19 thermal motor protection and overload responses, 1 thermal motor model – Watson-Marlow MM420 User Manual
Page 160
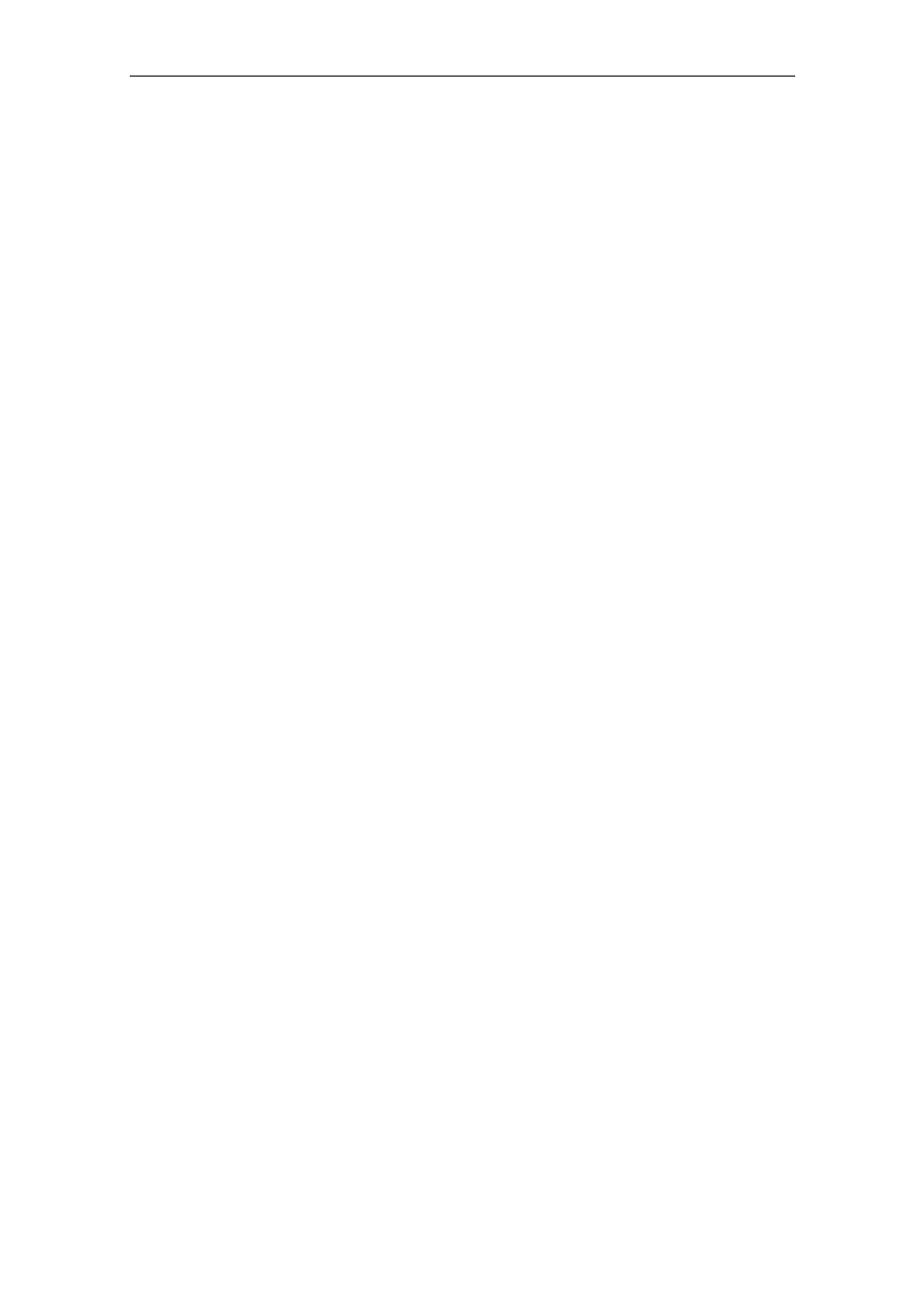
3 Functions
Issue 10/06
MICROMASTER 420 Operating Instructions
160
6SE6400-5AA00-0BP0
3.19
Thermal motor protection and overload responses
Parameter range:
P0610 – P0614
P0345
r
0034
Warnings A0511
Faults F0011
Function chart number:
-
MICROMASTER 420 has a completely new integrated concept for thermal motor
protection. There are numerous possibilities of effectively protecting the motor but
at the same time ensuring high motor utilization. The basic philosophy of this
innovative concept is to detect critical thermal states, output warnings and initiate
the appropriate responses. By responding to critical states it is possible to operate
the drive at the thermal power limit and to avoid, under all circumstances, an
immediate shutdown (where the drive inverter is tripped).
Features
The protective concept distinguishes itself as a result of the following individual
features:
Protection is effective without using any temperature sensor. The temperatures
of various locations in the motor are indirectly determined using a temperature
model.
Selectable responses P0610 which are to be initiated when the warning
threshold is exceeded in order to prevent an overload condition.
The motor protection has been designed to be completely independent of the
drive inverter protection. Warning thresholds and responses for drive inverter
protection must be separately parameterized.
3.19.1
Thermal motor model
The motor temperature rise increases because of the losses occurring during the
energy-conversion process in the motor. These losses can be essentially sub-
divided into two groups:
No-load losses
The no-load losses include the bearing and air friction losses as well as the re-
magnetizing losses (eddy current and hysteresis losses). All of these loss
components dependent on the speed and electrical frequency.
Load
losses
The load losses are mainly determined by the thermal losses in the windings
due to the current flowing through them.
An electrical motor represents a multi-material system (iron, copper, insulating
material, air) where the heat source is especially concentrated in the windings, the
laminated core and the shaft bearings. The following simplifications were made to
replicate the thermal processes in the motor:
The motor is a homogenous body
Heat sources are uniformly distributed in the motor
Heat is only dissipated using convection