Off-valve assembly -3, Gas console -3, Ignition console -3 – Hypertherm HD4070 Rev.1 User Manual
Page 42: Options -3
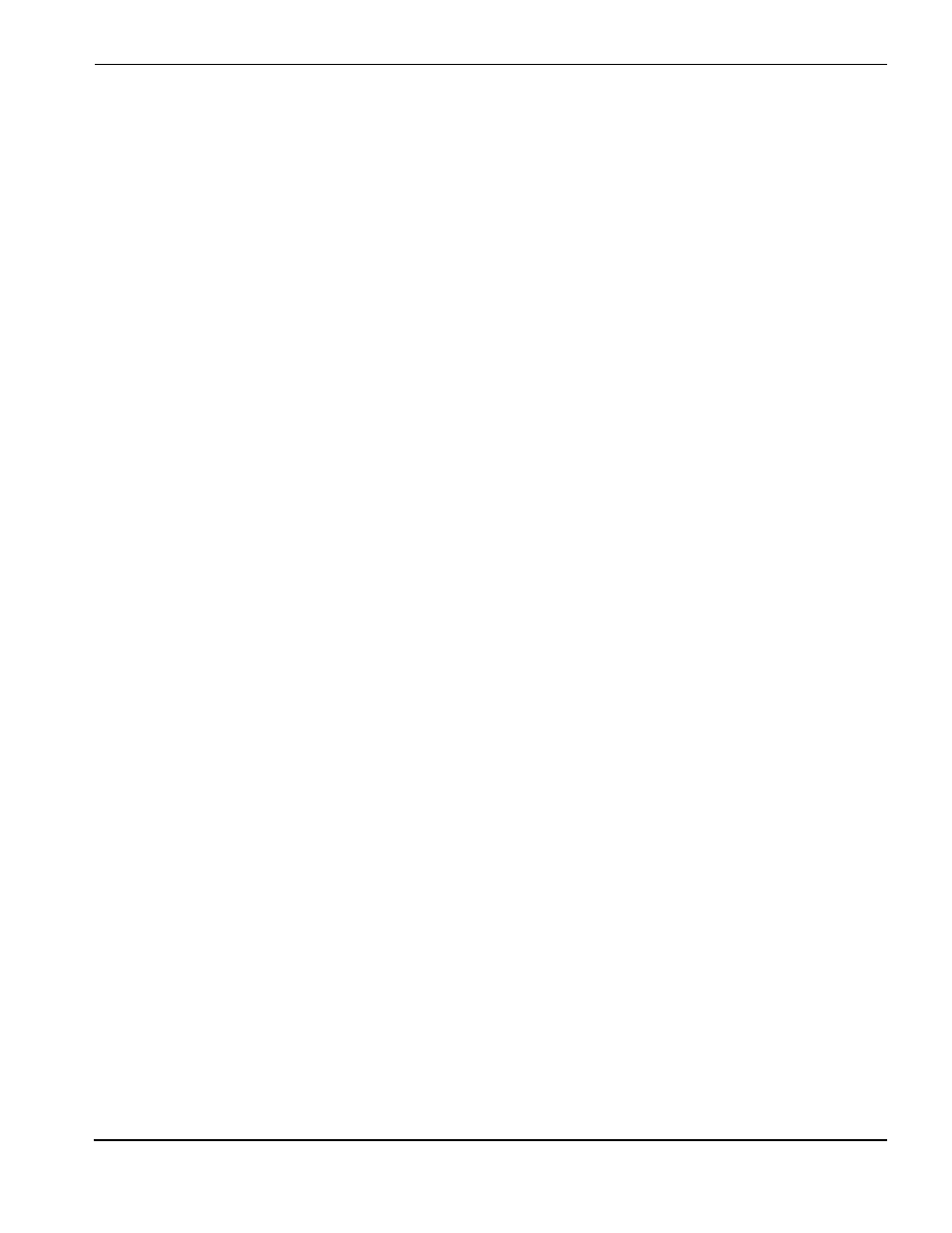
SPECIFICATIONS
HyPerformance HD4070
Instruction Manual
2-3
Off-valve assembly
The off-valve assembly consists of 5 solenoid valves, a manifold block and a wiring harness with connector. The
assembly interfaces with the machine torch, the ignition console and the gas console.
Gas console
The gas console manages all incoming gasses for selection and flow rate and is controlled by the HD4070 power
supply. The gas console includes motor valves, solenoid valves, check valves and pressure transducers, all
mounted on a single manifold assembly. The manifold significantly reduces gas leaks by eliminating the use of
flexible hose. The gas console also houses 2 relay PC boards and a control PC board.
Ignition console
The ignition console generates a high-voltage, high-frequency signal and couples it to the cathode lead and pilot
arc lead. The ignition console is fully electronic, eliminating the use of a spark gap assembly.
Options
• 2-torch option – The HD4070 plasma cutting system has the ability to support 2 torches operated from
a single power supply and gas console. When one torch is selected for cutting, the second torch is in
the off-mode. This allows operators to configure the system for 2 different processes (i.e. 100-amp
consumables installed in one torch and 200-amp consumables installed in the second torch), and to
select one torch or the other from the HD4070 display (or CNC).
Note:
A torch receptacle plug must be used if a two torch system is running in single torch mode.
Single torch mode is when a table is loaded with plate material and one torch is doing all
the cutting or marking. Dual torch mode is when one torch is performing one operation and
the second torch is performing another operation on the same plate material.
• Integrated CommandTHC option – The Hypertherm Integrated CommandTHC takes full advantage of the
HD4070’s automated capabilities. When the operator enters the material and thickness to be cut, using the
HD4070 display touch screen (or CNC), the Integrated CommandTHC automatically adjusts the torch
settings required for the specific process, including arc volts, torch-to-work distance, initial pierce height and
pierce time delay, using the plasma arc voltage to control the torch-to-work distance during cutting. IHS is
accomplished by ohmic contact sensing or by limited force stall detection. HD4070 power supplies that are
equipped with the Integrated CommandTHC option include the THC motor drive board, the THC control PC
board and THC power supply required for torch lifter operation and control.
• X-Y lifter assembly (page 2-12) The torch lifter station, under control of the THC control module,
positions a torch head vertically above the workpiece. Its maximum stroke is 8 inches (200 mm) between
the home and lower-limit switches. It is driven by a stepper motor attached to a leadscrew. An encoder is
provided for stall IHS sensing, and to detect gross errors during normal operation. A lower limit switch
detects maximum travel in the downward direction. A home switch is provided to detect when the lifter is
in the uppermost position. A power-off brake is energized after power-up, and allows controlled motion of
the torch. It is powered on during “Maintenance Mode” to prevent the torch from being accidentally
moved. An optional torch breakaway kit is available.
• Torch breakaway kit (optional page 2-13) The torch breakaway (collision sensor) provides a level of
protection for the torch, lifter and X-Y table. Air pressure locks the torch to the THC lifter assembly. The
air pressure can be adjusted to change the force required to trip the breakaway. Upon side impact, the
breakaway releases from the lock position and allows the torch to float. See page 2-12 for torch mounting
dimensions with and without the breakaway.