Chopper module test procedure – Hypertherm HT200LHF-200 Volt HySpeed User Manual
Page 101
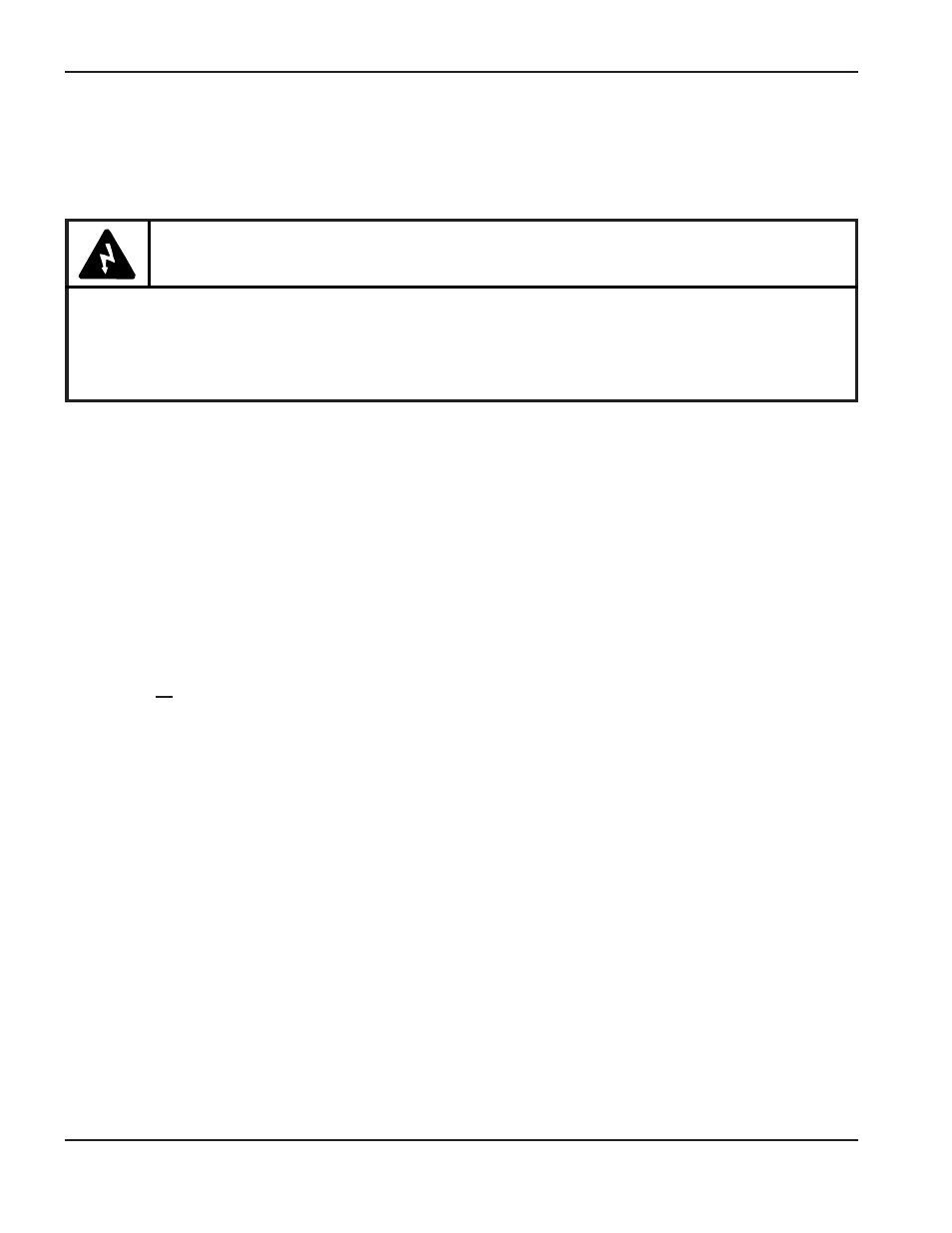
MAINTENANCE
5-12
HySpeed HT2000LHF
Instruction Manual
6
Chopper Module Test Procedure
Note: Take voltages with a digital multimeter capable of storing min. and max. readings.
1. Turn all power to the power supply OFF.
Disconnect the mating receptacles in the power supply to disable the high frequency transformer T3.
See Figure 6-7 for location of T3.
2. Remove large fuses F1 and F2. Check to see if the fuses are open.
3. Place the positive lead to the + side of the bridge and the negative lead to the – side of the bridge. See Figure
5-4. Note that actual connection points are hidden by cap support bracket in Figure 5-4.
4. Turn power to the power supply ON, and start the system up. After the START command has been given, check
the voltage. The input to the chopper at these points should be about +280 VDC. If the input is OK and
corresponding fuse F1 or F2 was blown, replace the chopper module.
If there is no +280 VDC input, check input to bridge for shorts. Also, check contactor (CON1), connections and
associated wiring to the contactor. Repair and/or replace defective component(s) if necessary.
5. If the voltage from above step is +280 VDC and corresponding fuse is not blown, check output of CH1 by
placing the positive lead of the voltmeter at point + WORK on the chopper module (wire #48A) and negative
lead at point - TORCH (wire #39A). (Check the output of CH2 by placing the leads of the voltmeter at the
corresponding points on the other chopper module.)
6. Turn the system on and press the START command. After the START command has been given, check the
voltage. If the output from each chopper at these points is +280 VDC, then the choppers are OK.
7. If the chopper does not output +280 VDC, check to see if the LED1 logic power light is illuminated. If LED1 is
extinguished, check if 120V is going to JP6. If there is no 120V at JP6, check wiring back to the power
distribution board. Repair or replace defective component(s), if necessary. Also check to see if LED3 is turning
green when enabled (normal condition). If LED1 is illuminated and LED3 is red when enabled (fault condition),
then make sure that JP9 is seated properly.
8. If the chopper still does not output 280V after completing step 7, there may be a problem with the control signal
or the chopper module. The chopper drive signal comes through the analog board PCB3 as an analog level
from 0 to +8 VDC, which varies the duty cycle and subsequent output current of the chopper. These analog
signals are on pins 3&4 REC1 of PCB3 for CH1, and 5&6 REC1 for CH2.
WARNING
SHOCK HAZARD: Use extreme care when working near the chopper modules. The large chopper
capacitors store large amounts of energy in the form of electric voltage. Even if the power is off,
dangerous voltages exist at the capacitor terminals, on the chopper, and the diode heatsinks.
Never discharge capacitors with a screwdriver or other implement…explosion, property damage
and/or personal injury will result.