Yaskawa SmartTrac AC1 User Manual
Page 78
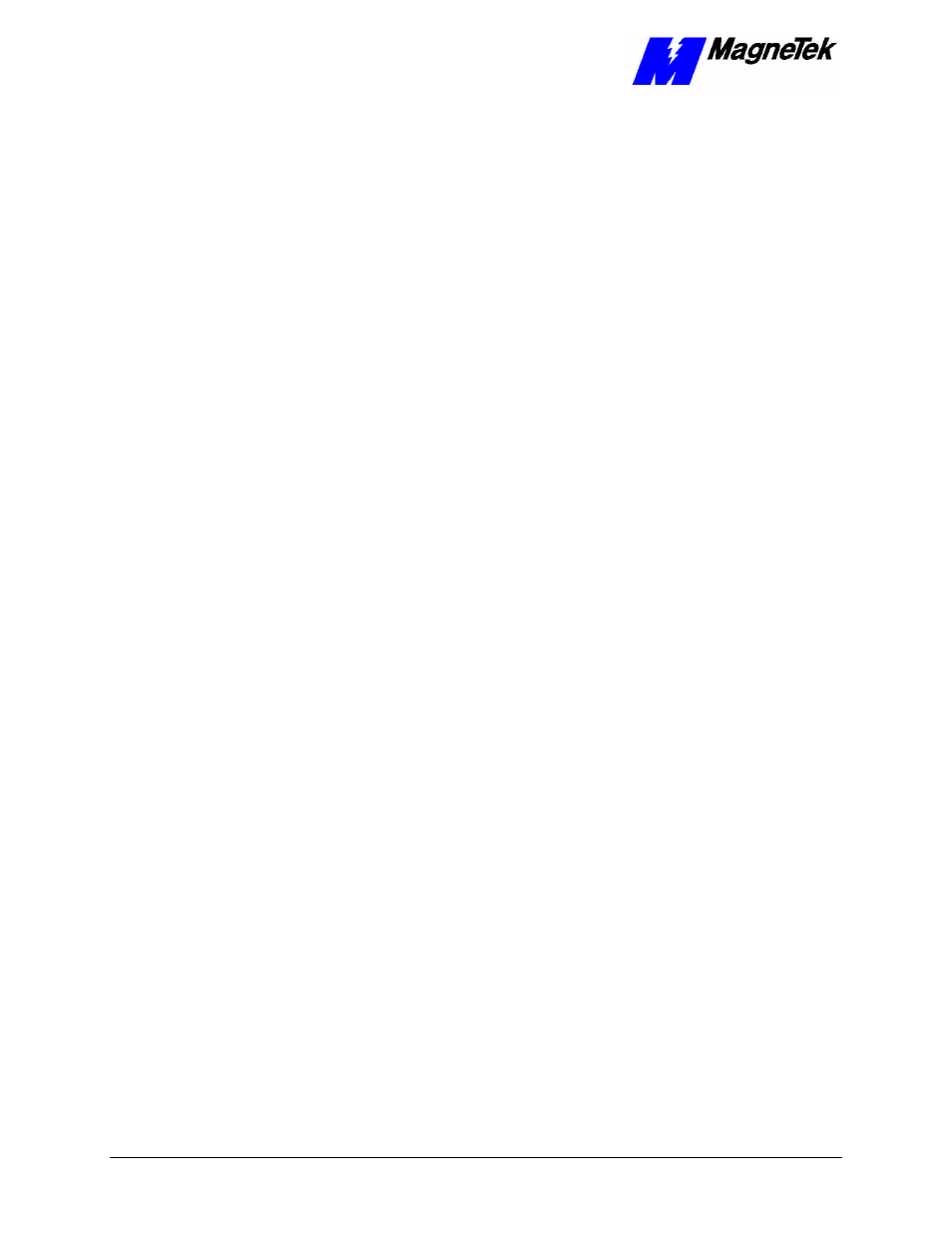
SMART TRAC AC1
8-8
••
Appendix C - Wiring, Grounding and Installation Practices for Noise ImmunityTechnical Manual TM 3554-000
•
Run separate steel conduit for power wiring to the drive input and the
drive output to the motor. Do not route input and output power wiring
together internal to the cabinet.
•
Never coil excess cable, whether in temporary wiring or final
installation wiring.
•
Ground wire must be provided from the motor case to panel ground in
addition to the required safety ground at the motor.
•
Excess cable should not be coiled. This applies to temporary wiring
and final installation. Wire length for a service loop is allowed for
maintenance purposes.
•
Low voltage signals such as analog inputs and outputs for speed or
torque control, digital inputs and outputs, and 24 VDC used for control
of the customers operating interface, should be run using shielded
cable, containing twisted pair(s).
•
Shields are connected to the drive shield connection. On a panel, the
shield is terminated to a terminal block. In the field, the external cable
shield is terminated to the terminal block, while the other end is usually
left unconnected.
•
Serial communication may be included with the low voltage wiring, or
routed in its own steel conduit.
•
A minimum three-inch bend radius for coax cables should be
maintained.
•
Stripping off signal wire insulation for termination should not result in
excessive exposed bare wire.
•
Electrical safety and improved mechanical capabilities require that the
terminals crimp on to the insulation on the back half of the terminal.
•
AMP or Thomas & Betts crimping tools are recommended. Crimping
tools must be used with the manufacturer recommended lugs, in
accordance with the manufacture’s usage guidelines.
•
The facility power ground should conform to the NEC, National
Electric Code for power distribution.
•
The chassis ground of the equipment and the conduit must be
connected to facility ground without creating ground loops.
•
If codes require grounding of the “Y” or “Star Point”
of the distribution
transformer, this should be connected directly to facility ground only.
•
Motor Encoder leads, encoder power and encoder output signals,
should be routed in their own steel conduit that does not contain power
or ac control wiring.
•
If necessary, the motor thermistor wiring may be included in the
conduit with the motor encoder leads. When doing so, a ferrite bead is
placed over the thermistor wires before they enter the conduit.
•
Separate conduit runs are required for Input Power, Output Power
(Motor), AC Control, and Low voltage.
•
Dynamic Braking wires are dc Bus voltage and switched at a very high
rate thus they need to be routed alone within their own conduit if
conduit is indicated.