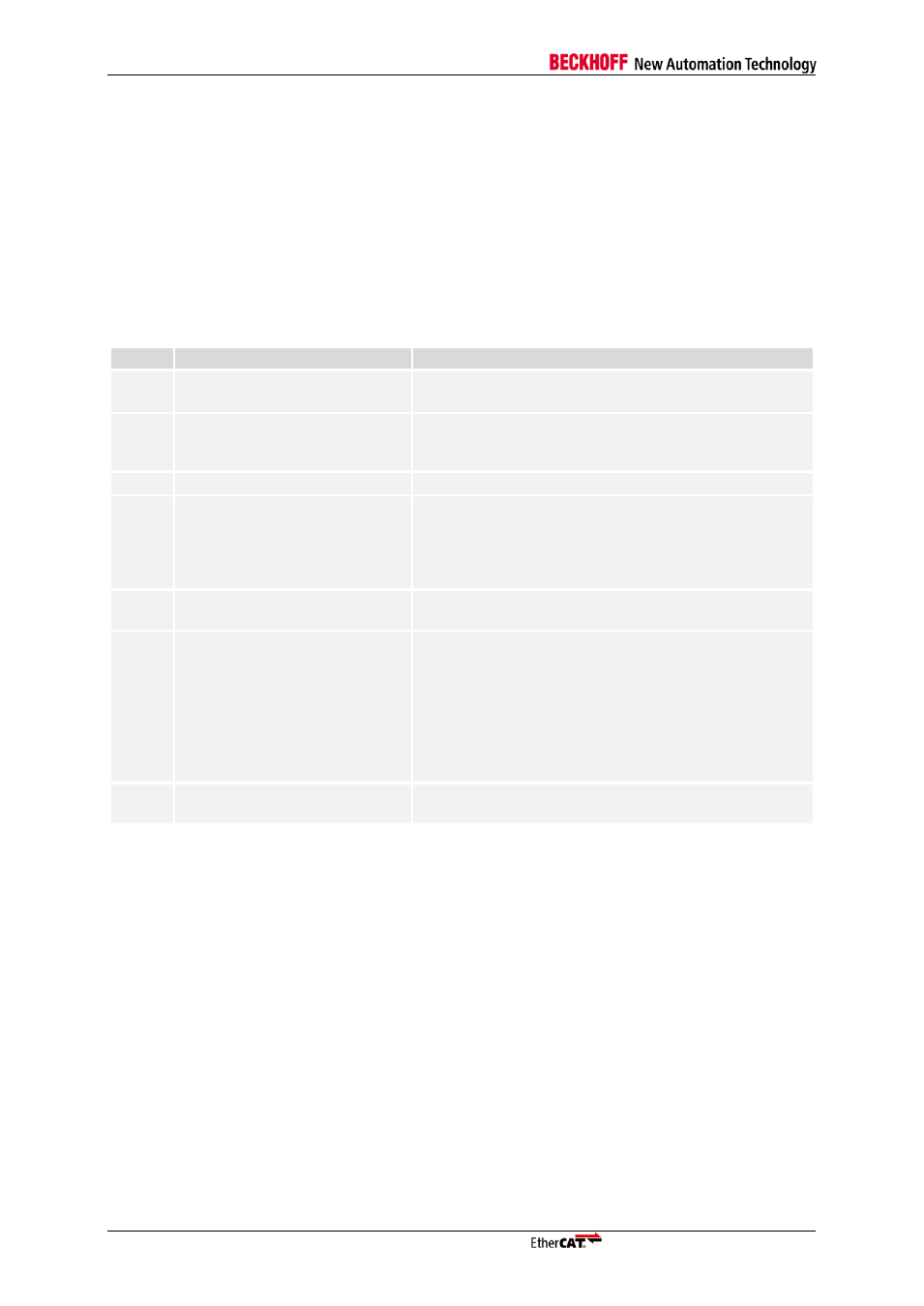
Additional Information
I-94
Slave Controller
– Technology
17 Additional Information
17.1 ESC Clock Source
The initial accuracy of the ESC clock sources has to be 25 ppm or better. This enables FIFO size
reduction, i.e., forwarding delay reduction, and supports fast DC locking. Existing designs do not need
to be changed.
17.2 Power-on Sequence
The power-on sequence of ESCs looks like this:
Table 59: ESC Power-On Sequence
No.
Step
Result
1
Power-on
Voltages reach proper levels
ASICs only: Power-on values are sampled
2
(FPGA
only)
Loading FPGA configuration
FPGA loads its hardware configuration
3
PLL locks
Clocks are generated properly
4
Release RESET
ESC operation begins. Process memory is not
accessible until the SII EEPROM is loaded, as well as
any function depending on ESC Configuration data. IP
Core: PDI is operational; others: PDI is not operational
until EEPROM is loaded.
5*
Links are established
EtherCAT communication begins, master can access
ESC registers
6*
Loading ESC EEPROM
Only upon successful EEPROM loading:
ESC Configuration registers initialized
PDI is activated (not IP Core: active after RESET)
PDI operation begins
Register bit 0x0110[0] turns to 1
Process Data RAM becomes accessible
Some PDIs: EEPROM_Loaded signal is driven high
ESC is in Init state
7
Example: Master proceeds to
Operational state
ESC proceeds to Operational state
* Steps 5 and 6 are executed in parallel.
NOTE: The PDI signals are not driven until the ESC EEPROM is loaded successfully, especially the
EEPROM_Loaded signal is not driven and needs a pull-down resistor if it is used.