Error code troubleshooting – 2 of 4 -16 – Hypertherm HD4070 Rev.1 User Manual
Page 179
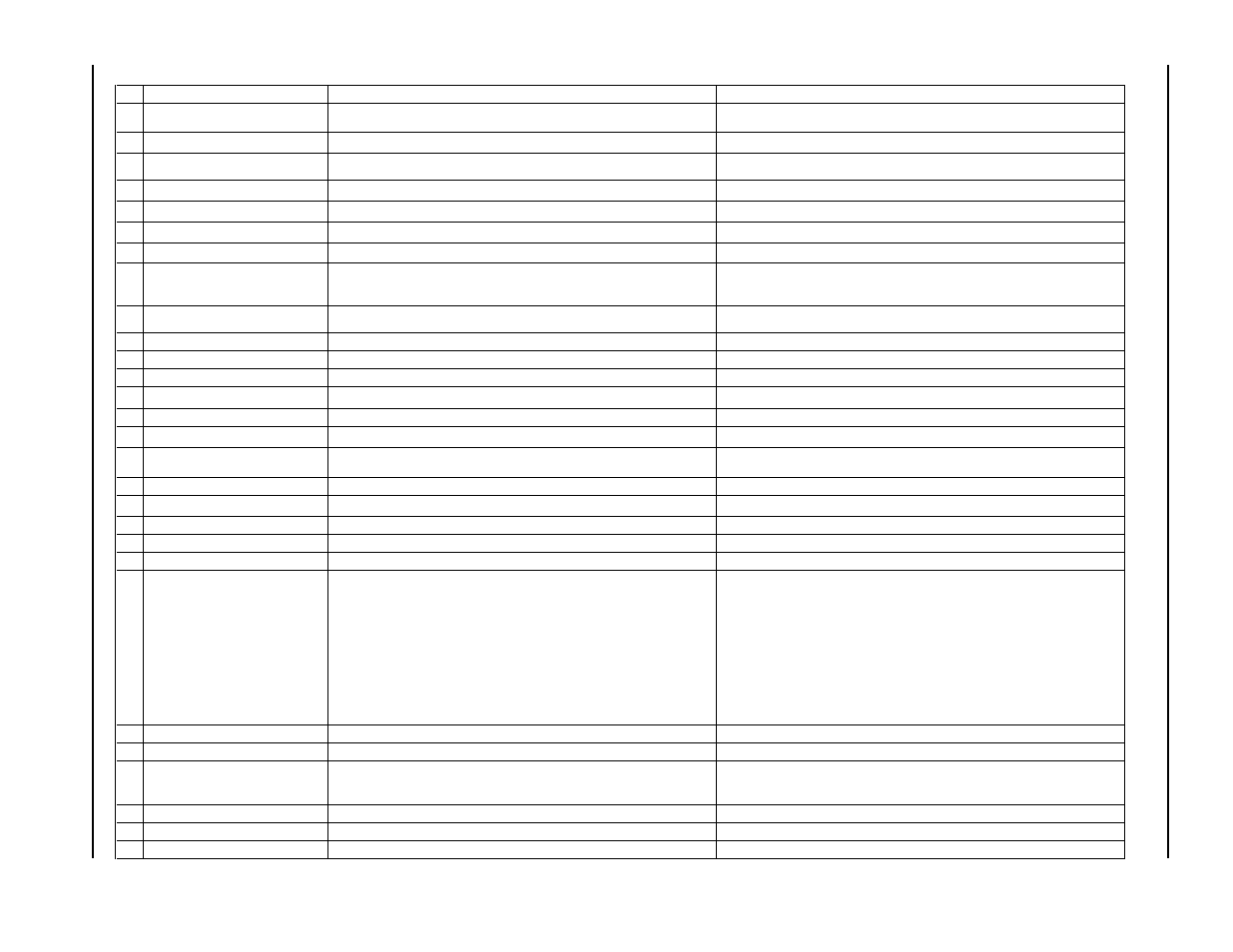
5-16
HyPerformance H
D4
0
70
Instruction Manual
MAINTENANCE
Error code troubleshooting – 2 of 4
ID #
Error Code or Message
Description
Corrective action
45 HIGH GAS PRESSURE
Gas pressure over 135psi (7.2Bar) detected. Interlock is tripped, the current
process is stopped and the arc is not allowed to fire.
Adjust supply gas pressure to specification. Recommend regulators be within 10
feet/3meters of gas console.
50 CYCLE START AT INIT
System was powered up while start command was coming from CNC.
Remove start signal. System will wait for next start command.
51 PILOT ARC OVERTEMP
Repeated, long pilot arcs have exceeded the thermal capacity of the pilot arc
controller.
Wait one minute for pilot arc controller to cool down.
52 NO PROCESS LOADED
The CNC has not selected a process.
Verify serial communication is working properly and select a process.
65 CHOPPER 1 OVERTEMP
Fans not working or vents are obstructed.
Make sure fans are operating and that the power supply vents are not obstructed.
66 CHOPPER 2 OVERTEMP
Fans not working or vents are obstructed.
Make sure fans are operating and that the power supply vents are not obstructed.
67 TRANSFORMER OVERTEMP
Fans not working or vents are obstructed.
Make sure fans are operating and that the power supply vents are not obstructed.
71 COOLANT OVERTEMP
Coolant temperature too high
(1) Check fan for operation. (2) Check coolant level. (3) Check for vent
obstructions. (4) Remove air from coolant loop, by following coolant servicing at
the beginning of this section.
80 CONTROL SYSTEM FAILURE
File corrupted, Faulty cable or Hard disk failure.
Run PC-104 test. See maintenence section.
81 CONTROL SYSTEM FAILURE
File corrupted, Faulty cable or Hard disk failure.
Run PC-104 test. See maintenence section.
82 CONTROL SYSTEM FAILURE
File corrupted, Faulty cable or Hard disk failure.
Run PC-104 test. See maintenence section.
83 CONTROL SYSTEM FAILURE
File corrupted, Faulty cable or Hard disk failure.
Run PC-104 test. See maintenence section.
84
CABLE TO GAS CONSOLE NOT
DETECTED
The cable is missing or not properly connected.
Check cable connections.
85 HARDDRIVE FAILURE
File corrupted, Faulty cable or Hard disk failure.
Not customer serviceable
86 HARDDRIVE FAILURE
File corrupted, Faulty cable or Hard disk failure.
Not customer serviceable
87 NO INPUT POWER DETECTED
Faulty control or breakout board.
(1) Verify all cables and wires for continuity. (2) Properly seat pins, sockets and
plugs. (3) Replace faulty control or breakout board.
88 CNC CABLE MISSING
Cable not connected or damaged.
Check power supply to CNC cable and connections.
89 FAIL TO OPEN FILE
File corrupted or hard disk failure.
Cycle power to clear error.
90 PROCESS INVALID FAIL
File containing process information is corrupt and not valid.
Reload the process file.
91 FAIL TO READ FILE
File corrupted or hard disk failure.
Cycle power to clear error.
92 FAIL TO WRITE FILE
File corrupted or hard disk failure.
Cycle power to clear error.
93 NO COOLANT FLOW
During normal operation, the system checks for coolant flow. After the coolant
pump has been turned on and the active torch has been selected, this error is
activated if the flow sensor does not indicate coolant flow within a 12 second
delay.
(1) Check that the torch head is installed. For two torch systems, check that either
the inactive torch or a dummy head is installed. (2) Check that the coolant tank
has enough coolant. (3) Check that the air has been purged from the coolant
lines. See Cooling System Servicing in the front of this section. (4) make sure
that the coolant lines are not obstructed or kinked. (5) Make sure that the proper
coolant select solenoid is energized. The torch #1 cooling solenoid is energized
from 120Vac output from the plasma interface board connector J6 pins 1 & 2.
Torch #1 output is indicated on the breakout board by LEDN 8-8. The torch #2
cooling solenoid is energized from 120Vac output from the plasma interface board
connector J6 pins 3 & 4. Torch #2 output is indicated on the breakout board by
LEDN 8-7. If the breakout board LEDN 8-8 is on (indicating coolant flow), check for
continuity across the coolant flow sensor output connections. If there is continuity
across the sensor output connections, replace the sensor. If LED D17 is ON and
there is no continuity across the sensor output connections, troubleshoot the plasm
94 DOOR INTERLOCK
Power supply access panel removed or loose.
Check that all panels are properly installed.
97 NO TORCH INTERFACE
THC#1 or THC#2 were not selected during set up.
Select one on the set up screen.
9 8 PHASE LOST AT INITIALIZATION
Phase loss sensor indicating that voltage is present at the chopper input
before the main contactor has been closed.
(1) Check that main contactor is open (2) Check phase loss sensor board. (3)
Check power supply control board. (See electrical PC boards and power supplies
in this section)
9 9 CHOPPER 1 OVERTEMP
Cable or sensor failure
(1) Make sure fans are working. (2) Blow out power supply.
1 0 0 CHOPPER 2 OVERTEMP
Cable or sensor failure
(1) Make sure fans are working. (2) Blow out power supply.
1 0 1 TRANSFORMER OVERTEMP
Cable or sensor failure
(1) Make sure fans are working. (2) Blow out power supply.
ID #'s 51-64: User must clear the error. Adjustments or changes must be made before cutting can continue.
ID #'s 65 & >: The error shuts the system off. The system needs to be reset or the power cycled before cutting can continue.